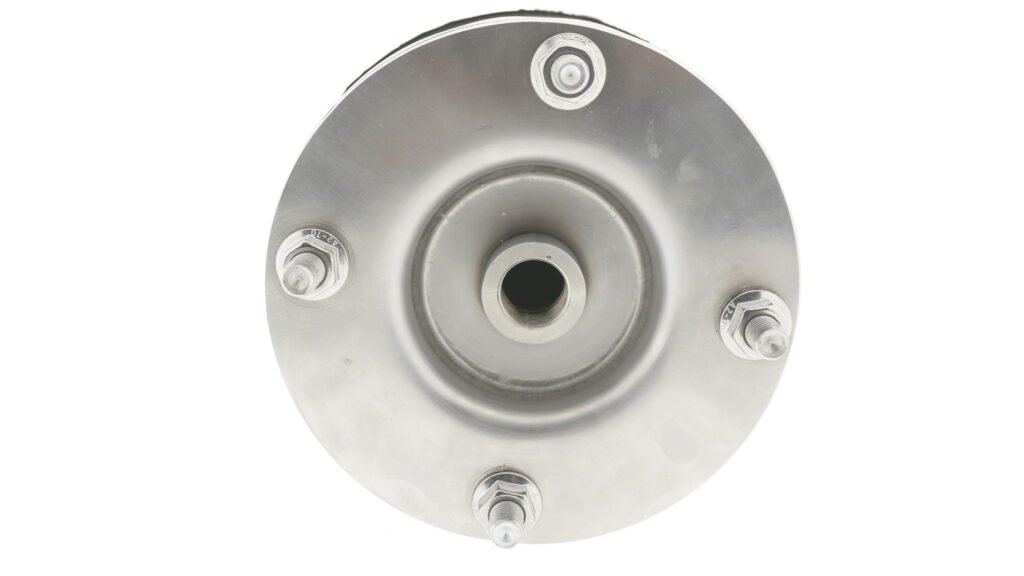
When considering air bellows as an alternative to hydraulic or mechanical springs, the benefits are clear. They offer exceptional load adaptability, superior vibration isolation, and enhanced durability in industrial applications. Unlike traditional suspension systems, air bellows provide an innovative solution that improves performance, efficiency, and longevity. With an operating pressure range of up to 12 bar, they can handle significant loads while maintaining their structural integrity. The temperature resistance spans from -40°C to +115°C, depending on the elastomer compound used. This ensures optimal functionality in extreme environments. Their maximum stroke capability reaches 375 mm, which makes them suitable for applications requiring significant displacement. The use of four-ply reinforced rubber construction in some models allows for increased durability under demanding conditions. Compact designs with diameters from 80 mm to 950 mm cater to diverse industrial needs.
1. Superior Vibration Isolation
One of the standout advantages of air bellows is their ability to absorb and isolate vibrations better than hydraulic or mechanical springs. With their rubber construction and air cushioning properties, these components can isolate up to 99% of unwanted vibrations, significantly reducing machine wear and noise levels. This leads to improved operational efficiency and prolonged equipment lifespan. Traditional springs transmit high levels of vibration, which increases mechanical fatigue. Air bellows operate at a natural frequency as low as 1.5 Hz, ensuring superior damping. When subjected to shock loads, they distribute force evenly, preventing localized stress concentrations. Their ability to support loads from 0.5 kN to 450 kN makes them suitable for both light and heavy industrial applications. Unlike rigid solutions, their flexibility absorbs shocks dynamically, reducing wear on machine components. The result is higher efficiency, lower energy consumption, and improved precision in motion control systems.
2. Adjustable Load Capacity
Air bellows excel in situations requiring variable load handling. By adjusting the internal air pressure, they can easily adapt to different weight requirements without the need for mechanical adjustments. This provides industries with versatility in operational setups. Traditional mechanical springs require pre-calculated settings and lack real-time adaptability. Air bellows adjust automatically, ensuring optimal force distribution across varying loads. Their load-bearing capacity ranges from 5 kN to 1,800 kN, allowing them to support both light and heavy machinery. Integrated height control systems ensure constant working heights, preventing misalignment issues common in mechanical setups. Their compact height ranges from 50 mm to 140 mm, making them ideal for space-constrained applications. They eliminate overload conditions by evenly distributing weight, reducing excessive force on machinery components. This prolongs equipment life, minimizes maintenance costs, and enhances system reliability. Lowering or raising pressure modifies stiffness, making fine-tuning quick and efficient.
