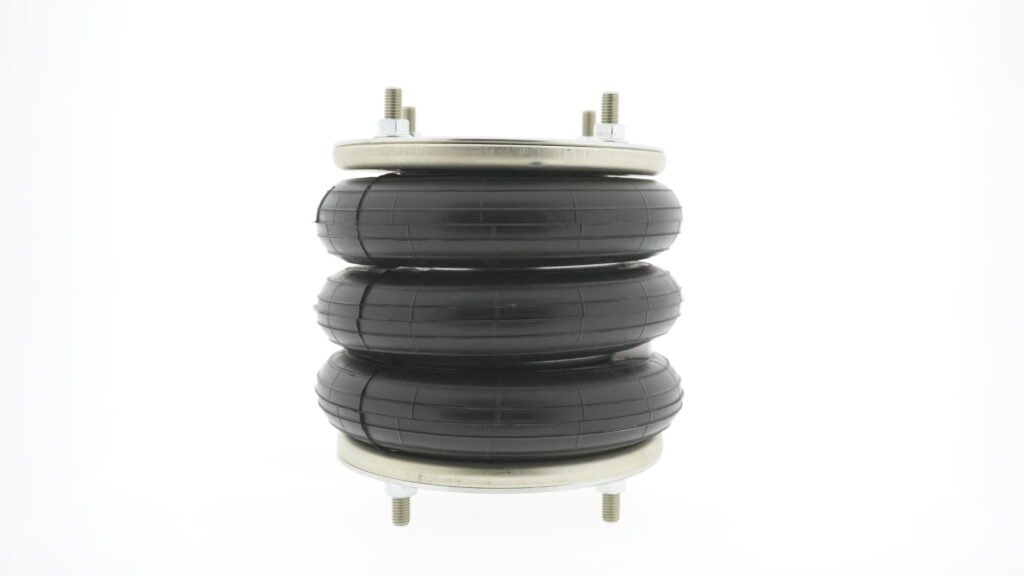
The Role of Air Bellows in Preventing Equipment Damage
In our industry, air bellows play a crucial role in safeguarding equipment from damage. These components are essential for ensuring the longevity and efficiency of various machines. At Tevema, we specialize in designing and manufacturing high-quality air springs that meet the rigorous demands of industrial applications.
Importance of Air Bellows in Equipment Protection
Air bellows are vital in absorbing shocks and vibrations, which can otherwise lead to significant wear and tear on machinery. By mitigating these forces, air bellows help maintain the structural integrity of equipment, thereby extending its operational life.
Key Benefits of Using Air Bellows
- Vibration Isolation: Air bellows effectively isolate vibrations, preventing them from transferring to sensitive components.
- Shock Absorption: They absorb shocks from sudden impacts, reducing the risk of damage.
- Load Distribution: Air bellows distribute loads evenly, minimizing stress on individual parts.
- Flexibility: Their flexible nature allows for slight misalignments without compromising performance.
“The important thing is not to stop questioning. Curiosity has its own reason for existing.” – Albert Einstein
Technical Specifications and Considerations
When selecting air bellows, it is essential to consider the following technical aspects:
Pressure and Load Capacity
Tevema air bellows are designed to operate at a maximum pressure of 8 bar. For applications requiring higher pressures, we offer a four-ply construction capable of withstanding up to 12 bar. This increased capacity allows for greater force application without compromising safety.
Material Composition
The choice of material for air bellows depends on the specific application requirements. Tevema offers air bellows in various elastomer compounds, including:
- Natural Rubber (NR/SBR): Suitable for temperatures ranging from -40°C to +70°C.
- Chlorobutyl (CIIR): Excellent resistance to acids, with a temperature range of -30°C to +115°C.
- Nitrile (NBR): Ideal for applications involving oils and fuels, with a temperature range of -25°C to +110°C.
- Ethylene Propylene Diene (EPDM): Resistant to high temperatures and ozone, suitable for -20°C to +115°C.
- Chloroprene (CR): Offers good weather resistance and moderate oil resistance, with a temperature range of -20°C to +110°C.
Installation and Maintenance
Proper installation and maintenance are critical to the performance and longevity of air bellows. Key steps include:
- Ensuring Adequate Clearance: Avoid sharp materials or surfaces that could damage the bellows.
- Regular Cleaning: Use water, soap, or alcohol to clean the bellows, avoiding abrasive or solvent-based cleaners.
- Inspection: Regularly check for wear, cracks, or damage to the bellows and associated pneumatic components.
“Science is a way of thinking much more than it is a body of knowledge.” – Carl Sagan
Applications of Air Bellows
Air bellows are used in a wide range of applications, including:
- Industrial Machinery: To isolate vibrations and absorb shocks in heavy machinery.
- Automotive Industry: In suspension systems to enhance ride comfort and vehicle stability.
- Aerospace: For vibration isolation in sensitive equipment and instruments.
- Construction Equipment: To protect hydraulic systems and other critical components from shock and vibration.
Detailed Application Examples
Industrial Machinery
In industrial settings, air bellows are crucial for maintaining the smooth operation of heavy machinery. They help in reducing the impact of vibrations and shocks, which can cause misalignment and wear in mechanical components. By using air bellows, we can ensure that machinery operates efficiently and with minimal downtime.
Automotive Industry
In the automotive sector, air bellows are integral to the suspension systems of vehicles. They provide a cushioning effect that enhances ride comfort and stability. This is particularly important in commercial vehicles that carry heavy loads, as it helps in maintaining control and reducing wear on the suspension components.
Aerospace
In aerospace applications, air bellows are used to isolate vibrations in sensitive equipment and instruments. This is critical for maintaining the accuracy and reliability of these devices, which can be affected by even minor vibrations. By using air bellows, we can protect these instruments and ensure their optimal performance.
Construction Equipment
Construction equipment often operates in harsh environments where it is subjected to significant shocks and vibrations. Air bellows help in protecting hydraulic systems and other critical components from these forces, thereby extending the life of the equipment and reducing maintenance costs.
In conclusion, air bellows are indispensable in preventing equipment damage by isolating vibrations, absorbing shocks, and distributing loads evenly. At Tevema, we are committed to providing high-quality air springs that meet the diverse needs of our clients. By understanding the technical specifications and proper maintenance practices, we can ensure the optimal performance and longevity of our air bellows.