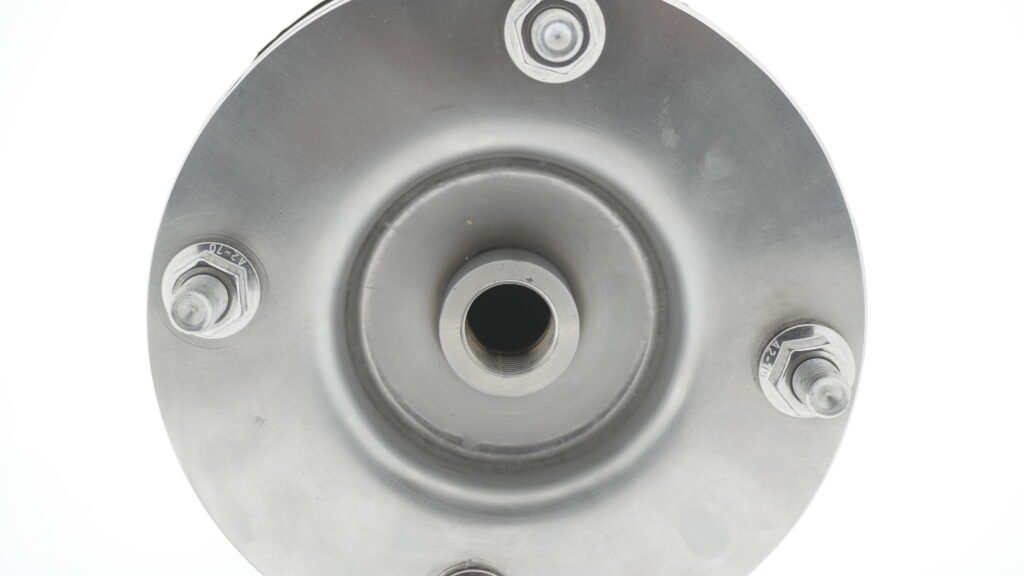
Understanding the Core Functionality of Air Springs
Air springs, also known as pneumatic suspension systems, play a vital role in load leveling and vibration isolation. Their design allows for dynamic stiffness adjustment, making them indispensable in industrial machinery, automotive suspension, and railway applications.
At their core, air bellows function based on compressed air dynamics. When pressurized, the internal air chamber expands, generating a cushioned force capable of supporting heavy loads while maintaining optimal ride height. Unlike mechanical springs, which exhibit a linear stiffness curve, air springs provide a progressive spring rate, offering superior shock absorption. This property allows for smoother operation in dynamic environments where load variations occur frequently. Their ability to provide real-time stiffness control makes them ideal for applications requiring variable damping characteristics. Some industrial models operate within 6-12 bar pressure ranges, accommodating high-performance vibration control systems.
Key Components of Air Springs
To fully appreciate their performance, it’s crucial to understand their construction. Each air spring consists of:
- Elastomeric Bellows – Made of reinforced rubber, these bellows enclose the compressed air, ensuring flexibility and durability. The number of fabric reinforcement plies (typically 2-ply or 4-ply) determines load capacity and pressure endurance. Some models use EPDM rubber, which is resistant to ozone and UV degradation, extending lifespan.
- End Plates – Typically crafted from electro-galvanized steel or stainless steel, these components provide structural integrity and corrosion resistance. Stainless steel variants (AISI-304 or AISI-316L) offer enhanced resistance against harsh chemicals and extreme environments. The thickness of end plates varies between 5 mm and 15 mm, influencing structural strength.
- Air Inlet Ports – Designed for precise pressure regulation, allowing seamless integration with air management systems. Ports come in standard BSP or NPT threading options to ensure compatibility with various pneumatic circuits. Some models feature dual air inlets, allowing faster inflation and deflation cycles. Industrial models may feature G3/4” or G1” air inlets to facilitate high-flow air management.
The Science of Load Distribution
One of the defining characteristics of air suspension is its ability to distribute weight efficiently. This is particularly beneficial in heavy-duty vehicles and industrial presses, where uneven load distribution can lead to premature wear and mechanical failure.
The behavior of an air bellow under load is governed by Boyle’s Law, which states that pressure and volume are inversely proportional. When a force compresses the air spring, the internal volume decreases, increasing air pressure and producing a restorative force that resists compression. This effect results in a self-adjusting suspension system that reacts dynamically to changing load conditions.
For instance, a single-convolution air spring with a diameter of 165 mm and a stroke of 50 mm can handle forces up to 10.1 kN at 7 bar pressure. A triple-convolution design, with an expanded stroke of 300 mm, can sustain loads exceeding 44 kN, making it ideal for industrial shock absorption and heavy vehicle support. Larger models, with higher-diameter bellows, can support loads exceeding 450 kN, providing heavy-load stability in industrial applications. Some railway-specific models maintain a constant ride height with pressure-controlled leveling systems.
Advantages of Air Springs in Suspension Systems
1. Enhanced Ride Comfort
Unlike coil springs, which transfer road shocks directly to the chassis, air springs provide a progressive damping effect, significantly reducing impact forces. This feature is essential for applications such as bus suspensions and railway bogies. The damping characteristics can be adjusted by modulating the internal air pressure, ensuring customized comfort levels in passenger transport systems. Air springs used in buses typically operate between 4-6 bar, ensuring passenger stability.
2. Adjustable Spring Rate
By modifying the air pressure, users can fine-tune the spring stiffness to accommodate varying load capacities. This adaptability is invaluable in off-road vehicles, trucks, and automated manufacturing. A typical double-convolution air spring with a working height of 225 mm can be adjusted from 4 Hz to 1.5 Hz natural frequency, effectively absorbing vibrations at different load levels. Load variations are managed effectively, ensuring consistent performance under dynamic loads. Some industrial actuators integrate electronic pressure regulators, allowing automated stiffness adjustments.
3. Superior Vibration Isolation
Industrial machines often suffer from harmful vibrations that can affect precision and longevity. Air springs effectively isolate vibrations, ensuring optimal performance for CNC machines, presses, and printing equipment. Some models offer 99% vibration isolation, making them indispensable for precision manufacturing. The use of multi-ply bellows enhances the ability to absorb low-frequency oscillations, providing superior shock absorption. Specialized industrial dampers are designed with anti-extrusion plates, preventing rubber deformation under extreme conditions.
Innovations in Air Spring Technology
The latest advancements in air spring materials and design optimization have led to:
- Multi-layer reinforcement for improved fatigue resistance.
- Integrated electronic pressure sensors for real-time monitoring.
- Hybrid air suspension systems combining electromechanical actuators for superior stability control.
- Ultra-lightweight composite materials to reduce overall system weight without compromising strength. Some newer models use Kevlar-reinforced bellows, increasing durability under extreme cyclic loading.
Air springs represent a pinnacle of suspension engineering, offering unparalleled load adaptability, shock absorption, and durability. By leveraging compressed air physics, these components enhance vehicle performance, industrial productivity, and passenger comfort. With ongoing advancements, air springs will continue to reshape the landscape of suspension technology for years to come. Some high-performance designs integrate active dampers, adjusting spring stiffness in milliseconds, optimizing ride quality across varied terrains.