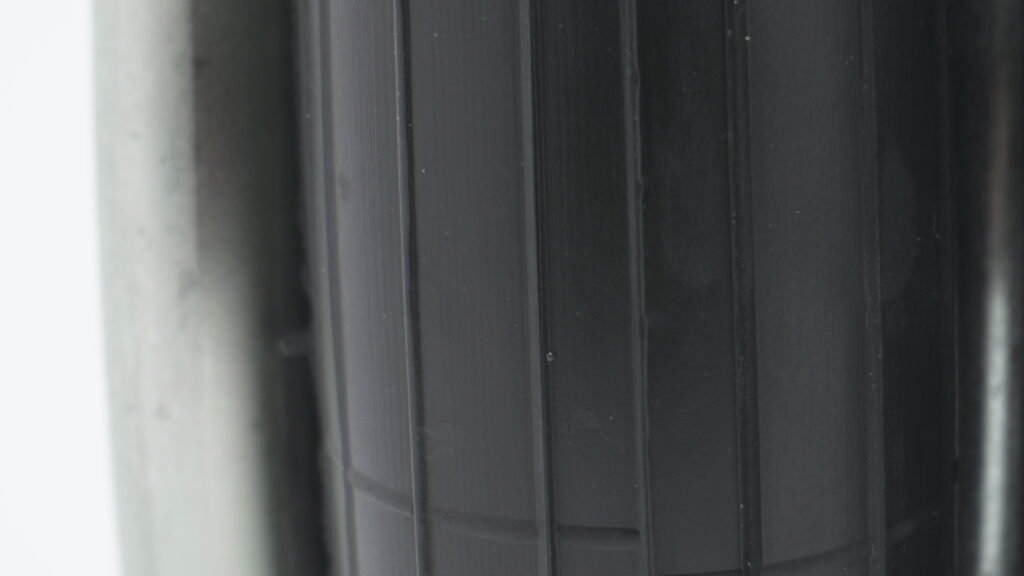
When selecting air bellows for industrial applications, one of the critical factors to consider is their chemical resistance. Different environments expose air bellows to various chemicals, oils, and extreme temperatures, which can affect their longevity and performance. Choosing the right elastomer compound ensures durability, reliability, and optimal function.
This article delves into the chemical resistance properties of the most commonly used air bellow materials, highlighting their strengths, limitations, and best-use scenarios. A thorough understanding of these aspects allows engineers and manufacturers to make informed decisions, reducing premature wear and increasing operational efficiency. Whether applied in automotive, industrial, marine, or heavy machinery, the right air bellow material can mean the difference between a short-lived component and long-term reliability. We will explore the best materials, their applications, and how to enhance air bellow longevity in chemically aggressive environments.
Key Factors Affecting Chemical Resistance
The chemical resistance of an air bellow depends on various aspects, including:
- Base polymer composition
- Reinforcing fabric layers
- Operating temperature range
- Exposure duration to chemicals
- Environmental conditions (UV, ozone, humidity)
Understanding these factors helps in selecting the right elastomer compound for air bellow applications in different industries. The chemical compatibility of a material is determined by its ability to withstand degradation when exposed to aggressive substances. For example, some materials exhibit excellent resistance to oils but degrade rapidly in acidic environments. Others perform well in high-temperature settings but may be susceptible to UV-induced aging. Additionally, the structural integrity of air bellows relies on the quality of reinforcement layers, such as fabric plies embedded between rubber compounds. These layers improve tensile strength and prevent early fatigue. A deeper analysis of these parameters ensures that the selected air bellow material offers optimal performance, even under extreme conditions. Choosing an inappropriate elastomer could lead to premature failure, increased downtime, and costly replacements.
Common Elastomer Compounds and Their Properties
1. Natural Rubber (NR/SBR)
- Excellent dynamic properties
- High flexibility and strength
- Moderate oil and chemical resistance
- Temperature range: -40°C to +70°C
- Best used for: Standard applications with minimal exposure to aggressive chemicals
Natural rubber-based air bellows offer superior mechanical strength and elasticity, making them ideal for applications requiring high shock absorption. However, NR/SBR compounds have limited resistance to oils, fuels, and harsh chemicals, making them unsuitable for hydraulic and automotive environments. The inclusion of styrene-butadiene rubber (SBR) enhances abrasion resistance and extends service life in moderate industrial applications. Despite their drawbacks, NR/SBR compounds remain widely used due to their cost-effectiveness and reliability in low-chemical-exposure settings. Engineers must assess specific environmental factors before choosing NR/SBR-based air bellows, ensuring they do not encounter conditions leading to premature degradation.
2. Chlorobutyl Rubber (CIIR)
- Superior resistance to acids
- Low gas permeability
- Excellent thermal stability
- Temperature range: -30°C to +115°C
- Best used for: Environments exposed to strong acids and industrial cleaning agents
CIIR-based air bellows excel in environments with acidic exposure and harsh chemical interactions. Their low permeability makes them highly effective in applications requiring airtight performance, such as pneumatic actuators and industrial sealing systems. Chlorobutyl rubber also offers exceptional heat resistance, preventing degradation under continuous high-temperature operations. Unlike NR/SBR compounds, CIIR retains flexibility even in extreme chemical settings, making it the material of choice for industries dealing with strong acids and reactive compounds. The superior aging properties of CIIR contribute to its longer operational lifespan, reducing the frequency of replacements and minimizing maintenance costs. However, CIIR has lower mechanical strength than some alternatives, necessitating reinforcement layers to improve durability in high-stress applications.
3. Nitrile Rubber (NBR)
- High resistance to oils and fuels
- Good abrasion resistance
- Moderate ozone and weather resistance
- Temperature range: -25°C to +110°C
- Best used for: Oil and fuel-rich environments such as automotive and hydraulic systems
NBR is one of the most commonly used elastomers for air bellows in oil-intensive environments. With high oil resistance, NBR-based air bellows maintain their structural integrity even when exposed to hydraulic fluids, fuel vapors, and lubricants. This makes them ideal for automotive suspension systems, industrial pumps, and hydraulic machinery. In addition to oil resistance, NBR offers good wear resistance, minimizing surface degradation from friction and mechanical stress. However, NBR is less effective in ozone-heavy conditions, as it lacks inherent UV stability. To mitigate this, manufacturers often blend NBR with reinforcing agents that enhance weathering properties. Industries requiring air bellows for oil-rich applications should prioritize NBR-based solutions, ensuring long-term reliability and resistance to fuel-induced deterioration.
Understanding the chemical resistance of modern air bellow materials is essential for ensuring optimal performance and longevity. By selecting the appropriate elastomer compound, industries can significantly improve reliability, reduce maintenance costs, and enhance operational efficiency. The right material choice ensures air bellows operate under demanding conditions without premature failure. Selecting a material that aligns with specific chemical exposures, temperature requirements, and operational loads extends the service life of air bellows. As industrial environments evolve, so does the need for durable, chemically resistant air bellows tailored for precise applications.