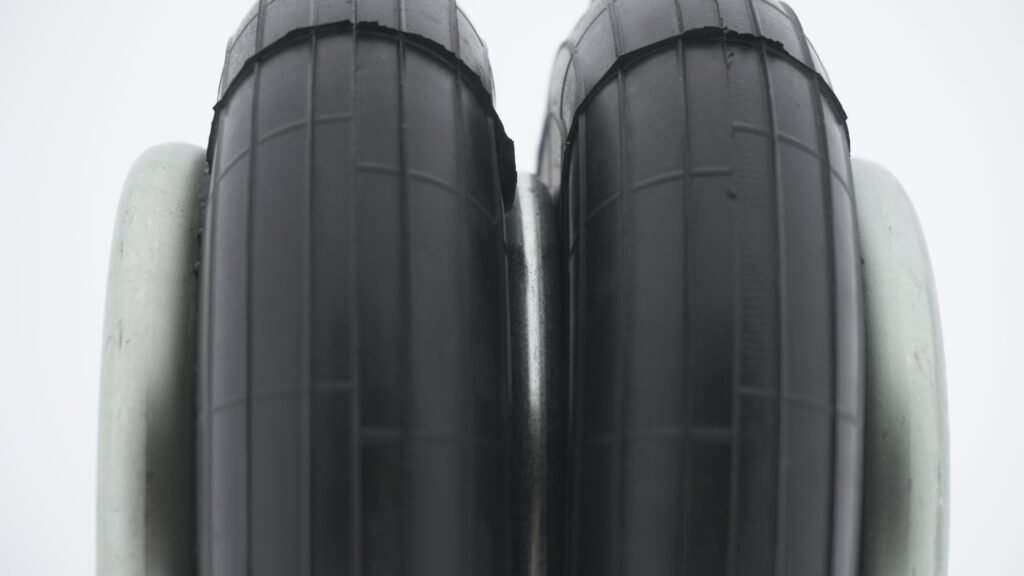
Maximizing Safety in Hazardous Environments
When operating in explosion-proof systems, ensuring the highest level of safety and reliability is critical. Air bellows provide a robust, maintenance-free solution that withstands extreme environments while delivering superior vibration isolation and precise motion control. Their ability to operate without lubricants or sliding seals makes them ideal for industries handling flammable gases, chemicals, and dust-sensitive areas. These systems require reliable components that do not generate sparks or excessive heat. Air bellows meet this requirement due to their non-electric actuation, which prevents ignition risks. Their high-quality elastomer materials ensure excellent chemical and temperature resistance, making them suitable for petrochemical, pharmaceutical, and heavy industry applications. With a long service life and minimal maintenance needs, they contribute to cost savings and operational efficiency. Their adaptability allows them to function in varied industrial setups, providing a dependable safety solution in explosion-prone environments.
Why Air Bellows Are Ideal for Explosion-Proof Systems
Air bellows stand out due to their non-electrical actuation, which eliminates the risk of sparks in volatile conditions. Additionally, their corrosion-resistant materials, such as stainless steel end plates and chemically resistant elastomers, ensure long-term durability under harsh industrial settings. These attributes make them indispensable in oil refineries, gas processing plants, and explosive dust environments. The ability to function efficiently in high-pressure scenarios without lubrication further enhances their reliability. Unlike hydraulic or pneumatic cylinders, air bellows have no moving metal components, reducing wear and extending operational life. Explosion-proof environments require specialized materials, and air bellows can be manufactured from natural rubber, nitrile rubber, and EPDM, among others. Their versatility in mounting configurations also allows them to fit into various industrial designs without requiring costly modifications. Their proven durability and adaptability make them the preferred solution for safety-critical environments.
Additional Benefits in Hazardous Conditions
Air bellows provide shock absorption, reducing stress on equipment operating under intense dynamic forces. They also enable precise load balancing, maintaining stable weight distribution across industrial machinery. Their low failure rate ensures uninterrupted operations in high-risk environments. Another significant advantage is their ability to function in high-humidity conditions, preventing degradation from moisture exposure. Unlike metallic actuators, air bellows do not corrode or deteriorate under extreme environmental factors. Their modular design allows for easy integration into custom applications, making them adaptable for diverse explosion-proof systems. This enhanced versatility ensures optimal machine performance and worker safety.
