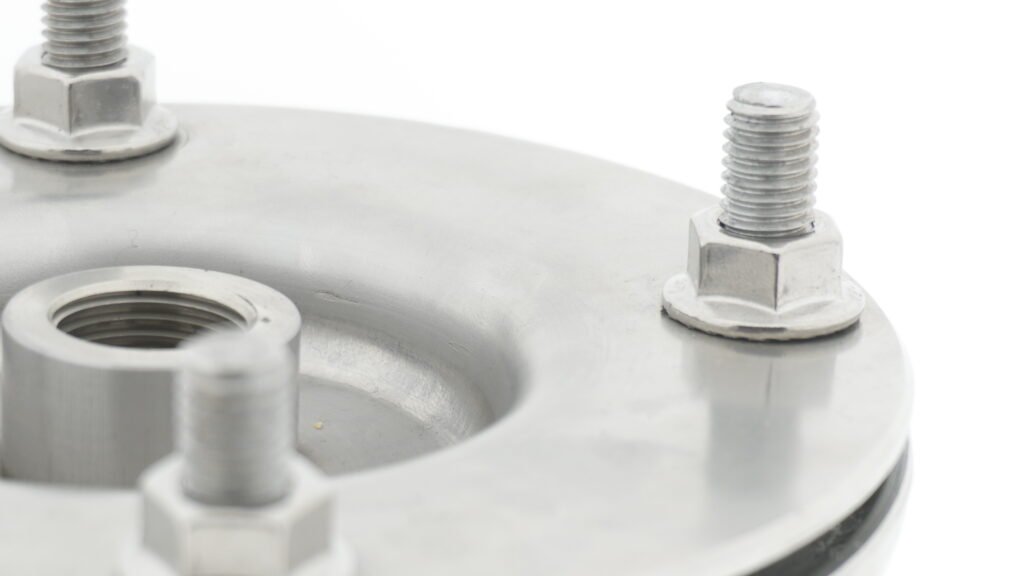
The Importance of Air Bellows Maintenance
Ensuring optimal performance and longevity of air bellows in industrial applications requires structured maintenance protocols. Factory managers must be equipped with the necessary knowledge to prevent unexpected downtime, optimize operational efficiency, and extend the lifespan of their air suspension systems.
Air bellows play a critical role in industrial machinery by absorbing vibrations and providing cushioning for heavy loads. These components operate under pressures up to 8 bar, with some high-strength variants capable of handling up to 12 bar. They are made from reinforced rubber compounds like natural rubber (NR/SBR) or chlorobutyl (CIIR), which offer excellent resistance against extreme temperatures, acids, and oils. Understanding these material properties helps managers make informed maintenance decisions that improve reliability and minimize replacement costs.
Common Issues with Air Bellows and How to Prevent Them
Regular inspections help in identifying potential failures before they cause major disruptions. Key issues include:
- Air leaks due to worn-out seals and improper pressure regulation.
- Structural fatigue caused by continuous exposure to high loads and vibrations.
- Misalignment leading to uneven wear and inefficient energy absorption.
- Contamination from debris, oil residue, and excessive moisture.
Preventative measures, such as routine checks, pressure monitoring, and proper installation, significantly improve reliability and efficiency. Factory managers should monitor for cracks, deformation, and surface wear using thermal imaging tools and ultrasonic leak detectors. Some advanced models feature internal reinforcement layers designed to withstand high frequencies of compression and decompression, reducing fatigue-related failures. Additionally, using stainless steel end plates instead of standard galvanized steel provides better corrosion resistance in high-humidity environments.
Key Components of an Air Bellows Maintenance Seminar
A well-structured air bellows maintenance seminar provides factory managers with:
- Hands-on training on detecting early signs of wear using advanced diagnostic tools.
- Best practices for installation, including correct torque settings for securing mounting hardware.
- Pressure management techniques to ensure consistent performance across different operational cycles.
- Case studies illustrating common failure scenarios, their causes, and practical solutions.
Training also includes an in-depth review of air bellow specifications, such as maximum stroke range, load-bearing capacity, and compression limits. Some bellows offer adjustable height configurations, enabling precise load balancing and vibration isolation in dynamic industrial environments. Understanding force-displacement curves and resonance frequencies ensures that bellows are used effectively to absorb shocks without overloading adjacent components.
Choosing the Right Training Program for Your Team
Selecting a reputable provider with industry expertise is essential. Factors to consider include:
- Comprehensive curriculum covering both theory and practical training.
- Experienced trainers with extensive industrial air suspension knowledge.
- Customizable content to address specific factory requirements.
- Post-training support for continuous improvement.
Factory managers should seek training providers that include on-site assessments and customized workshops tailored to their specific operational needs. Programs offering certifications ensure that participants gain recognizable industry credentials. Effective training also covers emergency response planning, ensuring teams know how to handle sudden air system failures with minimal production downtime. Manufacturers that integrate predictive maintenance techniques, such as real-time monitoring sensors, enhance their competitive edge by reducing unexpected failures.
Long-Term Benefits of Proper Air Bellows Maintenance
A proactive maintenance approach leads to:
- Reduced operational costs by minimizing repair expenses and extending component service life.
- Extended equipment lifespan, ensuring a higher return on investment through optimal efficiency.
- Improved safety through better system stability and load distribution.
- Consistent product quality by maintaining optimal performance and avoiding uneven vibrations.
Investing in maintenance training ensures that managers understand air bellows operational dynamics, including maximum load ratings, temperature tolerances, and expected cycle durability. Properly maintained bellows prevent excessive energy loss, enhance shock absorption, and contribute to energy efficiency improvements in automated production lines. Many modern bellows are designed with multiple convolution structures, allowing them to flex more effectively under variable loads without failure. This extends lifespan and reduces the need for frequent replacements.
Investing in air bellows maintenance seminars is a strategic move for factory managers aiming to optimize their operations. With structured training, preventative measures, and proper installation techniques, facilities can achieve maximum efficiency and minimal downtime.
Air bellows are critical for ensuring stable production cycles in heavy industrial settings. Proper knowledge of installation torque settings, pressure adjustments, and seal inspections ensures that they operate efficiently under varying environmental conditions. Training programs should focus on predictive maintenance technologies, allowing early detection of potential failures before they become costly problems. Incorporating sensor-based monitoring systems into maintenance schedules ensures long-term operational stability and cost efficiency.