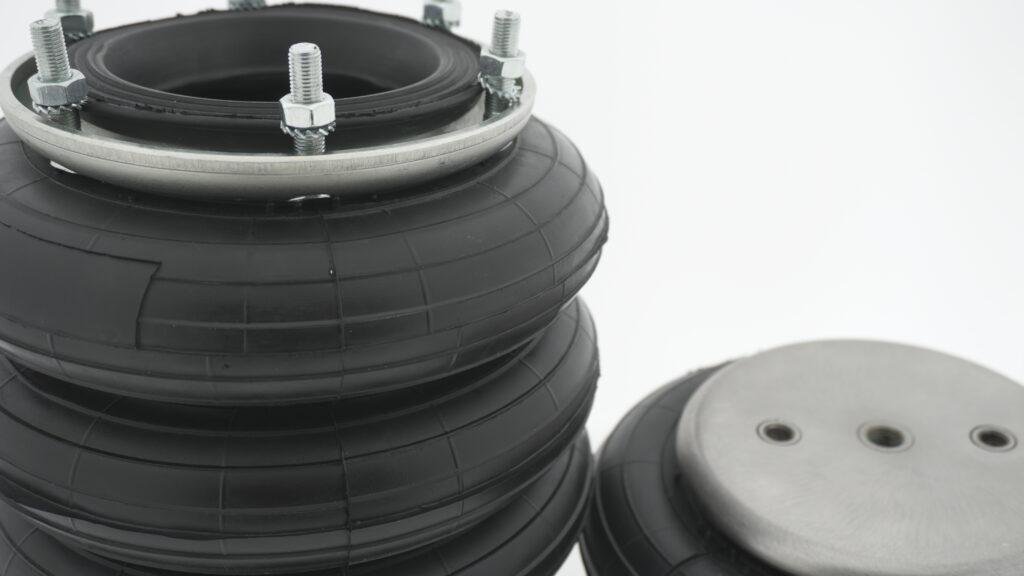
We regularly work with engineers who require reliable components for actuation and isolation in high-demand environments. Air bellows are ideal when compactness, flexibility, and performance matter. Each bellow contains multiple fabric-reinforced plies, embedded between an inner and outer rubber layer. They are vulcanized together with steel bead rings and mounted using galvanized or stainless steel plates. These bellows resist corrosion, oil, pressure, heat, and vibration across many industrial environments. We use air bellows rated up to 12 bar, handling axial forces exceeding 300 kN and natural frequencies as low as 1.2 Hz. Bellows can be single, double or triple convolution, depending on stroke and force needs. Pressure-regulated systems ensure constant height across shifting loads. Their flexible geometry allows for misalignment and tilt up to 30 mm or 25° respectively. This reduces stress and wear in mechanical assemblies. Tevema provides complete solutions with modular design options and elastomer types tailored to specific operating conditions.
Adaptive load isolation in automated lines
A manufacturing line required vibration isolation for precision tools mounted on a suspended concrete platform. Conventional rubber dampers did not perform well. We introduced double convolution bellows operating at 7 bar, each capable of supporting up to 73 kN. Their natural frequency of 1.58 Hz eliminated transfer of floor-borne microvibrations. Each unit had a design height of 285 mm and a stroke of 265 mm, maintaining form under dynamic load changes. Bellows were mounted using galvanized steel end plates with integrated G1/2 air inlets and M10 blind nuts. Height control was automated through a pressure feedback loop, ensuring stability even under shifting loads. Sensitive equipment downstream showed improved measurement consistency and fewer calibration interruptions. Mechanical fasteners were no longer needed to realign structures. Operators reported reduced machine noise and better performance consistency. The system ran continuously without service interruption. This confirmed the effectiveness of air bellows in isolating sensitive components from building-based vibration sources.
High-pressure actuation in press systems
A client operating vertical stamp presses needed a compact yet powerful alternative to hydraulic actuators. Hydraulic cylinders were large and maintenance-intensive. We installed triple convolution air bellows with four fabric plies and rated for 12 bar operation. Each actuator delivered over 300 kN of thrust, with a stroke of 375 mm and natural frequency near 2.0 Hz. Components included galvanized top plates, M10 blind nuts, and G3/4 air inlets. Bellows absorbed dynamic shocks and offered stable upstroke and downstroke profiles. Their ability to tolerate tilt angles up to 25° reduced the need for alignment brackets. Testing over 500,000 full cycles showed no structural degradation or loss of force. Noise levels were lower than hydraulic counterparts. Pressure adjustments allowed fine control of stroke behavior without stick-slip effects. The system’s compactness enabled easier integration. Maintenance requirements dropped significantly. This made air bellows an ideal actuator replacement in press systems needing consistent, compact, and smooth force output.
