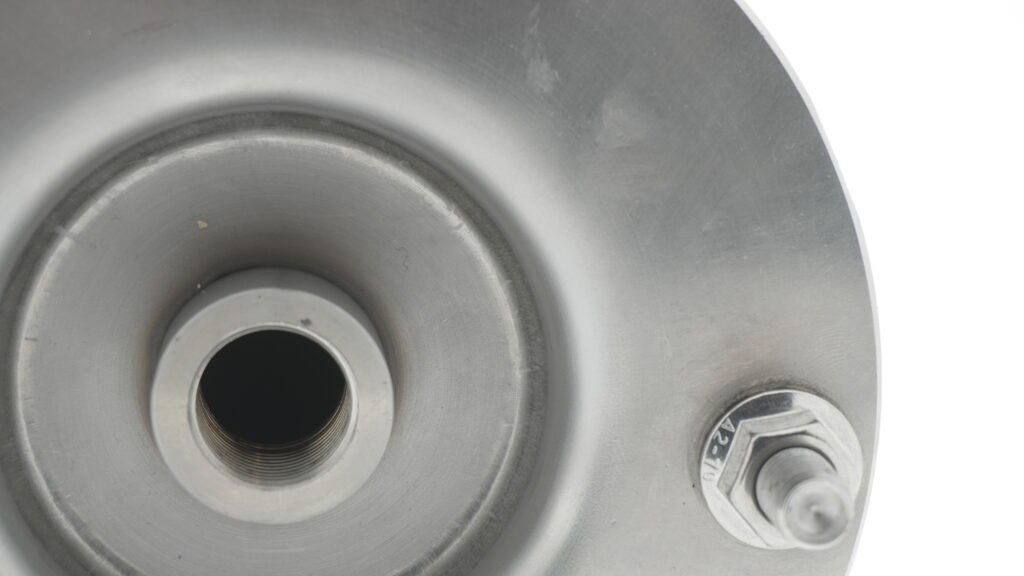
Understanding the Role of Air Bellows in Vibration Control
When it comes to industrial vibration isolation, air bellows play a crucial role in protecting equipment, ensuring longevity, and improving operational efficiency. The effectiveness of air springs depends on factors such as load capacity, frequency isolation, and durability. Selecting the right air bellows requires a technical understanding of how they function within specific applications. Tevema’s air bellows offer multiple design options, including single, double, and triple convolution models. Each of these configurations has different stroke lengths, load-bearing capacities, and frequency response characteristics.
The load-bearing capacity ranges from 0.5 kN to 450 kN, depending on the model and construction. The stroke lengths vary between 50 mm and 400 mm, ensuring adaptability for different industrial settings. Natural frequencies start as low as 1.5 Hz, making them ideal for precision vibration isolation applications. These specifications help industries achieve stable machine operation and extended component longevity.
Key Factors in Selecting the Best Air Bellows
1. Load Capacity and Weight Distribution
One of the most important considerations is the load-bearing capacity. The ability of an air bellow to support a load depends on its maximum force resistance at a given pressure. Tevema’s air bellows come in various sizes and pressure ratings, allowing for optimal load distribution.
- Single convolution bellows: Ideal for applications with limited height requirements.
- Double convolution bellows: Provide increased stroke and flexibility.
- Triple convolution bellows: Suitable for heavy-duty vibration isolation.
Each Tevema air spring can handle pressures up to 8 bar, with reinforced models capable of withstanding up to 12 bar. The elastic behavior of the rubberized structure enables them to withstand lateral displacements of up to 30 mm, while maintaining uniform force distribution.
2. Natural Frequency and Vibration Isolation
For effective vibration damping, choosing an air spring with the correct natural frequency is essential. Lower frequencies result in superior vibration isolation. Tevema’s air bellows achieve more than 99% vibration absorption, reducing the impact of oscillations on machinery and infrastructure.
- High-frequency vibrations: Require bellows with lower natural frequency.
- Low-frequency vibrations: Need precision tuning to avoid resonance.
The natural frequency of Tevema air bellows starts at 1.5 Hz and can be adjusted by modifying internal air pressure. Rubber bellows with larger diameters and triple convolutions offer the lowest frequencies, ensuring optimal isolation for sensitive equipment.
3. Material and Durability
Air bellows must be made from high-quality rubber compounds and reinforced materials to withstand harsh environments. Tevema offers air springs in natural rubber (NR/SBR), nitrile (NBR), and EPDM, each suited for different industrial conditions:
- NR/SBR: General-purpose with excellent dynamic properties.
- NBR: High resistance to oils and fuels.
- EPDM: Ideal for extreme temperature fluctuations.
The temperature range of Tevema’s air springs spans from -40°C to +115°C, depending on the elastomer type. Stainless steel variants are available for chemical and corrosive environments, ensuring prolonged durability and minimal maintenance.
4. Pressure Ratings and Stroke Requirements
Each air bellow has a maximum pressure rating that determines its force output. Standard air bellows operate at 8 bar, but reinforced versions can handle up to 12 bar.
- Short stroke applications: Require high-pressure bellows.
- Long stroke applications: Benefit from larger convolutions for increased flexibility.
Tevema’s air springs offer strokes ranging from 20 mm to 400 mm, ensuring flexibility for various industrial applications. The ability to operate at higher pressures increases the generated force, making them suitable for heavy machinery and precision tools.
5. Mounting and Installation Considerations
Proper installation ensures maximum performance and longevity. Tevema’s air bellows are designed with various mounting options:
- Dismountable bead ring design: Allows for easy maintenance and replacement.
- Crimped end plates: Ensure a permanent and secure fit.
- Bead ring assembly: Provides direct mounting to machinery without additional plates.
Common Applications of Air Bellows in Vibration Control
1. Industrial Machinery Isolation
Air bellows significantly reduce vibrational impact in machinery such as presses, compressors, and pumps. They help prevent structural damage, improve accuracy, and enhance operational efficiency.
2. Precision Equipment Support
In industries like semiconductor manufacturing and metrology, precise isolation is critical. Tevema’s air bellows provide a stable platform with minimal vibration interference.
3. Vehicle Suspension Systems
Air bellows are widely used in commercial trucks, buses, and railway suspension systems to enhance ride comfort and stability.
4. Foundation Isolation for Buildings
Buildings in seismic zones benefit from air bellows as they absorb ground vibrations, reducing structural damage risks.
Benefits of Using Air Bellows for Vibration Control
- Extended equipment lifespan by minimizing vibration-related wear.
- Adjustable stiffness via air pressure modifications.
- Superior load distribution, reducing stress points.
- Low maintenance due to the absence of friction-based wear components.
- Cost-effective alternative to complex mechanical vibration control systems.
Selecting the right air bellows for vibration control involves analyzing load capacity, frequency isolation, material durability, and pressure ratings. Tevema’s air springs offer high-performance solutions tailored for diverse applications. By choosing the correct air spring, industries can enhance efficiency, improve precision, and extend the lifespan of machinery and structures.