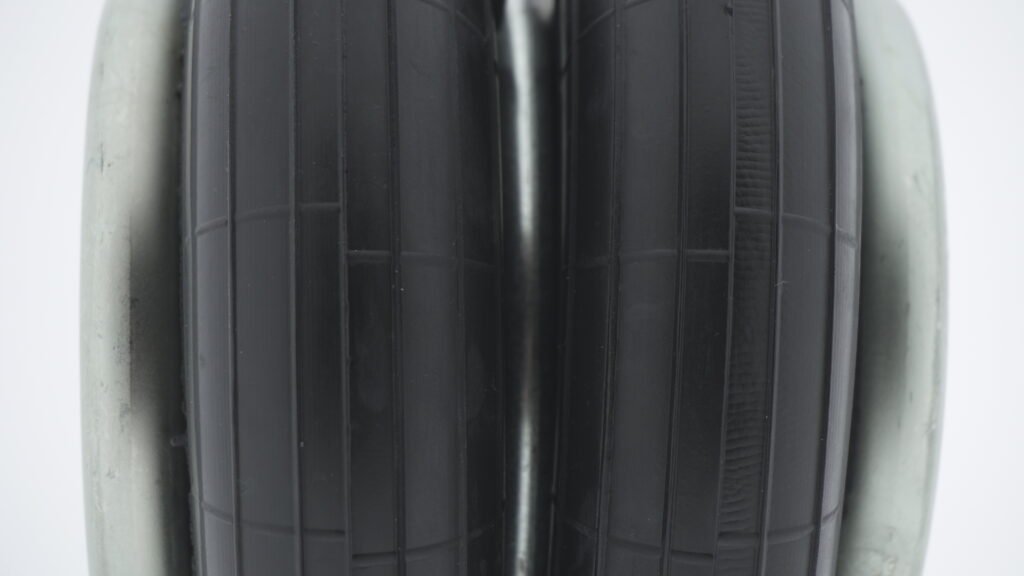
Maximizing Efficiency in Pneumatic Systems
In industrial applications, energy efficiency is a key factor in optimizing pneumatic systems. The use of air bellows plays a significant role in reducing energy consumption while maintaining operational effectiveness. By focusing on pressure regulation, friction reduction, and dynamic performance, we can enhance system efficiency and extend the service life of equipment. Energy efficiency is essential for industries aiming to reduce operational costs. Optimized pneumatic bellows provide better performance with reduced power input. Minimizing air leaks and improving pressure distribution ensures better results. Reducing friction between components prevents unnecessary power loss. By implementing advanced sealing techniques, compressed air utilization improves significantly. Consistently monitoring pressure variations helps in maintaining air spring performance. Preventing energy dissipation through optimized air control mechanisms is crucial. Air bellows solutions provide a more sustainable approach to energy conservation. Smart integration of pneumatic components enhances overall system efficiency. Achieving maximum output with minimal energy expenditure remains the ultimate goal.
How Air Bellows Contribute to Energy Savings
Minimal Air Leakage
Unlike conventional pneumatic cylinders, air bellows operate with fewer moving parts, minimizing air leaks and preventing energy losses. The rubber construction ensures a tight seal, improving compressed air efficiency and lowering operational costs. The absence of complex seals reduces friction. Lowering friction leads to longer operational life and better energy retention. Fewer mechanical failures mean fewer maintenance requirements. Industries rely on air bellows for long-term reliability. The unique material composition offers superior resistance to environmental factors. External temperature variations have a minimal effect on air spring efficiency. Consistent airflow regulation prevents excessive energy consumption. Eliminating pressure fluctuations improves stability in industrial processes. Achieving optimal energy distribution is a priority in pneumatic systems. Proper seal designs reduce air wastage significantly. Enhancing energy conservation in automation processes ensures sustainable industrial growth. Air bellows support efficient power transmission for demanding applications.
Lower Friction and Wear
With no internal sliding components, air bellows experience significantly lower friction losses. Traditional hydraulic actuators require lubrication and suffer from wear over time, leading to efficiency degradation. The unique flexible membrane of air bellows provides smooth motion with minimal resistance, enhancing overall system energy performance. Reduced component friction ensures greater reliability in pneumatic circuits. Air bellows require fewer lubrication cycles. The elimination of hydraulic fluid results in cleaner operations. Energy transfer is optimized for precise mechanical movement. Increased wear resistance prolongs the operational lifespan. Decreased energy loss due to mechanical inefficiency improves performance. The dynamic flexibility of air bellows enhances adaptability in industrial environments. Preventing excessive wear ensures a steady force output. Lubrication-free systems lower maintenance costs. Enhancing material strength further reduces structural fatigue. Consistently optimizing friction coefficients increases energy efficiency. Smoother motion profiles reduce strain on connected components. Air bellows design enhances mechanical longevity.
Optimized Pressure Utilization
Air spring actuators achieve high force output with low air consumption. By adjusting internal air pressure, they can maintain consistent force distribution, ensuring efficient power transmission in industrial machinery and vibration isolation applications. Maintaining stable pressure levels minimizes fluctuations in actuator response. Air springs dynamically respond to changing operating conditions. Enhanced pressure regulation improves pneumatic precision. Adaptive force control supports various automation processes. Reducing compressed air waste improves cost-effectiveness. Sustaining airflow efficiency ensures long-term reliability. Preventing over-inflation optimizes energy use. Pressure monitoring systems detect inefficiencies early. Implementing feedback control loops maximizes performance. Flexible membranes conform to dynamic loads efficiently. Improving air retention reduces energy loss. Enhancing spring elasticity supports varied applications. Pneumatic designs achieve superior motion control. Proper flow distribution reduces pressure variations.
Thermal Stability and Efficiency
Air bellows exhibit excellent thermal stability, ensuring consistent performance in varying temperature conditions. Unlike hydraulic systems, which suffer from fluid viscosity changes, air bellows maintain consistent operation in extreme environments. The flexible rubber construction prevents thermal expansion issues, maintaining structural integrity. Heat-resistant elastomers enhance durability, reducing temperature-related failures. Industries operating in high-temperature environments benefit from air bellows due to their resistance to heat degradation. Maintaining thermal balance within pneumatic circuits improves air utilization efficiency.
Integration with Smart Control Systems
Modern pneumatic systems incorporate smart control units that optimize air pressure regulation. Automated feedback loops continuously adjust air spring pressure, ensuring precise energy allocation. Smart sensors detect real-time pressure variations, preventing energy overuse. Integrating data-driven adjustments optimizes system responsiveness. Energy-efficient protocols in automated air bellows reduce compressed air waste, aligning with sustainable manufacturing goals. Enhanced digital monitoring helps detect system inefficiencies early, allowing for preventive maintenance strategies. Smart integration enhances performance consistency, reducing power fluctuations.
Maximizing the energy efficiency of pneumatic systems requires strategic design, material optimization, and proper maintenance. Air bellows offer superior performance with minimal energy consumption, making them the ideal choice for industrial applications. By investing in high-quality air springs, industries can achieve cost savings, environmental benefits, and enhanced system longevity. Implementing energy-efficient solutions optimizes compressed air use. Proactive system monitoring prevents inefficiencies. Efficient air pressure regulation sustains pneumatic performance. Long-term sustainability depends on optimized pneumatic technology. Improved component integration enhances operational efficiency. Balancing load distribution improves mechanical output. Advanced engineering principles ensure stable force application. Efficient energy allocation drives industry-wide progress. Preventing air leaks reduces power consumption. Enhancing material resistance supports longevity. Achieving peak operational efficiency remains the primary objective. Industrial sectors benefit significantly from optimized air bellows technology.