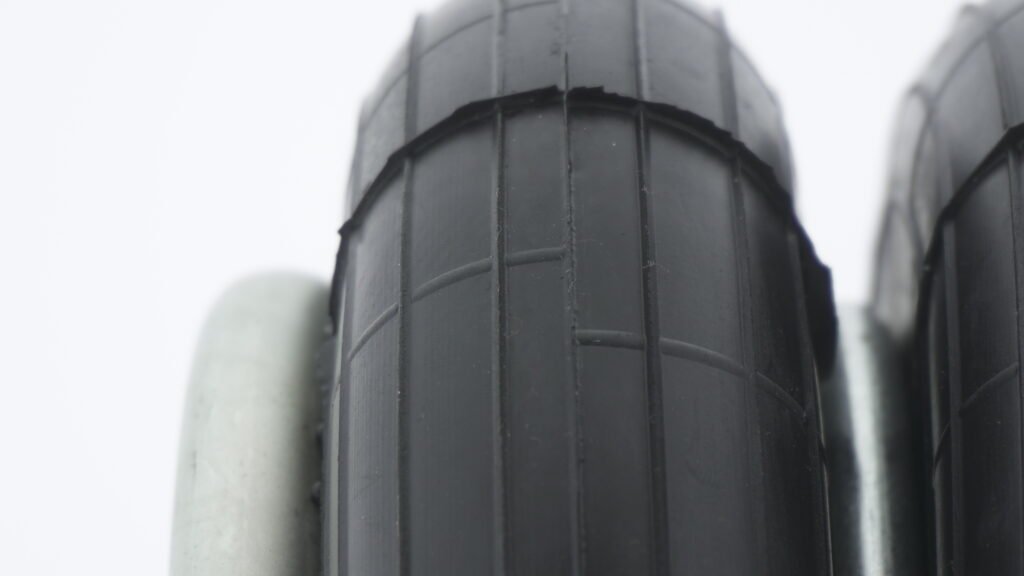
Understanding the Challenges in Chemical Environments
Air bellows are widely used in chemical processing plants due to their ability to provide vibration isolation, actuation, and load compensation. However, their exposure to corrosive substances, high temperatures, and abrasive chemicals presents significant challenges. Ensuring environmental safety in these conditions requires proper material selection, maintenance, and protective measures. The combination of rubber and metal components in air bellows makes them vulnerable to chemical degradation, which can lead to structural failure if not managed properly. Operators must be aware of the operating temperature range, chemical exposure limits, and mechanical stress factors to optimize the lifespan of air bellows in these demanding settings. Selecting the correct material composition ensures long-term durability and safe performance under extreme conditions.
Additionally, thermal expansion can affect the performance of air bellows, leading to material fatigue if not properly accounted for. Selecting materials with high thermal stability can prevent unwanted deformation and improve reliability. Moreover, bellows installed in hazardous environments must feature explosion-proof designs to comply with safety standards, ensuring that they do not become ignition sources in volatile atmospheres.
Material Considerations for Air Bellows
The primary materials used in air bellows include natural rubber (NR/SBR), nitrile rubber (NBR), chlorobutyl (CIIR), ethylene propylene diene (EPDM), and chloroprene (CR). Each material has unique properties that determine its resistance to chemicals, ozone, and temperature fluctuations. Selecting the correct material for a chemical setting is essential to prevent premature degradation.
- Natural rubber (NR/SBR): Excellent mechanical properties but limited chemical resistance (temperature range: -40 °C to +70 °C). Used in standard applications where exposure to harsh chemicals is minimal.
- Nitrile rubber (NBR): Resistant to oils, fuels, and ozone, making it ideal for petrochemical applications (temperature range: -25 °C to +110 °C). Often selected for oil refineries and fuel transfer systems.
- Chlorobutyl (CIIR): Offers superior acid resistance, essential for chemical plants (temperature range: -30 °C to +115 °C). Used in aggressive acid-processing units.
