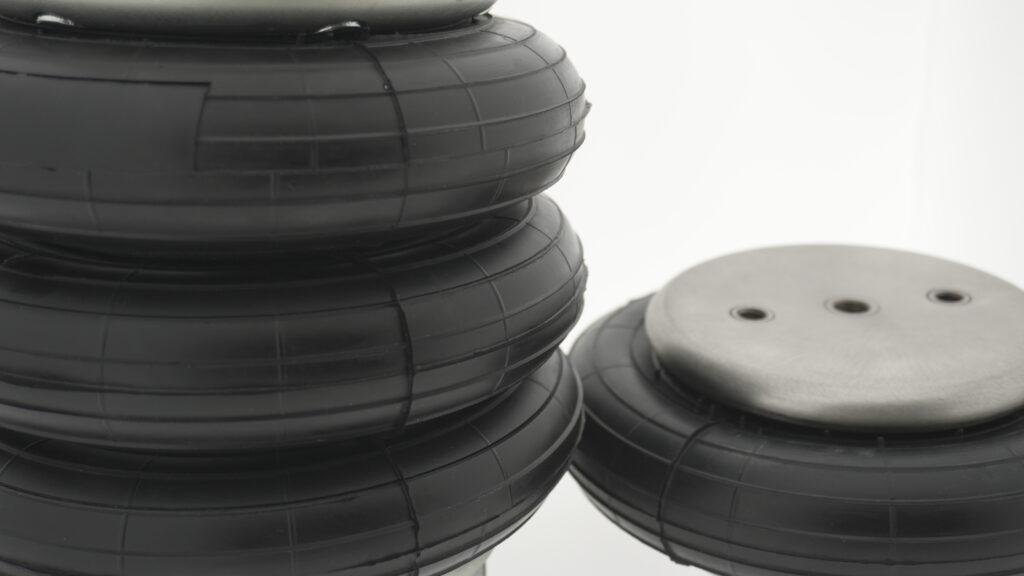
In our day-to-day engineering practice, we’ve seen how worn-out air bellows can silently compromise the performance of industrial systems. Left unchecked, a single damaged rubber bellow can jeopardize load stability, vibration isolation, or actuating precision. Our goal in this guide is to help you detect signs of degradation early and guide you through safe, effective replacement of industrial air bellows. When it comes to rubber-based components, aging is inevitable. However, by understanding the design tolerances, material fatigue thresholds, and pressure handling limits, we can minimize risks and keep systems running smoothly. This article outlines the steps to spot and replace degraded bellows without interrupting productivity. A standard single convolution bellow has a minimum height of 50 mm and a maximum stroke of 85 mm. Triple convolution types can handle up to 375 mm of vertical movement, depending on the diameter and pressure.
Spotting the early signs of worn-out air bellows
We often encounter issues where flexible actuators or rubber isolators underperform due to subtle deterioration. The first indicators include loss of height control, abnormal deflection, or inconsistent force output. Additionally, micro-cracks in the rubber surface or separation at bead rings signal mechanical fatigue. Routine visual inspections can uncover these early signs. We look for rubber blistering, fading elastomer surface, or air seepage marks near threaded ports. Any of these suggest the unit may have reached its load cycle lifespan. Frequent use in high-pressure environments, especially above 8 bar, accelerates wear. A common single convolution model offers 10.1 kN at 7 bar; any drop in output is cause for concern. Misalignment stress and exposure to chemicals also degrade polymer integrity, especially in bellows made from natural rubber or nitrile compounds. If left unaddressed, these issues evolve into dangerous ruptures, compromising safety.
Key performance parameters to monitor
To maintain reliable operation, we regularly track several technical performance indicators. These include force at operating pressure, stroke consistency, and vibration damping efficiency. Any shift in these values may indicate an issue. A declining natural frequency is a red flag in vibration isolation systems. For example, if a bellow’s frequency at 6 bar drops below design specs (often around 2.5 Hz), it no longer isolates efficiently. Similarly, actuators with incomplete strokes may indicate internal air leaks or layer delamination. A typical rubber bellow should maintain 44.4 kN at 7 bar if rated for that output. Measuring stroke displacement against nominal specs helps confirm the bellow still meets its design range. A drop in actuating force may also signal a worn internal structure. Always compare against manufacturer data from the original product sheet. These parameters are key to assessing whether replacement is needed.
Understanding failure modes of industrial air bellows
Knowing why air bellows fail helps us prevent recurrence. In our experience, common causes include material fatigue, chemical degradation, abrasion, and improper installation. Repeated flexing, especially at maximum stroke, causes rubber cracking. Chemically aggressive environments damage elastomer layers, particularly when incompatible materials are used. For example, nitrile rubber resists oils well, but fails in acidic conditions—making chlorobutyl or EPDM better alternatives in such cases. Likewise, stainless bead rings are a must in water or cleaning-agent exposure. Misaligned mounting points can twist the bellow, leading to torsional strain. Poorly aligned fasteners or uneven surface contact leads to premature wear at sealing interfaces. A standard bellow working with 12 bar pressure in four-ply construction must be installed carefully to avoid early failure. Over time, this causes loss of pressure retention and even rupture under load. Monitoring these conditions is essential for long-term reliability.
