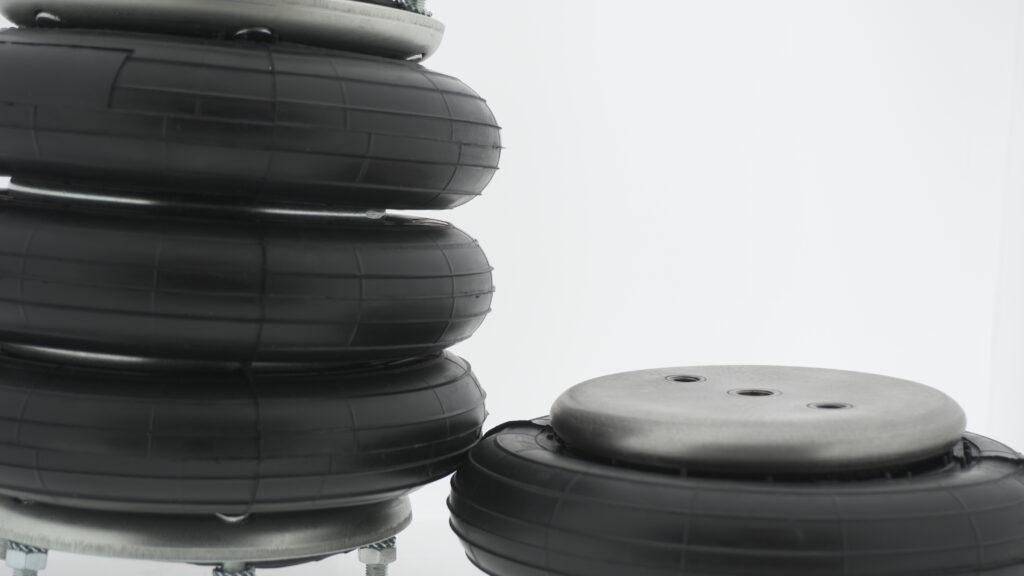
Precision manufacturing demands reliable vibration isolation, stable height control, and consistent load support under demanding conditions. Our tailored air bellows for precision manufacturing systems deliver robust, flexible, and efficient operation for high-precision applications. These components integrate seamlessly with sensitive machinery, offering modular configurations that promote adaptability. Constructed with advanced elastomers and reinforced structures, our designs outperform traditional springs in service life and control precision. Each bellow is engineered for easy maintenance and low wear, reducing unplanned downtime. Their compact design enables installation where space is limited without sacrificing mechanical integrity. Mounting configurations and ports follow industry standards, which simplifies design and replacement tasks. They maintain alignment under lateral loads, resist distortion under compression, and deliver axial motion without vibration. This article outlines the design, material specifications, and technical advantages that define our offering. We help engineers solve isolation, load balancing, and motion control challenges by providing long-term solutions for stability and uptime.
Design advantages of tailored air bellows
Our tailored air bellows for precision manufacturing systems include dismountable designs, bead ring closures, and crimped formats tailored for flexible integration. Dismountable versions use top and bottom plates clamped with bead rings, making disassembly and maintenance straightforward. Bead ring assemblies come in socket head, threaded, and countersunk formats, which attach directly to machinery. Crimped models use sealed ends for applications requiring permanent, tamper-proof performance. Each closure type delivers airtight seals and dimensional precision for demanding operations. Natural frequencies range between 1.2 Hz and 4.6 Hz, depending on model and load conditions. Stroke lengths span 20 mm to 400 mm, accommodating short and long travel needs. Standard port threads and bolt patterns simplify retrofitting in new or existing equipment. These modular elements allow engineers to tailor actuator characteristics to exact mechanical requirements. Whether isolation, actuation, or alignment correction is needed, our bellows provide a scalable and versatile mechanical interface.
