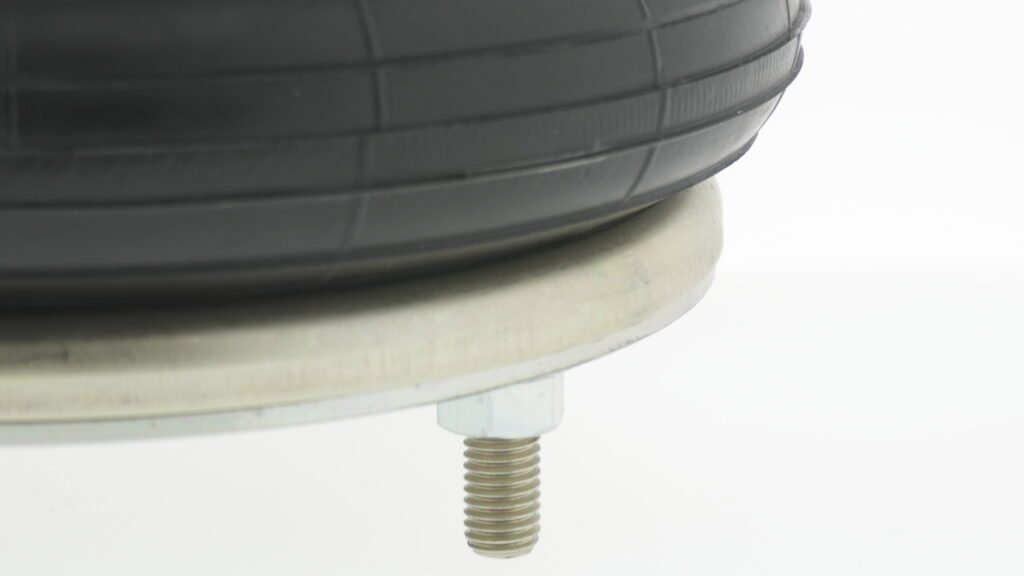
In our industry, optimizing the performance of air bellows is crucial for ensuring the longevity and efficiency of our systems. At Tevema, we understand the importance of proper setup and maintenance to achieve the best results. This article will guide you through the essential steps and considerations for enhancing air bellow performance.
Understanding Pressure and Return Mechanisms
To maximize the benefits of air bellows, it is essential to operate within the recommended pressure limits. Standard air springs should not exceed 8 bar pressure. For applications requiring higher pressure, we offer a four-ply construction capable of handling up to 12 bar. Remember, air springs are single-acting actuators and should never be used below atmospheric pressure. External loads must handle the return operation.
Operating within these pressure limits ensures the longevity and reliability of the air bellows. Over-pressurizing can lead to premature wear and potential failure, which can disrupt operations and increase maintenance costs. By adhering to the recommended pressure guidelines, we can maintain optimal performance and extend the service life of our air bellows.
Working Media and Safety Stops
Our air springs are designed to work with compressed air but can also use nitrogen, oil, water, and compressed air containing oil. When using water, ensure that stainless steel parts are used to prevent corrosion. Safety stops are vital to prevent the air actuator from exceeding its maximum allowable height or bottoming out. Flexible horizontal stops are recommended for full isolation effect.
Using the correct working media is crucial for the performance and durability of air bellows. Different media can have varying effects on the materials used in the construction of the bellows. For instance, using water without proper corrosion-resistant materials can lead to rust and degradation. Therefore, selecting the appropriate media and ensuring the use of compatible materials is essential for maintaining the integrity and functionality of the air bellows.
Support Area and Installation Space
A uniform load distribution is critical for the longevity of air bellows. Utilize the entire rubber actuator area or at least 65% of it. Ensure there are no sharp materials or surfaces that could damage the rubber bellow. Adequate clearance is necessary to avoid chafing at maximum diameter.
Proper installation space is another key factor in enhancing air bellow performance. The air bellows should be positioned correctly with sufficient space to operate without interference. This includes ensuring that there are no obstructions or sharp edges that could come into contact with the bellows during operation. By providing adequate clearance and a suitable support area, we can prevent damage and ensure smooth operation.
Elastomer Compounds and Metallic Parts
Choosing the right elastomer compound is essential for the specific application requirements. Options include:
- Natural (NR/SBR): -40° to +70°C, excellent universal properties.
- Clorobutyl (CIIR): -30° to +115°C, outstanding acid resistance.
- Nitrile (NBR): -25° to +110°C, excellent resistance to oils and fuels.
- Ethylene Propylene Diene (EPDM): -20° to +115°C, high temperature and ozone resistance.
- Chloroprene (CR): -20° to +110°C, good weathering resistance.
For metallic parts, we offer electro-galvanized steel and stainless steel options (AISI-304 and AISI-316L) for high wear resistance and durability.
Selecting the appropriate elastomer compound and metallic parts is crucial for the performance and longevity of air bellows. Each compound has specific properties that make it suitable for different operating conditions. For example, nitrile is excellent for applications involving oils and fuels, while EPDM is ideal for high-temperature environments. By choosing the right materials, we can ensure that the air bellows perform optimally under various conditions.
Auxiliary Reservoir and Tightening Torque
Adding an auxiliary reservoir can improve isolation by decreasing the natural frequency of the air spring. Ensure it is located close to the air spring with adequate flow in the connection pipes. Adhere to the recommended tightening torques for various fasteners to avoid over-tightening.
The auxiliary reservoir plays a significant role in enhancing the performance of air bellows. By increasing the volume, it helps in reducing the natural frequency, thereby improving the isolation rate. This is particularly beneficial in applications where vibration isolation is critical. Proper installation and connection of the auxiliary reservoir are essential to achieve the desired performance improvements.
Stability, Lateral Misalignment, and Angular Capability
For optimal stability, the distance between the narrowest points of the mounted air bellows should be at least twice the height from the center of gravity. Lateral misalignment capabilities vary by convolution type, with single convolution bellows allowing up to 10 mm and triple convolution up to 30 mm. The maximum tilt angle also depends on the convolution type, with double convolution bellows allowing up to 25°.
Stability is a crucial factor in the performance of air bellows. Ensuring that the air bellows are mounted correctly and that the distance between the narrowest points is adequate helps in minimizing wobbling and optimizing isolation. Additionally, understanding the lateral misalignment and angular capability of the air bellows allows us to design systems that can accommodate these movements without compromising performance.
Maintenance and Inspection
Regular maintenance is crucial for the longevity of air bellows. Clean the rubber bellow with water, soap, or alcohol, avoiding abrasives and organic solvents. Inspect the rubber bellow for wear, cracks, or damage, and check pneumatic components for any necessary replacements. Ensure all connections are tight but not over-tightened.
Maintenance is an ongoing process that involves regular inspection and cleaning of the air bellows. By keeping the rubber bellows clean and free from contaminants, we can prevent damage and extend their service life. Regular inspection helps in identifying any signs of wear or damage early, allowing for timely repairs or replacements. This proactive approach to maintenance ensures that the air bellows continue to perform optimally.
By following these guidelines, we can significantly enhance the performance and lifespan of our air bellows. Proper setup, regular maintenance, and choosing the right materials are key to achieving optimal results. At Tevema, we are committed to providing high-quality air bellows and support to ensure the success of your applications.