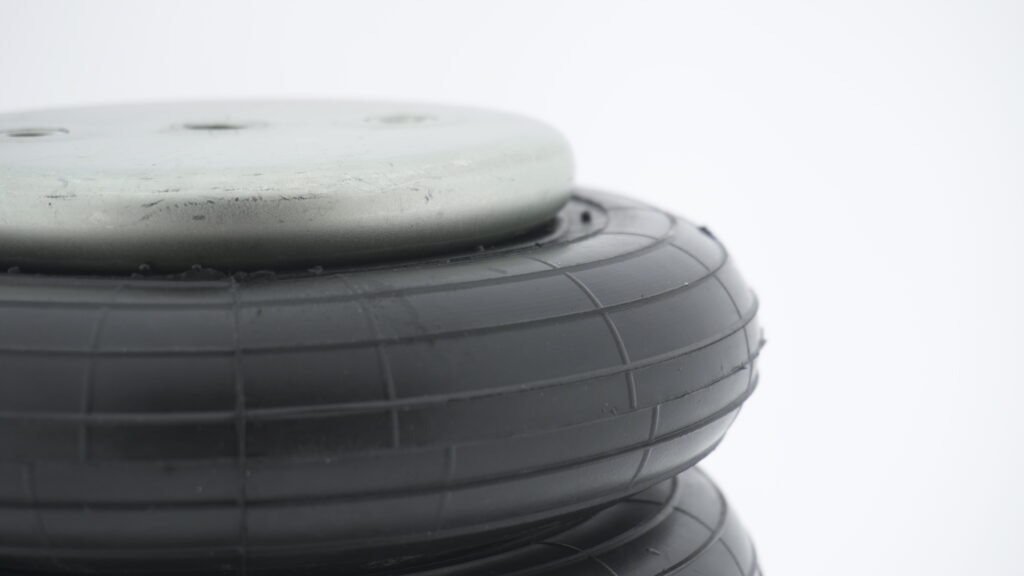
Common Issues in High-Load Applications
Air bellows are widely used in industrial machinery, heavy-duty vehicles, and vibration isolation systems. Under high-load conditions, they may exhibit performance issues that lead to premature failure. Operational inefficiencies and increased maintenance costs can occur. Understanding these issues ensures optimal performance and extended service life.
High loads can cause air bellows to degrade faster than usual. Rubber components may stretch beyond their intended limits. Metal parts can also experience stress fractures over time. If not maintained correctly, these problems reduce reliability.
Routine inspections are essential for detecting early signs of damage. Preventative maintenance can minimize sudden failures in high-load applications. Ensuring correct installation techniques will extend the lifespan of air bellows significantly. Using high-quality materials also improves durability.
Selecting the right air bellow for the specific load requirements is crucial. Different applications require customized designs to achieve maximum performance. Understanding the technical specifications ensures an optimal balance between flexibility and load-bearing capacity.
Pressure-Related Failures
Incorrect air pressure levels cause severe problems in high-load conditions. Excessive pressure results in overstressed material and premature failure. Insufficient pressure reduces stability, causing unpredictable motion and misalignment.
High pressure accelerates rubber fatigue, making air bellows more vulnerable to ruptures. Overinflation also increases the risk of leaks and component failure. Maintaining proper inflation levels ensures efficiency and longevity.
Low pressure causes instability and deformation, reducing load-bearing capacity. Underinflated air bellows may collapse under pressure, leading to unsafe conditions. To prevent this, regular inspections are required.
Proper calibration of pressure control systems helps maintain balance. Using automated monitoring systems can provide early warning signs of pressure anomalies. Regular pressure checks should be part of standard maintenance routines.
Installation of safety valves can prevent sudden overinflation. Pressure relief mechanisms help stabilize air bellows under fluctuating load conditions. Choosing high-strength materials can also improve resistance to pressure-related failures.
Material Fatigue and Wear
Continuous operation under high loads leads to material degradation. Rubber, reinforcement layers, and metal parts deteriorate over time. Wear accelerates if maintenance schedules are ignored.
Air bellows undergo frequent expansions and contractions. This repetitive movement causes micro-tears in rubber compounds. Over time, small cracks expand, leading to significant failures. Identifying fatigue early reduces risks of sudden breakdowns.
