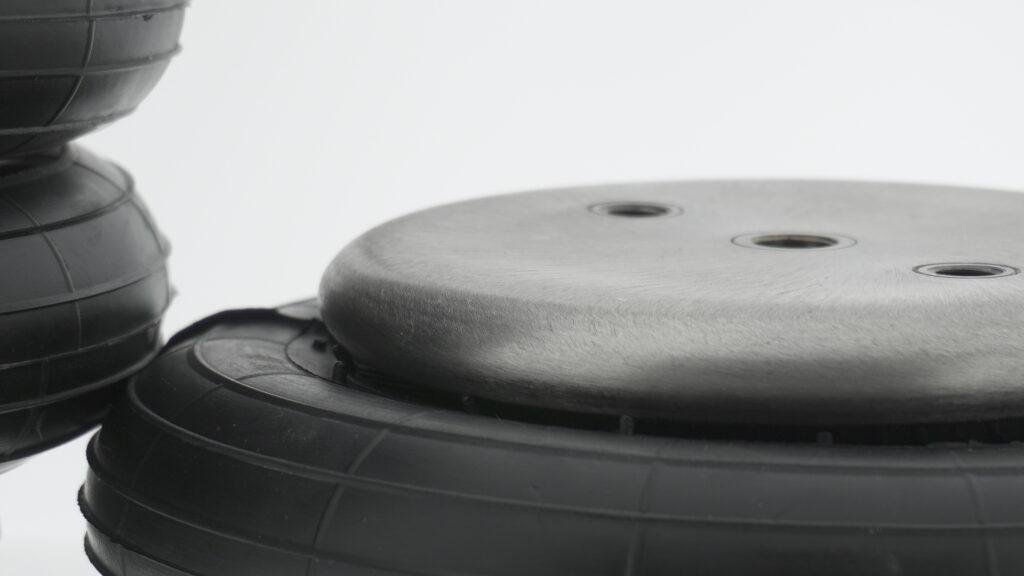
Pressure fatigue due to repeated cycling
One primary cause of what causes air bellows to rupture is excessive pressure cycling under dynamic loads. Standard bellows operate safely up to 8 bar, but many systems unintentionally exceed this. High loads combined with repeated inflation create internal tension on rubber-fabric layers. Cracks form near convolution folds, where bending stress is greatest. Over time, this microscopic damage spreads and weakens the structure. Bellows with four-ply reinforcement can endure 12 bar, increasing rupture resistance. At 7 bar, triple-convolution models generate forces up to 300 kN. Without stable pressure control, even these can rupture. Installing pressure regulators, safety valves, and feedback sensors minimizes load spikes. Air pressure should never exceed 80% of the unit’s maximum rating. Operators often overlook peak loads, which cause sudden failures. We recommend constant monitoring of pressure profiles during operation. Prevention through regulation extends service life significantly. Bellows under stable pressure cycles show fewer signs of fatigue and perform more reliably.
Elastomer failure from incompatible media
Material compatibility is critical in avoiding what causes air bellows to rupture under harsh chemical conditions. Elastomer compounds react differently to exposure media and temperatures. Using Natural Rubber (NR/SBR) with oils causes swelling, cracking, and premature failure. Nitrile (NBR) withstands oils, greases, and outdoor exposure significantly better. In acidic or ozone-rich environments, Chlorobutyl (CIIR) or EPDM maintain elasticity. Temperature ratings vary: NR handles -40°C to +70°C, CIIR goes up to +115°C, and EPDM works to +115°C. Operating beyond these limits hardens or softens rubber layers. Damaged layers expose fabric plies, accelerating internal wear. Elastomer selection must match both chemical and temperature profiles. We assess working media before finalizing product specifications. That includes vapors, mist, and cleaning agents. Failure to match the rubber compound with media leads to costly downtime. Selecting the wrong compound shortens the lifespan and causes avoidable ruptures. Always consult technical guidelines to align compound properties with environmental exposure risks.