Long-life performance in corrosive environments
We were contacted by a facility facing rubber isolator degradation due to acidic vapors and high humidity. The environment caused fast corrosion. We recommended double convolution bellows built with chlorobutyl rubber and AISI-316L stainless steel end fittings. These bellows withstood pressures up to 7 bar, with load capacities of 28 kN and natural frequencies below 1.6 Hz. The bead ring design eliminated the need for complex flanges. After one year of continuous exposure, the bellows showed no swelling, cracking, or loss in mechanical performance. Stainless steel resisted corrosion from water, chemicals, and detergents. Equipment mounted with these bellows needed no realignment or inspection over that period. The bellows maintained original stroke length and height, without deformation. Other elastomers had failed previously in less than three months. This confirmed the importance of matching elastomer type with environment. The chlorobutyl-stainless combination became standard in other production areas. Operators praised the stability and reliability improvements.
Supporting heavy-duty vertical presses
A stamping company reported premature cracking of their concrete foundation due to stress from vertical presses. Vibration and uneven loading were the cause. We proposed a solution using double convolution bellows rated for 7 bar with natural frequencies near 1.7 Hz. Each unit supported up to 69 kN with a design height of 250 mm. They were secured using M8 blind nuts and socket head bead rings, ensuring precise mounting. The bellows distributed force evenly across the press structure. Even under asymmetric die loading, the stroke remained level, reducing mechanical fatigue. The system eliminated resonance peaks and reduced floor vibration transfer. Operators reported smoother stroke transitions and fewer press alignment issues. With over 1.2 million cycles, the bellows maintained performance without maintenance. The original concrete was preserved. This case demonstrated how air bellows protect both machine and structure. They offered an ideal solution for heavy vertical loading with minimal mechanical complexity.
Compact setups in confined production floors
A textile plant required vibration control without increasing machine height. Vertical space was limited by overhead systems. We installed single convolution bellows with aluminum end plates, measuring only 50 mm in height. Each unit absorbed up to 18 kN, operated at 7 bar, and provided natural frequencies around 2.7 Hz. Stroke range was 70 mm, sufficient for equipment leveling. Mounting involved G1/4 threaded inlets and M6 blind nuts to fit narrow baseplates. These bellows absorbed both vertical and horizontal vibration from loom motion. Electronic controllers nearby showed reduced error rates. Operators noticed quieter operation and lower mechanical feedback. Over one year, the bellows maintained elasticity without height loss. No adjustments or realignments were needed. The rubber construction resisted textile dust and humidity. Because of the design’s compactness, no additional supports were required. This use case confirmed that air bellows provide space-saving, efficient vibration isolation even in limited-height production environments without reducing effectiveness.
Thermal stability in foundry applications
In a steel casting plant, precision weighing systems were being disrupted by ambient heat and vibrating platforms. Traditional rubber mounts failed quickly. We replaced them with nitrile-based triple convolution bellows, each rated to +110°C and resistant to oil mist. Bellows supported 44 kN at 8 bar, maintained stroke integrity, and operated with a natural frequency of 2.5 Hz. Galvanized hardware resisted furnace-side conditions. They were mounted using M10 blind nuts and connected with G3/4 air inlets for uniform fill rate. Bellows maintained height control even with temperature fluctuation. Calibration drift dropped to nearly zero. Mechanical shocks from vibrating shakers were absorbed without damaging internal load cells. The bellows showed no cracks, hardening, or loss of form. Over 14 months, the system ran continuously without breakdown. The plant extended the solution to other equipment. This case proved the thermal resilience and precision stability of properly engineered air bellows in extreme environments.
Elevating modular assembly tables
In a lean assembly system, ergonomic worktable height adjustment was required for multiple operator profiles. Electric actuators lacked flexibility. We used double convolution air bellows rated for 6 bar, delivering up to 27 kN per unit. Stroke was 120 mm, allowing standing and seated work heights. Each bellow featured three fabric plies, galvanized top plates, and M8 blind nuts. A central air manifold controlled the system, allowing synchronized movement across multiple tables. Adjustment took less than 4 seconds. Bellows stayed locked in place without sliding or drift. Pressure tuning ensured stable position holding even under variable weight. The system needed no lubrication and had no metal-on-metal wear surfaces. Tests over 1 million cycles showed zero degradation. Operators preferred the noise-free motion. Energy costs dropped compared to electric columns. This solution offered enhanced ergonomics and reliable adjustment across shift changes. Air bellows provided flexible, safe, and clean height control ideal for modular production floors.