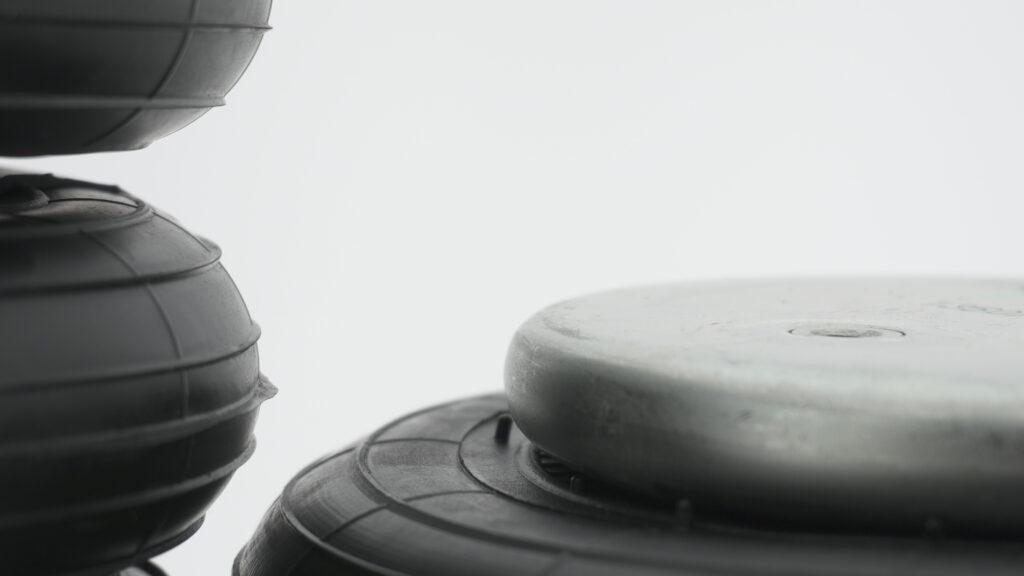
In industrial environments requiring vibration isolation or variable-load actuation, the importance of size customisation in air bellow performance is evident. Poor sizing leads to suboptimal functionality and potential failure. At Tevema, we engineer air bellows tailored to precise application needs. Choosing the wrong diameter or convolution count causes load imbalance and premature wear. Key dimensions like stroke, maximum height, and natural frequency must be correctly matched. The selected closure type, either bead ring or crimped, affects installation and flexibility. A standard triple convolution unit delivers 31 kN at 7 bar within 100 mm height. Our team ensures each design supports motion control, low vibration, and space constraints. Correct sizing also improves reliability and longevity. Systems requiring low-profile actuators benefit from our compact models. Customised bellows help maintain performance during varying operational demands. By designing precisely, we meet load, pressure, and environmental requirements. That’s the power of size customisation in modern engineering.
Understanding dimensional impact on vibration isolation
For vibration isolation, size customisation determines the natural frequency, directly affecting vibration dampening performance. Wrong sizing results in higher frequencies and poor isolation. At Tevema, we adjust diameter, convolution type, and design height to stabilize system response. Larger bellows with multiple convolutions can reach 1.58 Hz at 73 kN under 7 bar. End closures and mounting threads must precisely match the application’s structure. This guarantees mechanical integrity and operational consistency. By fine-tuning stroke and load parameters, we enhance vibration control. Material rigidity and flexibility also influence isolation capability. Our models achieve more than 99% vibration reduction in controlled testing. Engineers choose configurations based on load distribution, space, and mounting positions. Double and triple convolution units provide more flexibility and stroke, crucial for isolating heavy, dynamic loads. Incorrect sizing leads to instability and failure. That’s why size customisation is central in developing air bellows designed to absorb unwanted mechanical vibrations effectively and consistently.
Importance of diameter and convolution choice
Diameter and convolution selection significantly influence the performance of air bellows in demanding environments. Our bellows range from 80 mm to 950 mm in diameter. These cover forces from 0.5 kN to 450 kN. Custom stroke lengths vary between 36 mm and 400 mm, depending on operational needs. Single convolution units offer stiffness and low profile. Triple convolution units provide greater flexibility and extended movement. For example, a double convolution model achieves 12.8 kN at 7 bar, fitting within 75 mm height. Convolution choice affects height, stroke, and natural frequency. Smaller units suit precision tools, while larger ones handle industrial loads. Our engineers analyze load, frequency, and motion parameters to determine the ideal setup. Undersized bellows cause instability, while oversized units may waste space and material. Correct customisation ensures peak performance across the full load range. We recommend precise design analysis before selection. That’s why size customisation is vital for optimal force distribution and stroke control.