Misalignment and incorrect mounting methods
Misalignment and incorrect installation remain key factors in what causes air bellows to rupture during service. Each bellow tolerates limited angular and lateral displacement. Typical designs accommodate up to 30 mm lateral misalignment and 25° tilt. Exceeding these tolerances causes stress concentration on convolution zones. Uneven loads stretch and compress the bellow asymmetrically. This leads to cracking at bead-rubber interfaces. Improper torque on closures worsens alignment issues. We have seen ruptures from over-tightening during installation. Dismountable bead ring systems simplify correct setup, provided the mounting plates are parallel. Torque-controlled installation tools ensure even pressure. Misaligned mounting surfaces introduce shear forces. These forces accumulate at convolution roots. Over time, such loads exceed material limits. Repetitive stress leads to delamination and failure. We use custom jigs to confirm alignment before pressure testing. Installation precision prevents early fatigue. Mounting geometry matters just as much as internal pressure. Correct alignment practices extend operating life and reduce failure incidents in high-load applications.
Extreme temperature impact on rubber integrity
Extreme temperatures are often underestimated in what causes air bellows to rupture during operation. Each rubber compound has defined thermal boundaries. Exceeding these limits reduces material flexibility. Natural rubber becomes brittle under -40°C, forming cracks when flexed. EPDM and CIIR maintain properties up to +115°C, resisting ozone and UV degradation. In heated environments, metal expansion stresses rubber bead zones. Conversely, cold environments stiffen the outer skin. Both scenarios lead to internal delamination. We select elastomers based on measured ambient exposure. In high-heat zones, we use AISI-304 or AISI-316L stainless steel end closures. Stainless components prevent deformation from thermal expansion. High-temperature compounds retain elasticity and compression resilience longer. Each application requires tailored rubber-metal pairing. Long exposure to extreme temperatures accelerates aging. Even when pressure is stable, temperature extremes silently erode material strength. We always advise clients to monitor ambient conditions year-round. This avoids sudden ruptures caused by material transition beyond its design envelope. Prevention ensures sustained elasticity and strength.
Resonance and vibration overload conditions
Vibration-induced resonance is a significant factor in what causes air bellows to rupture in dynamic environments. Every bellow design has a natural frequency, usually between 1.4 and 4.6 Hz. When external machinery matches this frequency, resonance builds. Oscillations increase in amplitude, stressing the convoluted structure. Internal fabric plies experience repeated shear forces. Without damping, this causes rapid fatigue and rupture. At 6 bar, amplified vibration adds destructive kinetic energy. Systems without isolation buffers are vulnerable to early failure. We conduct resonance analysis before specifying a bellow. Choosing units with different natural frequencies avoids alignment with operating machinery. Adding mass or changing damping coefficients shifts the response curve. Low-frequency bellows isolate better under variable loads. We also recommend shock-absorbing mounts in high-vibration areas. Isolation is not optional—it’s essential for long-term stability. Improper damping shortens lifespan dramatically. Proper vibration matching prevents stress buildup. We always consider dynamic frequency before recommending or installing an air bellow system.
Chemical attack and ozone degradation
Chemical exposure and ozone presence significantly contribute to what causes air bellows to rupture in industrial environments. Many facilities use aggressive cleaning agents, solvents, and operate near ozone-producing equipment. These degrade outer rubber surfaces. Early signs include hairline cracks, discoloration, and reduced flexibility. Once the surface is breached, inner fabric plies are exposed. These plies deteriorate rapidly under pressure. Chloroprene (CR) and Chlorobutyl (CIIR) resist ozone and mild chemicals. Still, prolonged exposure without protection causes material fatigue. We advise storing bellows away from ozone-generating equipment. Protective coatings or shields offer additional defense in hostile zones. ISO 2230 guidelines define optimal rubber storage conditions. Dark, dry, and ozone-free areas preserve integrity. Material selection must consider cleaning schedules and nearby emissions. Failure to do so results in unseen damage. Routine inspection of the outer skin reveals early warning signs. Chemical resistance extends beyond rubber type—it includes smart environmental design. Proper placement and shielding prevent premature aging.
