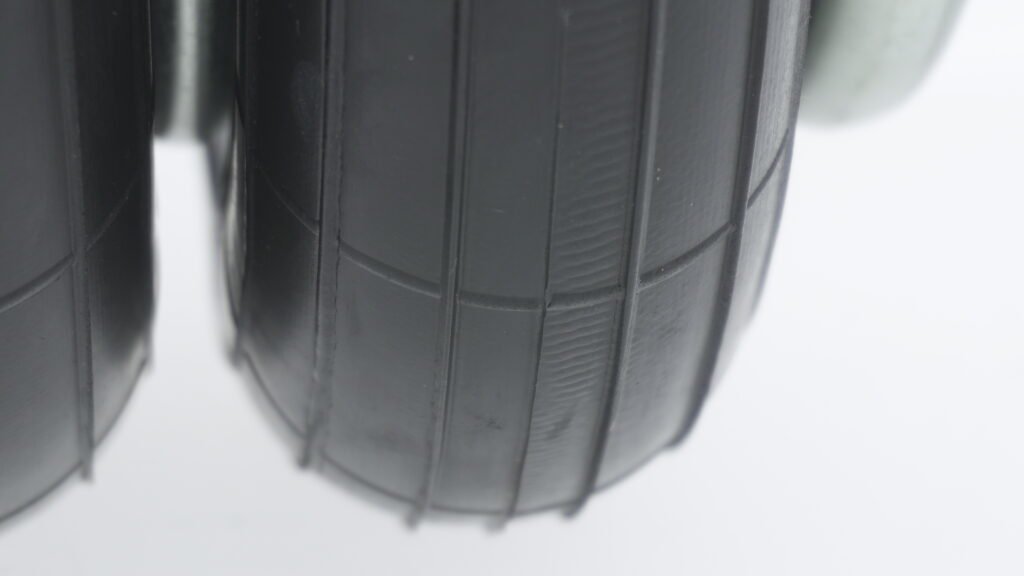
Ensuring the compliance of air bellows is crucial for their reliable performance. Air bellow testing is essential to confirm durability, safety, and efficiency in various applications. A failure in compliance can lead to severe malfunctions, costly downtime, and potential hazards. Compliance testing helps in identifying issues before installation, ensuring long-term functionality. It involves evaluating material integrity, pressure capacity, load-bearing performance, and vibration isolation efficiency.
Testing procedures must be thorough and adhere to industry standards to guarantee consistency in product quality. Each aspect of an air bellow, from its rubber composition to its metal end closures, must be examined. This guide provides a structured method for assessing compliance through various testing procedures. Following these steps ensures optimal performance and extended service life, making air bellows a reliable choice in industrial and vehicular applications.
Key Parameters for Compliance Testing
Before conducting compliance testing, it is essential to define the parameters that determine performance. These parameters provide insight into whether an air bellow meets industry requirements:
- Maximum Load Capacity – Determines how much force the air bellow can support. Most industrial-grade models withstand up to 450 kN.
- Operating Pressure Range – Standard bellows operate between 6 and 12 bar, with heavy-duty models reaching 15 bar.
- Axial Stroke Limits – Defines the extension and compression limits. Some designs allow movement between 30 mm and 250 mm.
- Material Integrity – Must resist temperature changes, oils, and exposure to chemicals.
- Vibration Isolation Efficiency – High-quality bellows achieve over 99% vibration isolation. Some models have frequencies as low as 1.5 Hz.
- Burst Pressure – Should be at least four times the maximum operating pressure.
- Fatigue Life – The air bellow must endure over one million compression-extension cycles without failure.
Testing these parameters ensures reliability, safety, and performance consistency. Compliance verification is a vital step before implementing air bellows in critical applications.
Step-by-Step Compliance Testing Process
1. Visual Inspection
A visual inspection is the first step in compliance testing. This step identifies visible damage, wear, or production defects before further tests. The following aspects must be checked:
- Surface cracks, punctures, or rubber deformities.
- Loose fittings or signs of metal corrosion.
