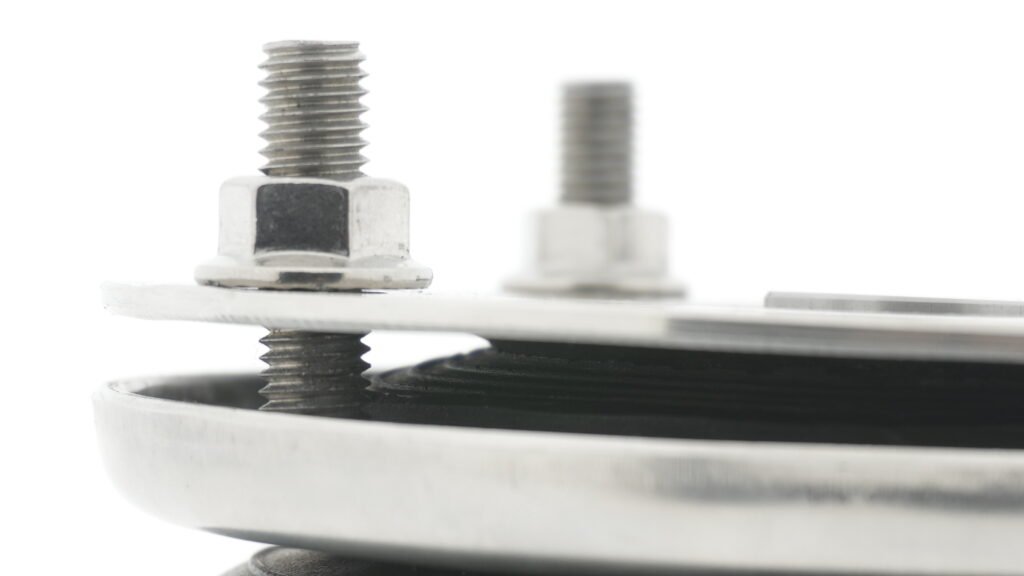
Enhancing Operational Efficiency with Air Bellows
Industrial air bellows play a crucial role in optimizing energy efficiency across multiple sectors. By leveraging their flexible design and high durability, businesses can reduce energy consumption while maintaining superior performance. Air bellows are widely used for vibration isolation, actuation, and load support, making them a versatile solution for industrial applications. The maximum allowable pressure for standard air bellows is 8 bar, but high-strength models can handle 12 bar. These units provide stroke lengths up to 375 mm, enabling extended actuation. With an operational temperature range of -40°C to +115°C, they work in diverse industrial environments. The integration of four-ply reinforced construction increases durability under high-load conditions, ensuring extended service life. Stainless steel end plates, available in AISI-304 and AISI-316L, enhance corrosion resistance in harsh environments. These specifications ensure maximum operational reliability and energy efficiency.
Reducing Energy Waste Through Advanced Design
One of the primary advantages of air bellows is their ability to minimize energy losses. Unlike conventional mechanical springs or hydraulic systems, air bellows operate with compressed air, ensuring minimal friction losses. Their low natural frequency and high damping capacity allow them to absorb excessive vibrations, reducing the energy required for machine maintenance and operation. The natural frequency of air bellows ranges between 1.2 Hz and 3.9 Hz, depending on size and configuration. This ensures effective vibration absorption while minimizing transmitted forces. Air bellows with crimped-end closures provide leak-free operation, preventing air loss and unnecessary energy consumption. Bead-ring models allow for easy disassembly and reassembly, reducing downtime and improving operational flexibility. With self-adjusting pressure mechanisms, air bellows maintain a consistent height under variable loads, optimizing energy use. Their modular designs allow for customization, making them ideal for applications requiring specific stroke lengths and load capacities.
Vibration Isolation for Increased Energy Efficiency
Excessive vibrations in industrial equipment can lead to energy waste, increased wear, and higher maintenance costs. Air bellows act as superior vibration isolators, absorbing mechanical shocks and reducing structural fatigue. This results in:
- Reduced downtime due to fewer mechanical failures.
- Lower energy expenditure by eliminating unnecessary oscillations.
- Extended machinery lifespan, reducing replacement costs.
The vibration isolation efficiency of air bellows exceeds 99%, making them one of the most effective solutions on the market. Load capacities range from 0.5 kN to 450 kN per unit, ensuring compatibility with diverse industrial setups. Operating heights can be regulated precisely, allowing optimal performance in applications requiring constant height adjustments. Multiple convolution designs, including single, double, and triple convolutions, provide varying degrees of flexibility and stroke lengths. These properties contribute to the reduction of structural stress and lower overall energy consumption.
Air Bellows as Energy-Efficient Actuators
Unlike hydraulic and pneumatic cylinders, air bellows provide efficient actuation with low air pressure requirements. Their lightweight construction reduces the need for high-pressure compressors, leading to lower operational costs. Key benefits include:
- Soft, controlled motion, reducing sudden energy surges.
- No lubrication required, eliminating additional power consumption.
- High load capacity with minimal energy input.
With stroke ranges between 20 mm and 375 mm, air bellows accommodate various industrial applications. Their low air consumption rates make them an energy-efficient alternative to traditional cylinders. The frictionless operation ensures consistent performance, eliminating issues related to wear and tear. Tilting capabilities up to 25 degrees allow for angular adjustments without additional components. Their compact height, starting from 50 mm, enables installation in space-constrained areas. Corrosion-resistant materials further increase longevity, reducing replacement cycles and promoting energy efficiency. The operational lifespan of air bellows surpasses that of traditional actuators, making them a cost-effective and sustainable solution.
Customization for Maximum Efficiency
Industries benefit from tailor-made air bellows that fit specific operational needs. Custom designs include:
- Multiple convolution options for precise motion control.
- Reinforced materials for extreme conditions.
- Optimized mounting configurations for efficient energy transfer.
Customization ensures that air bellows can handle specific load requirements, enhancing energy efficiency. Variable mounting options, including top and bottom plates with threaded or blind nut fittings, offer secure installation. The choice of elastomers, such as natural rubber (NR), nitrile rubber (NBR), or ethylene propylene diene monomer (EPDM), allows adaptation to harsh environments. Special coatings, including anti-ozone and anti-oil treatments, further extend service life. These adaptations enhance performance reliability, making air bellows a preferred solution for industries requiring low-energy, high-performance actuators and isolators.
Implementing air bellows in industrial settings is a strategic move toward energy efficiency, cost reduction, and improved equipment longevity. Their ability to adapt, isolate vibrations, and provide efficient actuation makes them an essential component in modern industrial processes. By incorporating reinforced elastomers, optimized pressure control, and custom mounting solutions, industries achieve maximum energy efficiency. Air bellows provide a sustainable alternative to traditional mechanical systems, reducing energy waste and ensuring long-term reliability. With their proven durability, cost-effectiveness, and operational flexibility, they remain a cornerstone of modern industrial automation.