Handling errors in end closure installation
Improper handling of end closures is a major factor in what causes air bellows to rupture during setup. Closures include crimped, bead ring, and dismountable designs. Incorrect torque or uneven fitting introduces structural stress. These mistakes deform the bead interface, weakening the seal. This often causes leakage or local tearing. Applying unbalanced force during assembly misaligns the inner plies. A distorted bellow flexes unevenly when inflated. That increases internal strain and fatigue. We recommend using torque-calibrated tools during all installations. Proper closure torque preserves symmetry. Stud patterns must match the plate’s hole geometry. Misalignment at this point compromises long-term integrity. Stainless closures prevent deformation under high torque. We always test bead plate flatness before assembly. Preloaded washers help distribute clamping force evenly. Mishandling during setup causes more ruptures than many realize. Always install closures with care and precision. Correct mounting is vital for pressure retention. A strong seal depends on accurate and uniform mechanical compression.
Storage degradation before installation
Storage conditions are often overlooked in what causes air bellows to rupture before even entering service. Rubber degrades when exposed to heat, UV, ozone, or moisture. Storing bellows near electric motors introduces ozone exposure. UV light triggers surface oxidation and hardens the rubber. High humidity causes internal condensation, weakening adhesive bonds. Bellows should be kept in cool, dry, and dark areas. ISO 2230 outlines best practices for rubber storage. We supply UV-resistant packaging to delay degradation. Still, customers should rotate inventory to minimize shelf aging. Long storage without usage can stiffen the outer cover. This leads to cracking upon first inflation. We recommend periodic inspection of stored units. Look for surface cracking, stiffness, or discoloration. Stainless steel components resist corrosion during long storage periods. Shelf life is not infinite, even if unused. Proper storage equals preserved performance. Once a bellow is compromised in storage, its operational reliability declines. Safe environments protect long-term material integrity.
Internal damage from unfiltered air supply
Contaminated air supply plays a major role in what causes air bellows to rupture during daily operation. Compressed air often carries oil, dust, or water. These contaminants abrade the inner surface during inflation cycles. Fine particles grind away at internal rubber layers. Water accelerates corrosion around metallic closures. Oil degrades adhesion between plies. At 7 bar, even microscopic debris causes significant wear over time. Bellows lacking filters fail faster than filtered systems. We recommend multi-stage filtration: oil separators, desiccant dryers, and particulate filters. Air quality must meet ISO 8573 standards. We also suggest regular inspection of filters. Clogged or saturated filters offer little protection. Filter bypasses or failures often go unnoticed until damage occurs. Clean air improves longevity and prevents internal scoring. Nitrogen is an alternative in moisture-sensitive applications. Clean media equals extended service life. Prevention starts at the compressor—not the bellow. Filtered supply lines are mandatory in precision pneumatic isolation systems.
How to prevent rupture through design optimization
Effective design is the foundation of preventing what causes air bellows to rupture across industries. System conditions must match bellow capabilities. Selection involves convolution type, stroke length, material, and pressure class. For example, triple convolution models handle strokes over 300 mm and loads exceeding 300 kN. We recommend choosing bellows with pressure ratings 25% above maximum system pressure. High-load systems benefit from four-ply reinforced constructions. Material choice is equally critical. EPDM, NBR, or CIIR suit harsh environments. Vibration-prone systems need low-frequency isolation models. Each application has unique thermal, chemical, and dynamic requirements. We analyze these before recommending a configuration. Mounting geometry must support bellow motion without restriction. Misalignment compensation features must be included. Custom solutions increase safety and reduce maintenance. Preventative design combines analysis with field data. Matching product to environment prevents premature failures. Longevity is the result of precise engineering. With the right configuration, rupture risks are minimized by design—not luck.