- EPDM: High ozone and temperature resistance, suitable for extreme environments (temperature range: -20 °C to +115 °C). Commonly applied in high-heat industrial zones.
- Chloroprene (CR): Moderate oil resistance with excellent weather durability (temperature range: -20 °C to +110 °C). Frequently implemented in outdoor chemical processing environments.
Advanced Protective Measures for Air Bellows
In addition to choosing the right materials, incorporating advanced protective measures further enhances environmental safety in chemical settings.
- UV-resistant coatings: Air bellows exposed to direct sunlight or ultraviolet light in outdoor installations benefit from UV-resistant coatings, which prevent premature degradation.
- Multi-layer construction: Some air bellows feature reinforced multi-layer rubber compounds to improve resilience against corrosive environments.
- Self-sealing technology: Specially designed self-sealing bellows automatically close small punctures, extending their service life in high-risk environments.
- Temperature-resistant reinforcements: Using aramid fiber reinforcement enhances durability in high-temperature applications where other materials would degrade.
- Electrically conductive options: Some applications require static discharge protection to avoid the buildup of static electricity, which can be hazardous in flammable environments.
Enhanced Safety Measures in Chemical Environments
To ensure safe operation, air bellows must meet stringent industrial safety standards. The following precautions should be taken to prevent mechanical failure and chemical degradation.
- Regular inspections: Frequent visual and mechanical checks to detect wear, leaks, or degradation before critical failure occurs.
- Pressure monitoring: Ensuring the air bellows operate within specified pressure limits to prevent ruptures.
- Leak detection systems: Real-time monitoring for compressed air loss or chemical infiltration.
- Proper installation: Avoiding misalignment and ensuring secure mounting to prevent failures caused by mechanical stress.
- Load capacity: Depending on the model, air bellows can support loads ranging from 0.5 kN to 450 kN, making them ideal for heavy-duty applications.
- Custom fittings: Certain applications require customized inlet and outlet fittings to accommodate specialized chemical processes.
Optimized Applications of Air Bellows in the Chemical Industry
Air bellows play a crucial role in various chemical processing applications, such as motion control, shock absorption, and load stabilization. Their flexible design makes them highly versatile.
- Pneumatic actuators: Providing precise motion control for chemical handling machinery.
- Vibration isolation: Protecting sensitive equipment from mechanical shocks in high-frequency environments.
- Height regulation: Maintaining stable working heights in reactors and mixing tanks, preventing process inconsistencies.
- Load compensation: Ensuring even distribution of chemical loads in conveyor systems.
- Angular movement: Some air bellows offer up to 25° of tilt motion, allowing for flexibility in dynamic applications, reducing stress on connected components.
- Emergency safety systems: Some air bellows are used in emergency shutdown mechanisms, where rapid inflation or deflation is required to prevent hazardous conditions.
Regulatory Compliance and Environmental Considerations
To ensure environmental safety, air bellows must comply with industry regulations such as:
- ISO 9001: Ensuring quality management in manufacturing, guaranteeing consistent performance.
- REACH Compliance: Avoiding the use of hazardous substances in rubber compounds, reducing environmental impact.
- ATEX Certification: Required for use in explosive atmospheres, ensuring worker safety in hazardous environments.
- RoHS Compliance: Ensures that restricted hazardous materials are not used in production, reducing environmental pollution.
Manufacturers must also adopt sustainable practices such as recyclable materials, low-emission production, and energy-efficient designs to reduce the environmental footprint and long-term waste.
Ensuring environmental safety for air bellows in chemical settings involves selecting the right materials, implementing protective measures, and following strict maintenance procedures. By leveraging stainless steel components, chemical-resistant elastomers, and advanced monitoring technologies, companies can enhance safety, longevity, and efficiency in chemical processing applications. Proper selection and preventive maintenance significantly reduce operational risks, making air bellows an optimal choice for chemical industry applications.