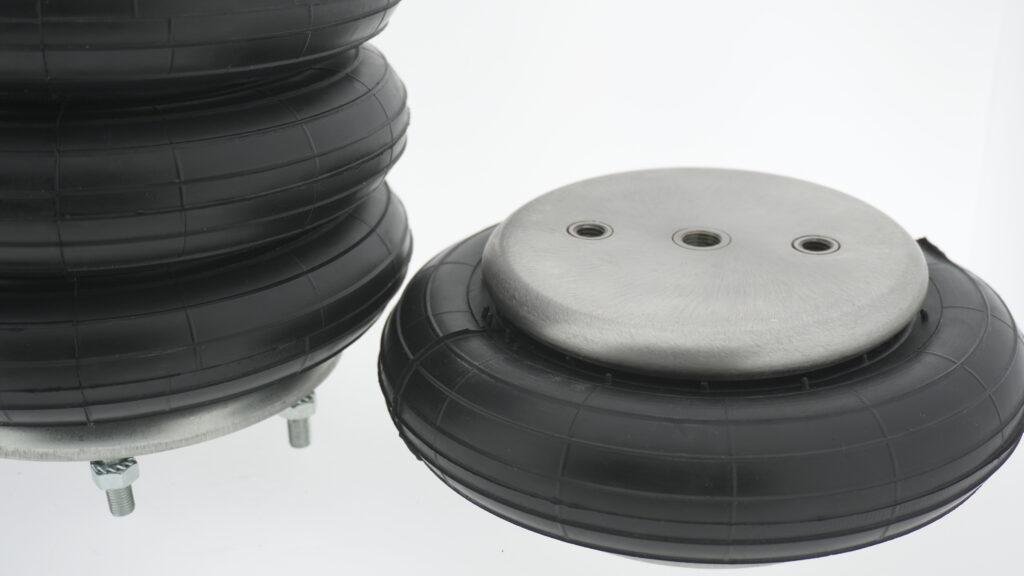
Precision and reliability in medical applications
In the field of medical device manufacturing, precision and reliability are non-negotiable. The integration of air bellows into medical equipment enhances efficiency, durability, and operational consistency. Due to their compact design, flexibility, and ability to operate without mechanical friction, air bellows provide an optimal solution for a variety of medical industry applications.
Standard air bellows models feature single, double, and triple convolutions, each with varying load capacities. The single convolution type offers a low-profile design, ideal for applications requiring short stroke lengths and high-pressure resistance. Double and triple convolution models allow for extended stroke ranges, supporting more flexible movement with increased force capacity. The typical operating pressure for standard configurations ranges between 6 and 12 bar, depending on the material composition and reinforcement layers used in the design. Additional features include electro-galvanized mounting plates and optional stainless-steel variants, ensuring corrosion resistance in medical environments.

Enhancing movement control in medical devices
In medical automation, the need for precise force control and smooth motion is critical. Air bellows provide exceptional actuation properties, allowing controlled movements without the drawbacks of metallic springs or hydraulic systems. The ability to absorb vibrations and maintain consistent pressure output makes them ideal for applications such as:
- Surgical robots requiring delicate pressure adjustments
- Patient positioning systems for adjustable hospital beds
- Diagnostic imaging devices where vibration isolation is essential
- Lab automation equipment needing precise actuation
The flexibility of air bellows allows for lateral displacement, which is often necessary in robotic-assisted surgical systems. The maximum lateral misalignment tolerance varies but typically falls within 25–30 mm, allowing for safe and reliable movement compensation. With a low static friction coefficient, these components ensure uniform force application in critical medical applications. Their compact height also allows easy integration into space-restricted setups.
Vibration isolation for sensitive medical equipment
Medical environments rely on equipment that must operate without external vibration interference. The high shock absorption and low natural frequency of air bellows make them indispensable in reducing structural vibrations. This is particularly important for high-precision diagnostic tools, including:
- MRI scanners that require an ultra-stable platform
- CT machines that must minimize motion-related distortions
- Microscopes and laser surgery tools needing absolute stability
The natural frequency of air bellows typically ranges from 1.5 to 3 Hz, ensuring maximum vibration isolation. This low-frequency range allows for a 99% reduction in transmitted vibrations, outperforming standard rubber dampers. When paired with pressure-regulated height control systems, air bellows ensure consistent level adjustments to counteract external environmental shifts. Their temperature-resistant materials allow operation under extreme lab conditions, enhancing reliability.
High-performance materials for medical environments
In the healthcare sector, the materials used in manufacturing must meet strict hygiene and durability standards. Air bellows are designed using high-performance elastomers and reinforced rubber, ensuring resistance to:
- Chemical exposure (disinfectants, sterilization agents)
- Extreme temperatures in autoclave conditions
- Long-term wear under continuous use
- Ozone and UV degradation, ensuring longevity in sterilized environments
Common elastomers include:
- Chlorobutyl (CIIR) – Excellent acid resistance and high-temperature performance.
- Nitrile (NBR) – Superior oil and fuel resistance.
- EPDM (Ethylene Propylene Diene Monomer) – Exceptional ozone and weather resistance.
Standard air bellows are reinforced with multiple fabric layers, usually two to four plies, providing added durability. A four-ply construction allows for increased pressure handling, reaching up to 12 bar while maintaining optimal elasticity. The outer rubber layers resist degradation from continuous exposure to sterilization chemicals.
Maintenance-free operation for medical efficiency
Unlike mechanical springs or hydraulic actuators, air bellows offer maintenance-free operation. This reduces operational costs in hospitals, laboratories, and production facilities by eliminating:
- Lubrication requirements
- Component wear due to friction
- Frequent part replacements
Their long service life ensures maximum reliability, making them a preferred choice in high-demand medical settings. Due to their corrosion-resistant metal components, air bellows maintain their integrity in humid or chemically aggressive environments. Most configurations include electro-galvanized or stainless-steel mounting plates, ensuring long-term durability in sterile conditions. Their self-cleaning properties make them particularly useful in operating rooms and contamination-sensitive environments.
Compact installation with high force output
Modern medical devices demand space-saving solutions without compromising performance. The compact height and high-force capability of air bellows allow for high load capacity while occupying minimal space. This is crucial in:
- Portable medical devices
- Automated diagnostic machines
- Patient support systems requiring compact yet powerful actuation
The typical installation height for single convolution bellows ranges between 50 and 150 mm, depending on the diameter and construction type. Double and triple convolution models extend the stroke range up to 375 mm, supporting greater motion flexibility in confined spaces. The maximum force output at 7 bar pressure reaches up to 450 kN, making these components suitable for high-load applications. Their pressure-regulated adaptability allows for customized force distribution, ensuring patient safety.
Safe and controlled pressure regulation
Medical applications often require precise pressure adjustments. Air bellows allow fine-tuned pressure control, ensuring a stable and predictable response under varying loads. This is essential in:
- Medical-grade air cushions for patient support
- Compression therapy devices
- Dosing and metering systems in medical labs
By integrating real-time pressure monitoring, air bellows can automatically adjust load distribution, preventing uneven force application. Standard configurations include G1/4” to G3/4” air inlets, allowing for seamless connection to medical-grade compressed air systems. This ensures consistent pressure delivery, crucial for maintaining patient comfort and medical accuracy.
Advancing medical technology with air bellows
The integration of air bellows in medical device manufacturing offers significant advantages, including precision actuation, vibration isolation, and long-term reliability. With their maintenance-free operation, high force capacity, and compact design, they continue to be an indispensable component in advanced medical technology. Customizable configurations allow for tailored solutions, ensuring compatibility with diverse medical applications where precision and durability are paramount.