3. Compact Design and Space Efficiency
Compared to bulky hydraulic cylinders or mechanical springs, air bellows offer a low-profile, compact design that allows for installation in restricted spaces. Their design height ranges between 50 mm and 279 mm, accommodating both low-clearance and high-travel applications. Traditional hydraulic actuators require additional fluid reservoirs, increasing system complexity. Air bellows eliminate this need, simplifying the overall setup. Their lightweight construction—comprising reinforced rubber with high-strength steel end plates—makes installation easier. A wide range of mounting options, including stud, threaded hole, or clamping bead rings, enhances compatibility with different machinery. Compared to mechanical alternatives, air bellows reduce total system weight by up to 40%, resulting in improved energy efficiency. In robotic applications, where every gram matters, this advantage is significant. Their ability to function in dynamic and high-speed environments without mechanical degradation makes them an ideal solution. Customization options for specialized geometries further improve adaptability.
4. Extended Product Lifespan and Low Maintenance
The absence of sliding seals and moving metal components makes air bellows highly durable. Unlike hydraulic systems, which require regular oil changes and seal replacements, air bellows are virtually maintenance-free. Traditional systems with metallic parts suffer from wear due to constant friction and exposure to contaminants. Air bellows require minimal upkeep, reducing downtime and operational costs. Their resistance to oil, water, and chemical exposure makes them suitable for harsh environments. With a typical lifespan exceeding 1 million cycles, they outperform conventional alternatives. High-performance elastomers such as EPDM, NBR, and chlorobutyl ensure resistance to environmental factors. Electro-galvanized or stainless steel end plates provide corrosion resistance, increasing longevity. Routine visual inspection suffices for long-term performance assurance. Their non-corrosive nature minimizes oxidation risks, making them ideal for marine, chemical, and food-grade applications. No lubrication required, meaning significant cost savings over years of operation.
5. Customization and Versatility
Unlike traditional springs with fixed parameters, air bellows can be customized to match specific force and stroke requirements. Available in single, double, and triple convolution designs, they cater to a wide range of motion applications. Diameters range from 80 mm to 950 mm, covering diverse industrial needs. Their angular motion capability of up to 25° allows for complex motion control. Unlike rigid alternatives, their high degree of lateral flexibility compensates for misalignment issues. Mounting configurations include crimped, bead ring, and dismountable plate types, ensuring integration into multiple systems. Industries such as automotive, aerospace, and heavy-duty manufacturing benefit from their adaptability. Air bellows operate efficiently at altitudes exceeding 3,000 meters, ensuring performance in extreme environments. They also withstand temperatures from -40°C to +115°C, making them ideal for both subzero and high-heat conditions. Their ability to function across various industries underscores their unmatched versatility.
6. Improved Safety and Reliability
Hydraulic systems can suffer from leaks and pressure failures, while mechanical springs are prone to fatigue. Air bellows eliminate these risks, providing a safe and reliable solution. Traditional actuators rely on metal-on-metal interactions, which cause structural fatigue over time. Air bellows contain no internal friction points, preventing premature wear. Their high burst pressure rating of over 30 bar ensures safety during high-load operations. Air bellows offer fail-safe functionality, as they gradually deflate instead of catastrophic failure. Unlike hydraulic units, which require emergency shut-off measures, air bellows operate without complex control systems. With minimal energy consumption, they prevent overheating risks associated with traditional suspensions. Food-grade variants with FDA-approved rubber compounds provide contamination-free operation in sensitive environments. Their ability to function in high-dust and corrosive atmospheres further reinforces their reliability. No high-pressure fluids reduce the risk of workplace hazards, making them an ideal choice for critical applications.
7. Cost-Effective Alternative
From a financial standpoint, air bellows provide a more affordable and long-lasting solution compared to hydraulic and mechanical springs. Lower installation costs make them attractive to industries seeking budget-conscious solutions. No requirement for additional pumps, reservoirs, or lubricants means fewer ancillary costs. A simple compressed air source suffices for their operation, reducing energy consumption. Energy savings of up to 30% compared to hydraulic counterparts result in long-term cost efficiency. Their long service life and minimal maintenance demands further improve return on investment. Bulk orders allow for economies of scale, reducing per-unit expenses. Industries with high equipment utilization rates, such as automotive production and heavy machinery, benefit from the durability of air bellows. Their quick installation and easy replacement process reduce downtime, leading to higher productivity and operational efficiency. Cost-effectiveness combined with superior performance makes air bellows an unbeatable alternative.