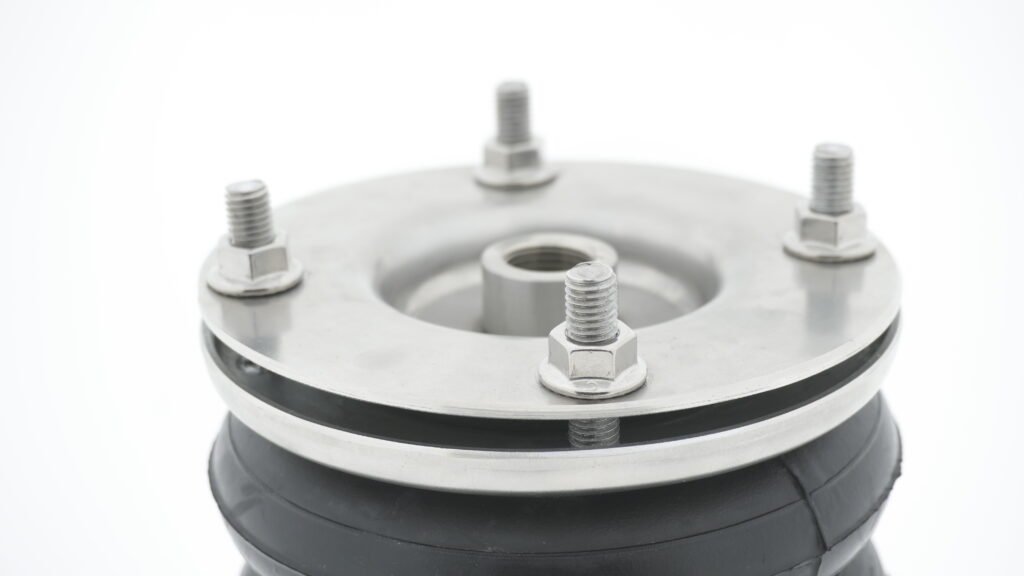
In industrial applications, maintaining operational efficiency in harsh environments is a key challenge. Air bellows are widely used in vibration isolation, load handling, and actuation systems. However, their performance can be compromised when exposed to extreme humidity. Understanding the impact of moisture, condensation, and corrosion on air bellows is crucial for ensuring longevity and reliability in demanding environments. Tevema air bellows are available in various rubber compounds and metal constructions, ensuring durability in challenging conditions. These bellows can withstand working pressures up to 8 bar and maximum loads of 380 kN per unit. Selecting the right material and design is essential for preventing premature failure. The influence of humidity on air bellows is critical, affecting structural integrity, performance, and service life. This article explores how to enhance durability and optimize functionality in humid conditions.
Material Selection for High-Humidity Conditions
To ensure durability in humid environments, the choice of elastomer compounds and metal components plays a significant role. Tevema air bellows are available in various rubber formulations designed to withstand moisture penetration, including:
- Chlorobutyl (CIIR) – Exceptional resistance to acids and moisture.
- Nitrile (NBR) – Superior oil resistance and outdoor performance.
- Ethylene Propylene Diene (EPDM) – Excellent ozone resistance and high-temperature stability.
- Chloroprene (CR) – High weathering resistance and moderate oil resistance.
In addition to rubber selection, metal end plates are available in AISI-304 stainless steel for enhanced corrosion resistance in wet environments. Tevema air bellows can also be supplied with AISI-316L stainless steel, offering superior performance in saline conditions. The use of reinforced fabric layers within the rubber structure increases tensile strength, ensuring structural integrity under heavy loads. These design enhancements prevent water infiltration, reducing the risk of degradation and performance loss over time.
Preventing Moisture-Related Damage
Water ingress can cause internal degradation in air bellows, leading to structural failure. To mitigate this, it is essential to:
- Use stainless steel fittings to prevent corrosion.
- Apply protective coatings on metallic components.
