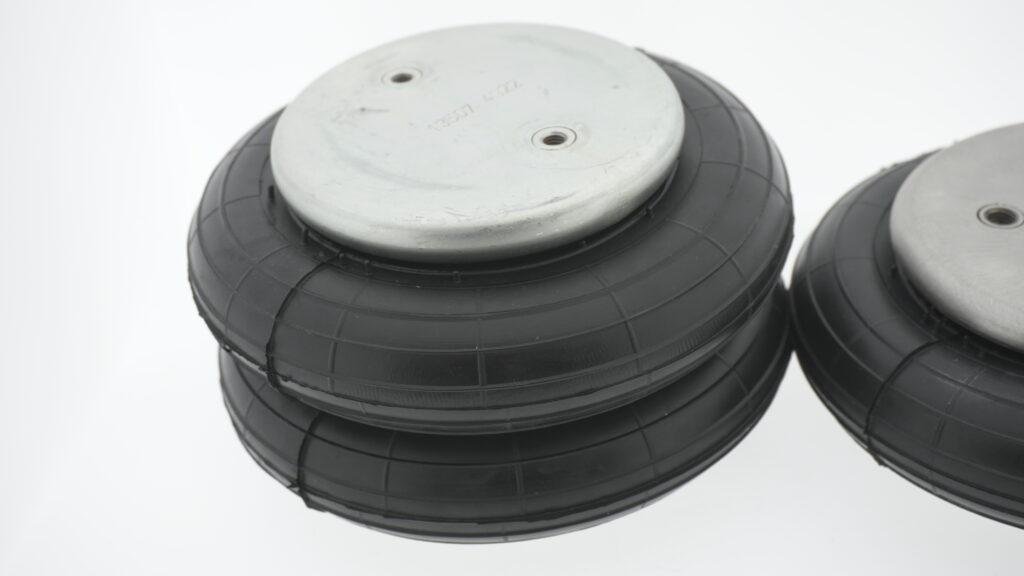
Enhanced Durability and Reliability
Air bellows are designed with reinforced rubber compounds and high-strength fabric plies for long-lasting performance. Unlike hydraulic actuators, which degrade due to seal wear and fluid contamination, air bellows function without dynamic seals, eliminating internal friction. This enhances reliability and reduces maintenance requirements. The vulcanized rubber layers protect against mechanical fatigue, ensuring a longer service life. The absence of oil-based lubricants prevents contamination risks, making air bellows ideal for clean environments. Their resistance to extreme temperatures, abrasion, and chemical exposure further strengthens their durability. Unlike hydraulic cylinders, which require constant lubrication, air bellows rely only on compressed air, reducing component wear. This translates to extended operational life and lower maintenance costs. Moreover, the flexible nature of air bellows allows for misalignment compensation, preventing mechanical stress accumulation. Their sealed construction eliminates fluid leakage, ensuring consistent force application without performance degradation over time.

Minimal Maintenance Requirements
One major advantage of air bellows over hydraulic actuators is their low-maintenance operation. Hydraulic systems require frequent fluid changes, seal replacements, and leak detection. These tasks demand regular monitoring, increasing downtime and operational expenses. Air bellows, however, function solely on compressed air, eliminating fluid management issues. Since air bellows lack moving seals, they do not experience friction-related wear. This ensures longer-lasting performance without frequent repairs. Additionally, hydraulic actuators need precise alignment to prevent seal damage, while air bellows can tolerate misalignment without affecting performance. This makes them more versatile and easier to integrate into existing systems. The simple construction of air bellows also means fewer failure points compared to hydraulic actuators. This directly results in lower repair costs, minimal downtime, and higher efficiency in industrial applications.
Superior Vibration Isolation
Unlike hydraulic actuators, which transmit mechanical vibrations to surrounding components, air bellows provide superior vibration isolation. Their rubber construction and air-filled chambers absorb shocks efficiently. This allows for smoother operations, preventing equipment damage due to excessive vibrations. By isolating vibration frequencies, air bellows extend machine lifespan, reducing stress-induced fatigue. This benefit is especially crucial for high-precision machinery, where stability and low vibration levels are necessary for optimal performance. Additionally, air bellows mitigate noise pollution, improving the workplace environment. Hydraulic actuators, in contrast, produce mechanical noise due to fluid compression and piston movement. By using air bellows, industries benefit from quieter operations, contributing to safer working conditions and reduced acoustic disturbances.
Greater Resistance to Harsh Conditions
Air bellows are highly resistant to environmental stressors, ensuring consistent performance in harsh conditions. Unlike hydraulic actuators, which rely on fluid integrity, air bellows function efficiently in temperature extremes, chemical exposure, and abrasive environments. Hydraulic systems depend on fluid viscosity, which changes with temperature fluctuations. This affects actuator response time and load-bearing capacity. Air bellows, however, maintain stable operation under varied environmental conditions. Manufactured using elastomer compounds such as nitrile, chlorobutyl, and EPDM, air bellows offer excellent chemical resistance. They withstand corrosive agents, oils, and abrasive particles, ensuring long-term reliability. In industries with exposure to harsh chemicals, air bellows provide a more durable alternative to hydraulic cylinders.
Compact Design and Installation Flexibility
Air bellows offer space-saving advantages over hydraulic actuators. Their low-profile design allows for compact installations, making them ideal for applications with space constraints. Unlike hydraulic cylinders, which require piston rods, air bellows generate axial force directly, reducing structural complexity. Additionally, air bellows feature versatile mounting options, including flange fittings, bead rings, and crimped designs. This allows for easy integration into various industrial setups. Unlike hydraulic systems, which demand precise alignment, air bellows adapt to misaligned surfaces without performance loss. Their lightweight nature simplifies transportation and installation, reducing setup costs. In contrast, hydraulic actuators require specialized handling due to heavyweight components. This makes air bellows the preferred choice for space-efficient, high-performance applications.
Lower Operational Costs
Air bellows offer significant cost savings compared to hydraulic actuators. Their energy-efficient operation, minimal maintenance, and long service life reduce overall expenses. Unlike hydraulic systems, which consume large amounts of energy for fluid compression, air bellows operate on compressed air, leading to lower power consumption. Additionally, air bellows eliminate the need for hydraulic fluid purchases and waste disposal, further reducing operational costs. The absence of seals and friction points ensures longer-lasting performance, lowering repair expenses. In industries where cost efficiency is critical, air bellows provide a high return on investment due to their low-maintenance requirements and reduced energy demands. This makes them a smarter choice for businesses looking to optimize resources while maintaining high-performance standards.
For industries seeking efficient, low-maintenance, and cost-effective actuation solutions, air bellows provide a clear advantage over hydraulic actuators. Their durability, reliability, and minimal upkeep requirements ensure long-term performance without frequent replacements. With superior vibration isolation, resistance to harsh conditions, and cost efficiency, air bellows continue to be the preferred choice for industrial applications. By eliminating fluid leakage risks, reducing energy consumption, and ensuring consistent force application, air bellows prove to be more reliable than hydraulic systems in varied operational settings.