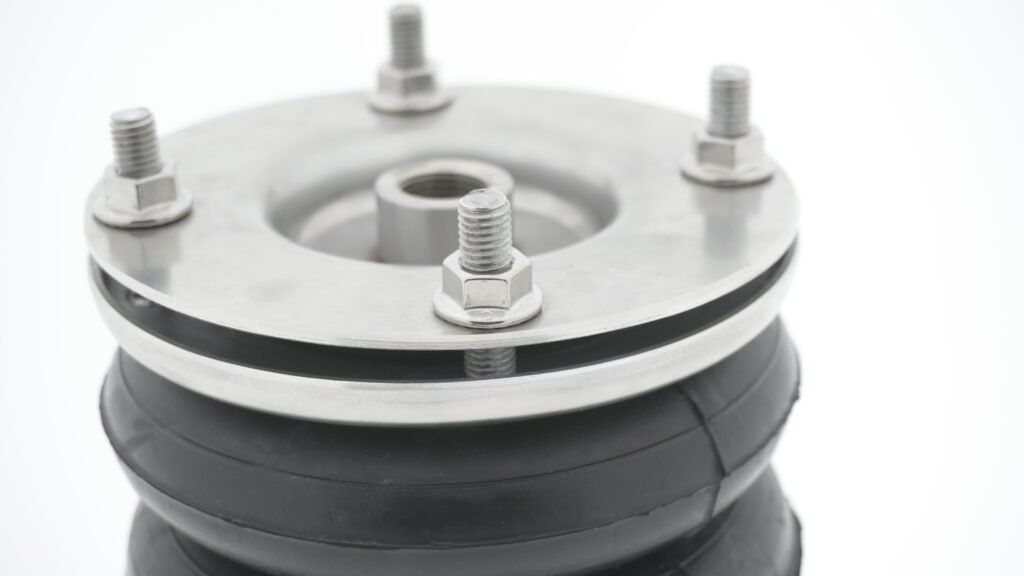
Enhancing Industrial Efficiency with Smart Air Bellows
Industrial air bellows have long been essential components in applications requiring vibration isolation, load support, and pneumatic actuation. The integration of real-time monitoring sensors has revolutionized the way these components perform, providing precise data that enhances efficiency, safety, and predictive maintenance.
Advanced air bellows with embedded pressure and displacement sensors offer precise control over load capacity, height adjustments, and shock absorption. With a maximum operating pressure of 12 bar, these components sustain high loads up to 450 kN. The inclusion of stainless steel end plates ensures durability in extreme environments. Additionally, electro-galvanized steel parts provide enhanced corrosion resistance, making them suitable for outdoor applications. Integrated wireless transmission capabilities enable remote monitoring, ensuring that engineers receive instant alerts about pressure fluctuations, leaks, and performance deviations.
Advantages of Sensor-Integrated Air Bellows
1. Predictive Maintenance for Extended Lifecycle
Traditional air bellows require periodic inspections to assess wear, pressure variations, and potential leaks. With integrated sensors, monitoring becomes continuous, allowing early detection of issues before they escalate. By utilizing pressure, temperature, and displacement sensors, manufacturers can track real-time performance and schedule maintenance precisely when needed, reducing downtime and extending component lifespan.
The four-ply construction available in premium models enhances durability, enabling operations in harsh industrial environments. Some units support custom elastomer compounds such as chlorobutyl (CIIR) for acid resistance, or nitrile (NBR) for oil resistance. These materials provide superior flexibility and ensure operational efficiency under varying temperature conditions from -40°C to +115°C. Predictive maintenance strategies utilizing sensor-driven diagnostics help to prevent catastrophic failures, ensuring safe and reliable operations.
2. Improved Load Distribution and Performance Optimization
The real-time data collected from pressure and force sensors enables dynamic load distribution adjustments. This is particularly beneficial in heavy machinery, automotive suspension systems, and industrial automation, where maintaining uniform pressure ensures optimal functionality. With smart air bellows, performance fluctuations are minimized, ensuring consistent vibration isolation and load stability.
Smart air bellows accommodate misalignment up to 30 mm, reducing mechanical stress in dynamic systems. In high-performance industrial presses, real-time pressure feedback enhances force uniformity, preventing uneven wear and extending machine lifespan. Advanced control algorithms automatically adjust inflation and deflation cycles, maintaining optimal load-bearing capacity. With integrated feedback loops, operators achieve precise motion control, essential for robotic applications and precision engineering.
3. Enhanced Safety Through Continuous Monitoring
By integrating pressure, strain, and temperature sensors, companies can enhance operational safety. For example, in pressurized systems, an unexpected pressure drop could indicate a potential leak or failure. Automated alerts ensure immediate action, preventing hazardous situations and protecting critical assets.
Smart air bellows maintain constant natural frequency values despite variable loads, ensuring stable vibration isolation. High-end models operate with natural frequencies as low as 1.5 Hz, significantly reducing structurally transmitted noise. This feature is crucial in precision manufacturing environments, where excessive vibrations compromise product quality. Overpressure shut-off systems provide additional safety layers, preventing structural damage and ensuring long-term system reliability.
Technological Integration: How Smart Sensors Work
1. Sensor Types in Air Bellows
- Pressure Sensors: Measure internal air pressure to detect leaks and ensure optimal performance.
- Displacement Sensors: Monitor the expansion and contraction of the bellow, crucial for pneumatic actuators.
- Temperature Sensors: Track heat buildup, ensuring the material withstands operational limits.
- Vibration Sensors: Detect irregularities that may indicate structural weaknesses.
- Load Sensors: Measure force distribution, improving efficiency in automated systems.
2. Wireless Communication and Data Analytics
Modern air bellows with integrated sensors can communicate via IoT-based platforms, transmitting real-time data to a central monitoring system. This enables instant analysis and automated adjustments. With machine learning algorithms, anomalies can be detected early, facilitating predictive maintenance strategies.
Wireless-enabled air bellows can be integrated into existing SCADA and ERP systems, ensuring seamless compatibility with industrial control infrastructures. Data transmission occurs via 5G or industrial-grade Wi-Fi, guaranteeing low-latency communication for mission-critical applications. Sensor logs stored in cloud databases enable historical performance analysis, allowing engineers to optimize operating conditions proactively.
The integration of smart sensors in air bellows has revolutionized industrial applications, ensuring higher efficiency, enhanced safety, and significant cost savings. As industries continue to embrace IoT-based predictive maintenance, sensor-integrated air bellows will play a pivotal role in optimizing industrial automation, transportation, and heavy machinery operations.
With self-regulating load distribution, real-time diagnostics, and automatic failure prevention, these components are crucial in future-proofing industrial applications. Industries that prioritize efficiency, durability, and predictive maintenance will find sensor-equipped air bellows indispensable for enhancing operational reliability.