Key Features Enhancing Explosion-Proof Safety
- Non-Sparking Operation: No internal electrical components reduce ignition risk.
- High Load Capacity: Withstands extreme pressures while maintaining flexibility.
- Vibration Isolation: Absorbs up to 99% of unwanted vibrations, preventing machinery wear.
- Corrosion Resistance: Available in AISI-304 and AISI-316L stainless steel for harsh chemicals.
- Flexible Mounting Options: Adaptable designs ensure secure installation in confined spaces.
Material Selection for Enhanced Protection
Choosing the right material is vital for explosion-proof applications. Our air bellows are manufactured using high-performance elastomers such as:
- Natural Rubber (NR/SBR) – High flexibility and durability in standard conditions.
- Chlorobutyl (CIIR) – Exceptional resistance to acids and industrial solvents.
- Nitrile Rubber (NBR) – Best suited for oil, fuel, and ozone-rich environments.
- Ethylene Propylene Diene (EPDM) – Superior temperature and UV resistance.
- Chloroprene (CR) – Offers balanced weathering and oil resistance.
Customizable Solutions for Varied Industrial Needs
Explosion-proof applications demand precision-engineered air bellows with customizable diameters, mounting configurations, and pressure ratings. We offer solutions designed for:
- Petrochemical processing
- Mining and tunnel ventilation systems
- Chemical and pharmaceutical industries
- Dust-sensitive manufacturing plants
- Aerospace and military-grade equipment
Mounting Configurations
- Bead Ring Design: Provides quick installation and secure fixation.
- Dismountable Design: Allows for easy replacement and maintenance.
- Crimped Design: Ensures leak-free performance in high-pressure applications.
Performance Under Extreme Conditions
Explosion-proof systems require components that withstand high pressures, extreme temperatures, and continuous operational loads. Our air bellows excel under such conditions, offering:
- Working pressure range of up to 12 bar (higher pressures available on request).
- Operational temperature limits from -40°C to +115°C, depending on material selection.
- Designed for lateral misalignment absorption up to 30 mm, reducing mechanical stress.
- Compact installation height, ensuring usability in space-constrained environments.
Safety Enhancements Through Redundant Systems
In explosion-proof applications, redundant safety systems ensure fail-safe operation. Incorporating backup air springs prevents unexpected equipment failures, increasing system resilience. Smart monitoring systems can be integrated to detect pressure deviations, alerting operators to potential malfunctions before they escalate. Additionally, protective enclosures shield air bellows from abrasive dust or chemical exposure, further extending their lifespan. Investing in multi-layered safety solutions enhances operational security, minimizing workplace hazards.
Vibration Isolation: A Critical Factor
One of the greatest benefits of air bellows is their ability to provide outstanding vibration isolation. In explosion-prone environments, excessive vibration can lead to:
- Mechanical fatigue and failure
- Unintended ignition sources
- Reduced equipment lifespan
- Operational inefficiencies
By absorbing vibrations before they transfer to surrounding structures, air bellows improve overall system reliability and safety.
Cost Efficiency and Maintenance Benefits
Unlike traditional pneumatic or hydraulic actuators, air bellows are maintenance-free, leading to significant cost savings over their lifetime. Their simple yet robust construction eliminates the need for lubrication, reduces downtime, and ensures consistent performance. Key cost-saving benefits include:
- Lower installation costs due to compact and modular design.
- Extended operational lifespan, reducing replacement frequency.
- Minimal wear and tear, lowering the need for periodic inspections.
- Energy-efficient performance, reducing compressed air consumption.
Ensuring Compliance with Safety Standards
All air bellows used in explosion-proof environments must comply with strict industry safety standards such as:
- ATEX Directive 2014/34/EU for explosive atmospheres.
- ISO 2230 for rubber product storage requirements.
- EN 14214 ensuring resistance to biofuels and chemicals.
- CE Certification for pressure equipment compliance.
By adhering to these standards, our solutions guarantee safe and efficient operation in high-risk environments.
Ensuring safety in explosion-proof systems demands high-performance, non-sparking, and durable solutions. Our air bellows provide an unmatched combination of safety, durability, and efficiency, making them the ideal choice for critical industrial applications. Their ability to absorb vibrations, handle extreme loads, and resist corrosion ensures maximum operational reliability. Contact us today to explore how air bellows can enhance your explosion-proof system’s safety and performance.