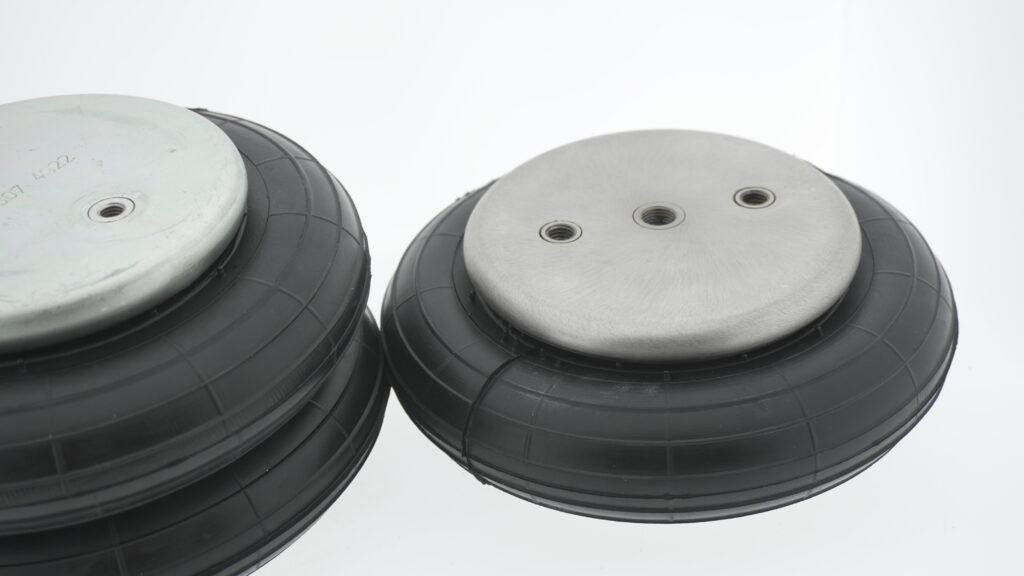
Understanding Wear in Air Bellow Systems
Air bellow systems play a crucial role in industrial applications, offering high durability, load absorption, and vibration isolation. However, like any component subjected to continuous movement and pressure fluctuations, air bellows experience wear over time. Identifying and mitigating deterioration factors ensures optimal performance and extended service life. The main sources of wear in air bellows include material fatigue, pressure fluctuations, environmental exposure, and mechanical stress. Each of these factors contributes to progressive degradation, affecting the reliability and functionality of the system. Regular inspections, maintenance routines, and the use of high-quality materials help to minimize premature failures. Without proper care, air bellows can suffer from cracking, loss of flexibility, and structural weaknesses. Addressing these concerns ensures long-term operational stability and cost efficiency. This article examines common wear factors, preventative measures, and best practices for maintaining air bellow systems.

Material Fatigue and Aging
The primary cause of degradation in air bellows is material fatigue. Elastomeric compounds, such as natural rubber, nitrile, and EPDM, experience wear due to repeated stress cycles. Each cycle of compression and expansion leads to microscopic cracks, gradually reducing structural integrity. Over time, these cracks propagate, leading to potential failure. The choice of high-quality rubber with reinforced fabric plies significantly reduces fatigue-related failures. In addition to stress-related wear, aging effects impact elasticity and performance. Exposure to ozone, UV radiation, and chemicals accelerates rubber hardening. This process reduces flexibility and increases the likelihood of fractures. Protecting air bellows from harsh environmental conditions helps to extend service life. Proper storage in cool, dark, and dry environments prevents premature deterioration. Using ozone-resistant materials enhances durability in demanding industrial settings. Regular visual inspections help detect early signs of fatigue, allowing for timely replacement before failure occurs.