Criteria for determining when to replace air bellows
We advise replacing air bellows when any of the following is observed: Surface cracks exceeding 2 mm depth. Loss of original stroke length beyond 10%. Measurable air leakage during static pressure hold. Visible separation at bead ring joints. Permanent deformation under no-load conditions. Additionally, if the bellow reaches its maximum rated cycles or shows any sign of rubber fatigue, a replacement is prudent. For systems requiring consistent height control, a minor shift can cause significant process instability. A bellow originally rated at 69 kN force should not drop below 62 kN under the same conditions. Always refer to your application’s load specifications and compare with current performance data. Subpar output at rated pressure indicates the need for replacement. Make sure that safety margins are maintained in systems using multi-convolution bellows to support dynamic loads.
Choosing the right replacement air bellow
When selecting a replacement, we consider the convolution type (single, double, triple), pressure rating, and material compatibility. It’s also essential to match mounting threads, end plate designs, and stroke lengths precisely. Tevema offers air bellows in both D Series and F Series, supporting standard industrial mounting types. We recommend reviewing the original bellow’s dimensions—diameter, height, port size, and fixation points—before sourcing a match. For harsh conditions, opt for versions with AISI-304 stainless steel end plates or chlorobutyl elastomer compounds. These variants resist chemical corrosion, temperature extremes, and ozone aging. In high-load applications, four-ply construction models are ideal. A proper match will restore functionality and prolong service life. Double convolution models, for instance, should provide 27 kN at 7 bar. Always verify specs before final installation.
Steps for safe removal of worn air bellows
Before removing any pressurized component, we ensure the system is shut down and fully depressurized. Using a locking mechanism, we secure the axis to prevent accidental motion. Our next steps include: 1. Disconnect air supply and any linked automation control. 2. Remove bolts or studs from top and bottom plates. 3. Detach air ports and sensor connectors if applicable. 4. Gently twist and lift the bellow to avoid deforming adjacent parts. 5. Clean all mating surfaces before installing the new unit. We caution against using metal tools that can scratch sealing surfaces. Instead, use non-marring tools to detach the unit. For systems with bead ring configurations, ensure the correct torque settings are applied during reassembly. A typical torque value for bead rings is between 20 Nm and 40 Nm, depending on thread size.
Installing the new air bellow correctly
Proper installation ensures a long service life. We begin by aligning the mounting holes and air inlet ports exactly. A misaligned unit creates uneven loading and accelerates elastomer wear. Apply a non-hardening sealant to air fittings. Mount the unit using manufacturer-recommended torque settings to prevent over-compression. Make sure the bellow is not under tension or compression in the rest state. Once secured, connect the air supply lines and perform a leak test at working pressure. Observe for any hissing sounds, pressure drops, or unexpected movement. If clear, cycle the unit through a few test strokes and verify smooth operation. When replacing multi-convolution types, ensure all rings and intermediate spacers are properly aligned. Skipping alignment will cause functional imbalance. If using four-ply construction, verify air inlet port sealing can handle pressures up to 12 bar. Record torque values for future maintenance tracking.
Common pitfalls to avoid during air bellow replacement
One common mistake we see is failing to match the correct bellow size or connection type. This leads to improper seating, air leaks, or complete system failure. Avoid reusing old mounting hardware, as worn fasteners compromise torque retention. Another issue is over-tightening clamps, which cuts into the rubber and shortens lifespan. Always follow tightening torque guidelines. Using lubricants incompatible with the rubber material can also cause chemical swelling. Never operate the system before confirming proper installation and leak-tight sealing. Check for angular misalignment, as it introduces side loads that damage the bellow over time. Also, avoid introducing sharp debris during assembly. Lastly, always verify that media compatibility aligns with the new bellow’s elastomer compound. For example, don’t use natural rubber bellows in oil-saturated environments. Triple convolution bellows must be supported on flat surfaces to avoid uncontrolled lateral movement during compression.
Post-replacement performance validation
After installation, we conduct a full performance validation to confirm optimal function. This involves: Checking stroke range against design specs. Monitoring force output at 7 bar. Validating vibration isolation with frequency meters. Inspecting air seals under static and dynamic pressure. For isolator applications, we test that vibration transfer is reduced by at least 99%, confirming the rubber isolation efficiency. For actuator roles, we verify consistent and smooth movement across strokes. We also re-calibrate systems requiring height control or load compensation. These adjustments ensure the new bellow works in harmony with existing components. Periodic post-installation checks improve long-term performance. Using maintenance-free air springs not only reduces downtime but also contributes to safer, more stable operation. Measure ambient temperature and humidity during tests to ensure optimal environmental conditions. Ensure stroke measurements are within 5% of technical specification values noted in the design data.
Summary: ensuring air bellow longevity
By identifying issues early and replacing worn-out air bellows correctly, we ensure maximum system uptime and safety. Whether it’s through regular inspection or smart component selection, our maintenance strategy revolves around proactive care. Replacing air bellows isn’t just about fixing a problem—it’s about restoring precision, isolation performance, and actuator control. By choosing the right materials, matching configurations, and following installation best practices, we extend the life of the equipment and improve operational efficiency. Document replacement dates, pressure levels, and performance benchmarks to maintain a historical log for future analysis. This is how we maintain the highest standards in industrial motion and vibration control.