- Store air bellows in dry environments to avoid premature aging.
- Ensure proper drainage in pneumatic systems to prevent water accumulation.
Additionally, Tevema air bellows offer optional polyurethane coatings, further increasing resistance to water absorption and chemical exposure. The use of four-ply construction enhances load-bearing capabilities while reducing the impact of humidity-induced stress. The integration of moisture-repellent additives in the rubber compounds prevents swelling and deformation, ensuring stable mechanical properties. Implementing sealing mechanisms at connection points further reduces moisture penetration, maintaining operational reliability in humid conditions.
Effects of Humidity on Air Bellow Performance
High moisture levels impact air bellow functionality by:
- Reducing elasticity, leading to decreased stroke efficiency.
- Increasing wear on rubber components.
- Causing condensation inside the bellow cavity, leading to internal degradation.
- Accelerating corrosion on metallic parts.
The elongation at break and compression set properties of air bellows are influenced by prolonged exposure to moisture. Tevema air bellows are tested for tensile strength degradation under high-humidity conditions, ensuring material stability. Humidity affects response time, reducing actuator efficiency in precision applications. The presence of moisture-laden air can lead to hydrolysis in certain elastomers, necessitating advanced rubber formulations for long-term reliability. The implementation of high-performance sealing solutions reduces performance loss, ensuring optimal system function.
Best Practices for Air Bellow Maintenance in Humid Environments
To extend the lifespan of air bellows in high-humidity settings, follow these best practices:
- Routine Inspections – Check for cracks, wear, and signs of moisture ingress.
- Use Moisture Filters – Install desiccant dryers to remove excess water from air supply lines.
- Regular Cleaning – Wipe down exposed surfaces to prevent moisture buildup.
- Store in Controlled Environments – Avoid exposure to fluctuating temperatures and high humidity.
- Apply Anti-Corrosion Treatments – Use rust inhibitors on metallic components.
By integrating environmental monitoring sensors, operators can track humidity levels in real time, preventing unexpected failure. Using low-permeability elastomers helps maintain internal air pressure, enhancing system longevity. The incorporation of anti-humidity coatings extends service life, reducing maintenance costs over time. Ensuring proper ventilation around installed air bellows prevents localized condensation, minimizing potential material degradation.
Application-Specific Considerations
Marine and Offshore Industries
In maritime applications, salt-laden air accelerates corrosion. Tevema air bellows made with stainless steel end plates and EPDM rubber are ideal for ship decks, cargo holds, and offshore platforms. These bellows undergo salt spray testing to ensure long-term durability. The use of closed-cell elastomers minimizes water absorption, preventing hydrolysis-induced weakening. Enhanced UV resistance protects against long-term environmental exposure, ensuring stable performance in extreme conditions.
Food Processing and Pharmaceuticals
High humidity is common in cleanrooms and sterile environments. Chlorobutyl air bellows provide superior resistance against sanitization chemicals and steam exposure. FDA-approved rubber compounds ensure compliance with hygiene regulations, making them ideal for food production machinery. The use of non-marking materials prevents contamination risks, ensuring safety in sensitive environments. These bellows are designed for high-temperature washdowns, resisting degradation from frequent cleaning cycles.
Mining and Heavy Industry
Moist underground environments necessitate reinforced air bellows with four-ply rubber construction, ensuring high load capacity and resistance to waterborne particulates. Tevema air bellows feature abrasion-resistant coatings, protecting against dust accumulation and chemical exposure. These bellows are tested under dynamic compression cycles, ensuring long-term endurance in intense industrial settings. With reinforced textile layers, they provide exceptional mechanical resilience against shock loads.
The impact of humidity on air bellows cannot be ignored. By choosing the right materials, implementing maintenance strategies, and utilizing protective coatings, we can extend the lifespan of air bellows in high-moisture environments. Tevema air bellows provide long-term durability, ensuring optimal performance even under extreme conditions.