Pressure Fluctuations and Overloading
Exceeding the recommended pressure limits accelerates wear by causing internal stress concentrations within the reinforced layers. Standard air bellows operate within 8-bar pressure, but four-ply reinforced designs allow higher pressure resistance up to 12-bar. Ensuring correct air pressure regulation prevents premature wear and deformation. Frequent pressure changes introduce stress variations, leading to weakened rubber compounds and increased risk of rupture. Overloading places additional strain on the structural components, shortening lifespan and reducing mechanical efficiency. Proper pressure monitoring and load distribution mitigate these risks. By adhering to manufacturer specifications, users can avoid excessive force that weakens rubber integrity. Implementing pressure regulation systems reduces shock loading, improving long-term durability. Additionally, using reinforced mounting structures helps prevent distortions caused by irregular pressure variations. Maintaining stable operating conditions significantly enhances performance reliability. Regular maintenance checks ensure optimal functionality and reduce failure rates in high-pressure environments.
Environmental and Chemical Exposure
Industrial environments expose air bellows to corrosive substances, including oils, solvents, and cleaning agents. Some rubber types, such as chlorobutyl and nitrile, provide enhanced chemical resistance, reducing swelling and softening. Chemicals can penetrate rubber layers, altering elasticity and causing deterioration. Ensuring that air bellows operate in controlled environments minimizes damage. The use of stainless steel end plates enhances durability in harsh conditions, preventing corrosion-related failures. High moisture levels also accelerate rubber degradation, leading to surface cracking and loss of mechanical properties. Temperature variations further affect air bellow integrity, causing shrinkage or expansion. Using weather-resistant elastomers mitigates external influences. In environments where extreme chemicals are present, selecting specialized rubber formulations is essential. Protective coatings further enhance resistance, ensuring extended lifespan and consistent performance. Regular chemical exposure assessments help in predicting potential wear factors, allowing for preventative action before significant damage occurs.
Vibration and Dynamic Stress
Continuous vibrations induce micro-movements, leading to abrasion at the mounting interfaces. While air springs effectively dampen shocks, incorrect alignment results in uneven stress distribution, increasing wear rates. Poorly secured mounting structures cause friction points, reducing service life. Proper installation and alignment adjustments mitigate vibration-induced degradation. When subjected to continuous dynamic stress, air bellows develop localized weak spots. These areas experience accelerated material fatigue, leading to early failures. Reinforcing mounting points with shock-absorbing materials reduces stress impact. Additionally, air bellows should be periodically realigned to avoid asymmetrical pressure distribution. Using precision-engineered mounting brackets enhances stability, improving overall durability. Adjusting air pressure to dampen excessive vibrations further extends operational lifespan. Regular condition monitoring detects early-stage wear, enabling timely interventions. Preventing uncontrolled movements within the system ensures optimal efficiency and long-term operational effectiveness.
Temperature Variations
Air bellows are designed to operate within a specific temperature range. Extreme heat or cold affects the rubber elasticity, leading to brittleness or softening. High-temperature elastomers such as EPDM withstand elevated heat exposure, while chlorobutyl compounds maintain resilience in extreme cold environments. Excessive thermal expansion and contraction weaken structural integrity, accelerating degradation rates. Temperature fluctuations also affect air pressure consistency, impacting operational efficiency. Air bellows in outdoor settings require additional insulation to prevent temperature-induced wear. Using heat-resistant coatings further improves thermal stability, ensuring sustained performance. Selecting the right elastomer compound for specific applications prevents unexpected failures. Proper ventilation systems help maintain stable temperatures, reducing strain on rubber components. Regular temperature monitoring and protective measures enhance longevity and prevent premature breakdowns in thermally dynamic environments.
Maintenance Strategies for Longevity
To maximize the service life of air bellows, regular inspections and preventive maintenance are essential. Recommended practices include:
- Pressure monitoring to prevent overloading
- Surface cleaning to remove chemical contaminants
- Lubrication of mounting interfaces for smooth movement
- Periodic replacement based on usage cycles and wear indicators
Implementing a structured maintenance plan ensures reliable performance. Addressing early signs of degradation reduces replacement costs and extends product lifespan. Proper storage conditions further prevent premature aging. Selecting compatible elastomers for specific applications enhances wear resistance. Routine inspections help detect potential vulnerabilities, allowing for proactive interventions before failures occur.
Understanding the wear and tear mechanisms in air bellow systems allows for proactive maintenance and optimized performance. By selecting durable elastomers, maintaining proper pressure, and ensuring correct alignment, businesses can extend the operational life of their air bellows and achieve cost efficiency.