Metal components also experience stress under heavy loads. Corrosion and wear reduce their load-bearing ability. Ensuring proper surface treatments protects against environmental factors. Using anti-corrosive coatings extends component lifespan.
High-strength elastomers provide better fatigue resistance. Reinforced materials maintain integrity under extreme conditions. Choosing rubber compounds suited for specific environments enhances durability.
Routine inspections detect early wear signs. Regular lubrication prevents excessive friction between components. Maintaining a clean operational environment minimizes exposure to contaminants. Preventative maintenance ensures air bellows continue functioning effectively under stress.
Mounting and Alignment Issues
Incorrect mounting and misalignment lead to uneven load distribution. This issue accelerates wear and tear, reducing efficiency and performance.
When air bellows are not aligned properly, stress concentrations occur. Uneven forces create weak points, causing premature failure. Regular inspections ensure mounting positions remain optimal.
Misalignment also reduces stroke efficiency. The bellows may not expand or contract as expected. Proper calibration helps maintain uniform motion. Using high-precision mounting systems improves performance.
Bolts and brackets must be tightened correctly. Loose fittings cause vibrations that worsen wear. Using high-torque specifications ensures structural stability.
Adjustable mounting brackets provide flexibility in high-load applications. These allow for corrections without major modifications. Choosing brackets with vibration-dampening features adds stability.
Aligning components before installation prevents future complications. Using laser alignment tools ensures precise positioning. Correcting errors early avoids costly failures later. Proper training of installation personnel enhances reliability.
Environmental Factors
Air bellows exposed to extreme temperatures, chemicals, or UV radiation degrade faster. Harsh environments accelerate wear, leading to failures.
High temperatures cause rubber to lose elasticity. Excessive heat exposure leads to hardening and cracking. Cooling mechanisms reduce thermal stress, preserving rubber integrity.
Cold temperatures also affect flexibility. Frozen rubber becomes brittle, increasing the risk of fractures. Insulating materials provide protection against extreme cold.
Chemicals weaken rubber structures over time. Oils, fuels, and industrial solvents deteriorate elastomers. Choosing chemically resistant materials enhances durability.
UV exposure causes rubber oxidation. Prolonged sunlight contact results in surface degradation. Protective coatings shield against UV damage.
Regular inspections identify environmental stress factors early. Proper storage conditions reduce unnecessary exposure. Ensuring correct material selection extends air bellow lifespan in harsh conditions. Investing in climate-adaptive solutions prevents environmental wear-related failures.
Leakage and Seal Failures
Leaks reduce performance in high-load applications. Air escapes through damaged seals, causing inefficiencies.
Seal degradation occurs from continuous pressure fluctuations. Worn seals allow air to escape, reducing efficiency. Replacing seals at regular intervals prevents failures.
O-ring failures cause slow leaks. Using high-quality seals with proper lubrication improves longevity. Ensuring correct torque specifications during assembly prevents misalignment issues.
Clamping mechanisms should be checked for tightness. Loose fittings cause minor leaks that worsen over time. Conducting periodic seal integrity tests helps detect early issues.
Regularly cleaning sealing surfaces prevents dust accumulation. Contaminants accelerate wear, reducing effectiveness. Using protective sealant compounds minimizes degradation.
Implementing routine pressure tests helps diagnose leaks. Pressure monitoring systems alert operators about drops in efficiency. Maintaining an optimal seal condition ensures peak performance in high-load environments.
Troubleshooting air bellows under high-load conditions requires proactive maintenance. Preventative strategies ensure optimal performance and reduce failures.
Maintaining correct pressure levels, using high-quality materials, and ensuring proper installation maximize efficiency. Conducting regular inspections prevents minor issues from escalating.
Understanding environmental effects helps protect against premature wear. Using advanced sealing techniques minimizes leaks. Implementing pressure monitoring systems prevents fluctuations.
Choosing the right air bellow for the application is critical. Selecting materials based on specific operating conditions ensures durability.
Optimizing alignment, mounting, and pressure control extends service life. Routine maintenance schedules should be strictly followed. Investing in proactive solutions guarantees reliable air bellow performance.