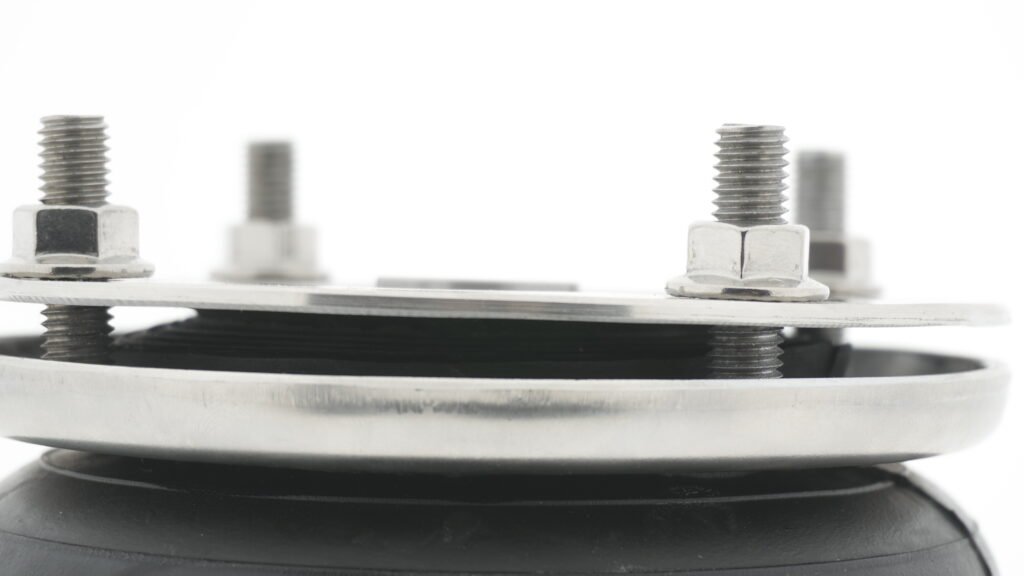
The Evolution of Vehicle Suspension
The automotive industry is experiencing a significant shift in vehicle suspension technology. Traditional coil springs and leaf springs have long been the standard. However, air bellows are rapidly gaining traction due to their superior load capacity, adjustability, and vibration isolation properties.
Air bellows offer improved shock absorption and load management due to their multi-layered elastomeric construction. They are reinforced with nylon cord plies, enhancing durability and pressure resistance. Unlike conventional steel springs, air bellows have an operating pressure range of 4 to 12 bar, depending on construction type. Their low natural frequency (1.5 Hz to 3.5 Hz) ensures effective vibration damping, reducing mechanical stress. The flexible rubber membranes prevent fatigue failure, providing consistent ride quality. These advantages contribute to improved vehicle handling, longer component life, and reduced maintenance costs over time.
Enhanced Comfort and Ride Quality
One of the key reasons behind this transition is the improved ride comfort that air suspension systems offer. Unlike conventional suspension components, which have a fixed spring rate, air bellows dynamically adjust to varying loads and road conditions. This ensures a smooth ride, reducing the impact of road irregularities and enhancing overall driving comfort.
Air bellows maintain constant natural frequency regardless of load changes, ensuring uniform ride performance. By automatically adjusting pressure levels, these systems adapt to terrain variations, preventing excessive vehicle movement. Tests indicate 99% vibration isolation efficiency, making them ideal for luxury vehicles, public transport, and heavy-duty applications. Advanced air management systems regulate internal air pressure, optimizing ride stability. The materials used—such as chloroprene rubber—provide high resistance against ozone exposure and temperature extremes (-40°C to +115°C). With corrosion-resistant bead rings, air bellows maintain structural integrity in harsh environments, extending service life.
Superior Load Handling Capabilities
For commercial vehicles, buses, and heavy-duty trucks, air bellows provide unmatched load distribution capabilities. These systems help maintain a consistent ride height, even under varying payloads, preventing excessive body roll and chassis stress. This load adaptability is crucial for long-haul transportation and freight logistics.
Air bellows support static loads up to 450 kN, depending on convolution type and diameter size. Multi-ply reinforced versions allow safe operation at higher pressures, increasing axle load-bearing capacity. Load-bearing tests demonstrate up to 50% reduced strain on suspension components compared to coil springs. Their low hysteresis ensures efficient energy transfer, minimizing power loss. By reducing chassis vibrations, air bellows enhance cargo stability, preventing load shifting during transit. The ability to adjust suspension stiffness improves handling, ensuring better cornering control and braking stability under heavy loads.
Extended Lifespan of Vehicle Components
Traditional steel springs are prone to fatigue and corrosion, leading to premature wear and costly replacements. In contrast, air bellows are constructed with reinforced elastomeric materials, significantly extending their lifespan. Their ability to absorb shocks and vibrations prevents premature wear on other vehicle components, including wheel bearings, suspension arms, and axles.
Air bellows undergo extensive durability testing, with a fatigue resistance exceeding 3 million cycles under full load conditions. They feature specialized rubber compounds designed for high wear resistance, including EPDM, NBR, and NR/SBR blends. The bead plate assembly consists of electro-galvanized steel or AISI-304 stainless steel, preventing corrosion-related failures. Unlike mechanical springs, which require periodic re-tensioning, air bellows operate maintenance-free, reducing downtime. Their closed air system eliminates friction wear, ensuring a consistent spring rate over years of usage.
Adjustability for Different Driving Conditions
Air suspension systems offer unparalleled adjustability. By modifying air pressure, drivers can optimize vehicle height, improving aerodynamics, fuel efficiency, and off-road capabilities. This feature is particularly beneficial for adaptive suspension systems in luxury cars and performance vehicles.
Vehicles with electronically controlled air suspension can adjust ride height between 30 mm to 250 mm, based on driving mode. Lower settings enhance fuel efficiency, while raised positions improve ground clearance for off-road driving. Advanced height sensors communicate with ECU systems, enabling real-time suspension tuning. Dynamic adjustments optimize shock absorption, reducing driver fatigue on rough terrain. The inclusion of multiple convolution types (single, double, triple) allows manufacturers to tailor performance characteristics for specific driving applications.
The automotive industry is rapidly shifting towards air suspension systems due to their numerous advantages over traditional suspension components. With benefits such as improved ride quality, better load handling, enhanced fuel efficiency, and superior durability, air bellows are becoming the preferred choice for modern vehicles. As technology progresses, we can expect even more refinements and innovations, ensuring a smoother, safer, and more efficient driving experience for all.