Role of end closure types in design flexibility
End closures determine how air bellows interface with machinery. We offer crimped, bead ring, and dismountable closures. Each type affects serviceability and integration. Crimped closures are compact and durable, suited for fixed installations. Bead rings allow replacement and quick maintenance. Dismountable designs offer flexibility in dynamic applications. Threaded ports range from G1/4 to G3/4, depending on airflow needs. Mounting hole sizes vary with load and diameter. These details are essential in achieving a precise fit. Size customisation includes choosing correct closure formats to ensure seamless integration. Mismatched threads or hole patterns can cause leaks and misalignment. Correct port alignment improves airflow, reducing delays in actuation. Our design process ensures that each unit aligns with system specifications. From mounting holes to port size, every element is adjusted to the application. This approach reduces downtime and simplifies assembly. Size customisation in closure design ensures mechanical stability and optimal performance across diverse environments and requirements.
Optimizing stroke length for mechanical efficiency
Stroke length is essential for effective motion and controlled actuation. Our designs accommodate strokes from 36 mm to 452 mm, tailored by diameter and convolution. A triple convolution unit can offer 300 mm stroke and 44.4 kN force at 7 bar. We select stroke based on required displacement, compression, and motion speed. Longer strokes increase flexibility but reduce stiffness. Shorter strokes offer faster, more rigid responses. Our engineers balance stroke with required natural frequency and durability. Frequencies under 2.5 Hz enhance vibration absorption. Oversized strokes risk mechanical failure or misalignment. Undersized strokes limit travel and reduce functionality. Stroke calculations also factor in cyclical fatigue and durability. Proper size customisation ensures safe and efficient stroke control. Each bellows design is engineered for the precise stroke needed. We optimize every parameter, from inner pressure to stroke range. This tailored approach improves mechanical efficiency and long-term reliability under dynamic and repetitive movements.
Matching material specifications to size requirements
Material choice complements size customisation, ensuring performance under varying temperatures, media, and pressure levels. We offer elastomers like EPDM, NBR, CIIR, and CR. Each material resists different hazards, including oil, weather, and chemicals. For high loads, we offer four-ply constructions for additional strength. These models reach up to 12 bar working pressure and 300 kN of force. Steel options include electro-galvanized for standard use or AISI 304/316L stainless steel for corrosive environments. Size influences material thickness and reinforcement layer count. Small units need flexible yet durable compounds. Large bellows demand strength, elasticity, and heat resistance. Matching compound to diameter prevents ruptures and wear. Our engineers adjust material properties to vibration, pressure, and media exposure. Chemical compatibility is vital to long-term function. Incorrect material pairing can compromise seal integrity or structure. That’s why size customisation always includes material selection. From compound to reinforcement, every layer supports mechanical, chemical, and thermal performance criteria.
Balancing compact height with load requirements
Achieving high force in compact spaces requires thoughtful sizing. Bellows must deliver stroke and load within strict height constraints. Compact units can produce 27.1 kN at 7 bar, with a minimum height of 75 mm. Larger bellows exceed 67 kN while retaining short compressed profiles. Height is adjusted by convolution count and plate size. Lower natural frequencies are maintained through strategic diameter-to-height ratios. Our engineers calculate minimum and maximum height per project. Proper sizing improves fit and load transmission. Misalignment occurs if stroke exceeds height limits. Space-constrained environments require careful selection of bellow height and load output. Port positioning and mounting geometry are also tailored. Every detail is measured against system drawings. That precision avoids field modifications or misfits. Size customisation ensures even heavy loads can be isolated in confined systems. With tight vertical tolerances, accurate bellows sizing maintains stroke, safety, and stability without exceeding available mechanical envelope limits.
Enabling modular system integration with custom sizing
Tevema’s size customisation simplifies modular integration across industrial systems. Our bellows match hole patterns, port positions, and layout requirements. Port threads range from G1/4 to G3/4, and fastener configurations are tailored for each application. Designs are adapted to fit plates, mounts, and motion paths. For example, a unit offering 125 mm height and 75 kN can operate in parallel systems. Alignment eliminates stress, motion imbalance, or failure. Modular compatibility lowers installation time. Each bellow’s dimensions are adjusted to existing hardware and structural interfaces. We ensure mounting holes, stroke limits, and thread orientations match equipment geometry. Adjusted sizing supports uniform actuation across multi-point applications. In dynamic systems, bellows must synchronize precisely. Improper fit causes mechanical lag and system stress. Tevema engineers develop bellows to match both mechanical and control system needs. That’s why size customisation supports speed, reliability, and adaptability. It ensures each component operates in harmony within complex, integrated machinery environments.