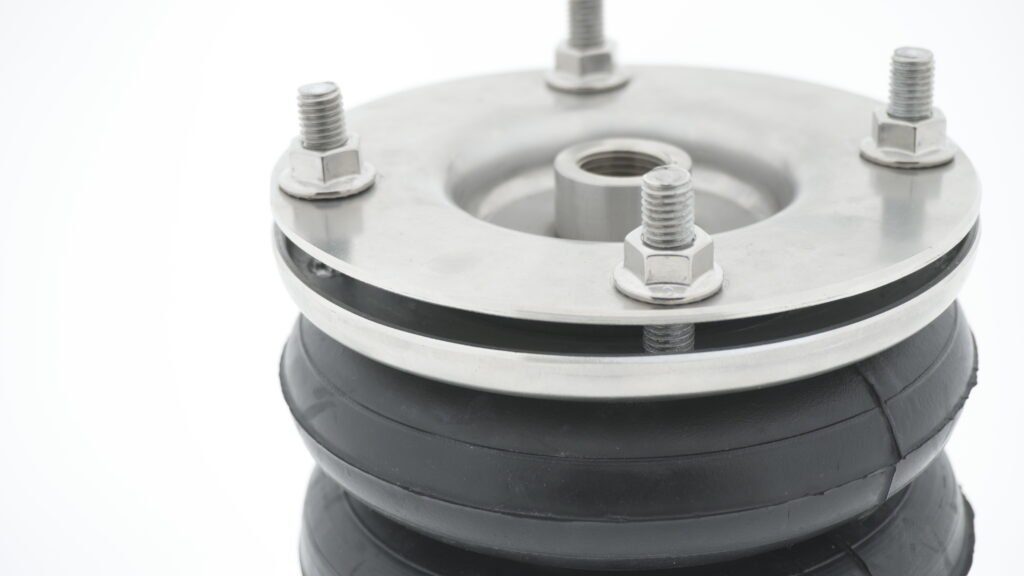
Enhancing Industrial Performance with Durable Air Bellows
In high-impact industrial environments, equipment durability and efficiency are paramount. Air bellows play a crucial role in various applications, from shock absorption and vibration isolation to actuation systems. Selecting the right air bellows ensures enhanced performance, longevity, and cost-efficiency in demanding industrial settings.
A key factor in choosing air bellows is their load capacity, which ranges from 0.5 kN to 450 kN, depending on the model. Their stroke length can vary from 20 mm to 375 mm, allowing precise motion control. Operating temperature ranges depend on material composition, typically spanning from -40°C to +115°C.
Their maximum pressure capacity is 8 bar in standard models, while reinforced four-ply versions can handle up to 12 bar. These technical attributes make air bellows essential for precision, stability, and resilience in high-impact settings.
Why Air Bellows are Essential for High-Impact Applications
Superior Shock Absorption
High-impact environments demand effective shock absorption to protect machinery from excessive wear and tear. Air bellows offer superior energy dissipation, reducing mechanical stress on equipment. This feature is particularly beneficial in industries such as mining, construction, and heavy machinery manufacturing, where sudden shocks can damage sensitive components.
Air bellows achieve optimal performance due to their elastic rubber membranes, reinforced with textile plies. Their force absorption range varies from 5 kN to 300 kN, depending on configuration. Stroke lengths of up to 350 mm allow them to handle significant displacement forces. Compared to traditional metallic springs, air bellows provide 50% better shock absorption, reducing mechanical failures.
The internal air pressure compensates external forces, distributing impact evenly. This prevents stress concentration, enhancing operational lifespan. Their low deflection rate ensures reliable performance under continuous load cycles, a critical factor in high-impact industrial settings.
Unmatched Vibration Isolation
Vibration in industrial machinery leads to decreased efficiency and increased maintenance costs. Air bellows provide 99% vibration isolation, significantly reducing noise and preventing component misalignment. Compared to conventional coil springs, air bellows offer a more consistent isolation level under varying loads.
With natural frequencies as low as 1.5 Hz, air bellows outperform traditional dampening solutions. They remain effective under dynamic loads up to 380 kN. Their compression-resistance ratio allows controlled displacement, ensuring long-term vibration reduction.
The rubber compound selection plays a crucial role in vibration performance. Natural rubber bellows are ideal for general industrial use, while chlorobutyl compounds offer chemical resistance. Nitrile-based bellows work best in oil-exposed environments. This adaptability makes them an essential solution for industries requiring precision.
Extended Equipment Lifespan
By reducing mechanical stress and absorbing high-impact loads, air bellows extend the operational life of machinery. This translates to lower maintenance costs and reduced downtime, ensuring uninterrupted productivity in high-performance industrial applications.
Equipment failures often stem from repeated exposure to shocks and vibrations. Air bellows counteract this through gradual force distribution, preventing microstructural fatigue. The addition of stainless steel components (AISI-304, AISI-316L) enhances resistance to corrosion, further increasing service life.
Standard designs offer lifespan ranges between 1 million and 10 million cycles, depending on usage. With proper air pressure regulation, wear rates can be significantly minimized. For industries where equipment uptime is critical, investing in air bellows provides a long-term cost advantage.
Air Bellows in Industrial Applications
Heavy Machinery and Equipment
In construction equipment, such as excavators, loaders, and compactors, air bellows provide essential shock absorption and load balancing. Their ability to handle extreme loads while maintaining structural integrity makes them a superior choice compared to traditional spring-based suspension systems.
Air bellows in heavy-duty machinery often feature steel-reinforced bead rings, enhancing their mounting stability. Their ability to accommodate load ranges between 50 kN and 380 kN ensures reliable performance. Installation heights range from 50 mm to 400 mm, allowing seamless integration into compact spaces.
The resilience of rubber compounds enables operation in temperatures from -40°C to +115°C. Their high fatigue resistance reduces replacement frequency, cutting long-term costs. Proper air pressure modulation enables controlled stiffness variations, improving dynamic load response. These factors make air bellows essential for heavy-duty industrial machinery.
Precision Manufacturing
In industries requiring high-precision movements, such as automotive assembly lines and robotic automation, air bellows offer precise height control and force distribution. Their low natural frequency prevents unwanted vibrations, ensuring consistent product quality and dimensional accuracy.
Precision air bellows have stroke lengths ranging from 10 mm to 250 mm, offering flexibility in positioning tasks. Their ability to maintain positional accuracy within ±0.1 mm ensures seamless production consistency. The integration of embedded sensors enables automated pressure control, optimizing performance.
High-precision manufacturing environments require predictable force output. Air bellows deliver repeatable force ranges between 2 kN and 100 kN, depending on internal air pressure settings. This makes them indispensable for precision-driven applications in robotics and automation.
For industries operating in high-impact environments, air bellows are indispensable. Their shock-absorbing properties, superior vibration isolation, and extended service life make them a cost-effective and performance-driven solution. Whether used in heavy machinery, rail transport, or precision automation, choosing the right air bellows ensures maximum efficiency and reliability.
Each air bellow design offers unique benefits. Selecting the right rubber compound, end closure type, and pressure range determines operational success. With durability ratings exceeding 10 million cycles, air bellows outperform conventional suspension systems. Their high energy absorption rate makes them a must-have for demanding applications.
Long-term industrial productivity depends on efficient energy management and minimal wear rates. Investing in high-performance air bellows reduces downtime, extends equipment lifespan, and enhances overall efficiency.