- Abnormalities in the reinforcement plies.
- Condition of bead rings and end closures.
A thorough pre-test examination reduces the risk of unnecessary failures during performance testing. If defects are found, the bellow should not proceed to pressure testing until resolved.
2. Dimensional Verification
To confirm design consistency, the air bellow’s dimensions must be verified using precision instruments. Measurements must match manufacturer specifications:
- External and internal diameters.
- Minimum and maximum stroke lengths.
- Alignment of mounting holes.
- Wall thickness of rubber layers should be between 3 mm and 10 mm.
Accurate dimensional verification ensures that the air bellow will function correctly when installed. Misalignments or thickness variations can cause premature failures.
3. Pressure Leak Test
A pressure leak test assesses airtightness and detects potential weaknesses. The process involves:
- Pressurizing the air bellow to its operating range.
- Monitoring for pressure loss over time.
- Submerging in water to check for air bubbles, indicating leaks.
- Using ultrasonic sensors for precise leak detection.
A properly sealed air bellow should retain pressure without fluctuations. If leaks are found, they must be sealed before further testing.
4. Load and Deflection Testing
Air bellows must be tested under different load conditions to determine their flexibility and strength. A hydraulic press applies varying loads while measuring axial displacement:
- Confirm the predicted stroke length under specific loads.
- Compare results with manufacturer specifications.
- Ensure the spring rate remains consistent across multiple test cycles.
- Measure lateral stability to detect unwanted movement.
This test ensures that the air bellow provides the expected force and flexibility required for its intended use.
5. Vibration Isolation Efficiency
To test vibration control, the air bellow is mounted on a test rig. The procedure involves:
- Measuring vibration frequencies at different pressures.
- Comparing results with baseline damping values.
- Confirming compliance with ISO 10846 vibration standards.
- Evaluating torsional and lateral vibration reduction.
An effective air bellow should minimize vibration transmission, enhancing equipment longevity and stability.
6. Temperature and Chemical Resistance Test
Industrial air bellows often operate in harsh environments, requiring exposure tests to ensure durability:
- Testing at extreme temperatures from -40°C to +115°C.
- Submerging in oils, grease, and aggressive chemicals.
- Checking for rubber swelling, hardening, or surface degradation.
- Evaluating resistance to UV exposure and ozone degradation.
Ensuring material integrity under these conditions prevents premature wear and performance loss.
7. Burst Pressure Testing
The burst pressure test evaluates the maximum pressure an air bellow can withstand before failure. The process includes:
- Gradually increasing pressure beyond operational limits.
- Documenting the exact rupture point.
- Ensuring failure occurs at designed locations, not mounting areas.
A bellow must exceed its rated pressure margin to pass this test. If failure occurs too soon, it indicates manufacturing defects.
8. Fatigue Cycle Testing
To assess long-term durability, an air bellow is subjected to repeated stress cycles. The test involves:
- Simulating one million compression-extension cycles.
- Observing structural changes or loss of elasticity.
- Conducting shock load endurance tests.
- Confirming retention of airtight integrity.
A compliant air bellow should maintain performance throughout its expected lifespan.
Regulatory Standards for Air Bellows
Industry standards ensure air bellow compliance and safety. Key regulations include:
- ISO 10846 – Testing for vibration isolation efficiency.
- ISO 19657 – Performance standards for rubber isolators.
- EN 13597 – Compliance methods for industrial air bellows.
- ASTM D412 – Tensile strength assessment of rubber materials.
- SAE J145 – Durability requirements for air spring systems.
Adhering to these standards ensures air bellows perform consistently in real-world applications.
Comprehensive compliance testing is essential for ensuring air bellows perform optimally in industrial and vehicular applications. By conducting pressure tests, dimensional verifications, vibration assessments, and fatigue testing, manufacturers and users can ensure long-term reliability. Following regulatory guidelines prevents failures, reduces maintenance costs, and enhances product efficiency. Advanced testing methods, including real-time monitoring and automated stress analysis, further improve accuracy and predictive maintenance.