Performance under pressure and load conditions
Our tailored air bellows for precision manufacturing systems come in standard and reinforced four-ply designs supporting pressures up to 12 bar. Load capacity ranges from 2.4 kN to 452 kN, depending on diameter, ply count, and mounting configuration. Available formats include single, double, and triple convolutions optimized for space and force requirements. The bellows maintain steady performance when subject to pressure cycles, minimizing motion variation across operating ranges. Heights start at 50 mm, ideal for low-clearance applications. Many units offer a 3:1 stroke-to-height ratio, enabling compact systems with long-range actuation. Standard ports range from G1/4” to G3/4”, and common thread options include M8 and M10, simplifying integration. Each model is tested for leak resistance, stroke repeatability, and deflection stability under dynamic conditions. Our engineering approach ensures high efficiency, with minimal hysteresis and rapid return characteristics across variable system demands and cyclic pressure scenarios.
Material selection for durability and adaptability
The tailored air bellows for precision manufacturing systems use elastomers chosen for industrial durability, chemical resistance, and thermal stability. Materials include natural rubber (NR/SBR) for flexibility, chlorobutyl (CIIR) for acid exposure, nitrile (NBR) for oil resistance, EPDM for ozone and heat, and chloroprene (CR) for outdoor use. Temperature tolerance spans -40°C to +115°C, depending on material type. Fabric-reinforced layers increase tensile strength and shape retention under load and pressure. Each unit is vulcanized into a seamless, crack-resistant structure that withstands vibration and repeated cycling. Metallic components include electro-galvanized steel, AISI-304 stainless, and optional AISI-316L stainless steel for chemical exposure. These finishes resist oxidation, industrial cleaners, and moisture intrusion during continuous use. By combining optimized elastomer blends with rugged end plates, the bellows provide consistent performance. They maintain shape and air tightness in environments where load demands, temperatures, and chemical exposure fluctuate during operation.
Benefits for isolation and noise reduction
Our tailored air bellows for precision manufacturing systems offer vibration isolation exceeding 99%, helping stabilize processes and safeguard sensitive systems. They maintain consistent natural frequency under load shifts, reducing resonance effects in dynamic machinery. Their rubber membranes absorb vibration in all directions, including axial and lateral movement. Units tolerate 30 mm lateral offset and 25° angular misalignment, eliminating the need for additional guides or compensators. This mechanical flexibility simplifies design and reduces cost in systems with tight alignment tolerances. Their vibration-damping characteristics lower structural noise transmission, improving the working environment and protecting sensors or equipment. These features benefit high-precision systems requiring continuous accuracy and minimal noise interference. Compared to rigid isolators, our bellows deliver softer, more responsive control with no stick-slip issues. This results in longer component lifespan, reduced error rates, and better motion consistency throughout repeated cycles in harsh production environments.
Cost-efficiency and long-term value
Our tailored air bellows for precision manufacturing systems offer lower total cost of ownership by combining durability, maintenance-free operation, and affordable setup. Unlike traditional cylinders with seals and friction points, our bellows operate cleanly using pressurized air. This eliminates lubrication needs and internal part wear, extending maintenance intervals significantly. Standard mounting heights from 50 mm enable installation in compact frameworks without compromising stroke capacity or force output. Threaded ports and fasteners, including G-series threads, M8, and M10, reduce the need for special adapters. Their simple structure allows for easy inspection and rapid swap in modular production cells. Four-ply versions support higher pressure ranges and more frequent cycling without deformation. These capabilities lower replacement rates, minimizing downtime and lifecycle costs in process-critical applications. Modular features support reuse or scaling in evolving machine designs. Engineers benefit from reliability, compatibility, and efficiency—all delivered in a robust, streamlined component.
Product range and configuration options
We supply tailored air bellows for precision manufacturing systems in single, double, and triple convolution formats, each offering distinct performance advantages. Outside diameters range from 80 mm to 950 mm, allowing force capacity tuning for specific equipment classes. Design variations include removable closures, crimped fixed ends, and bead-ring mountings for tool-free installation. End components are available in galvanized steel, stainless steel, or aluminum, suited to environmental exposure and weight requirements. Strokes span 20 mm to 400 mm, covering short displacement to long-travel needs. Natural frequencies from 1.2 Hz to 4.6 Hz ensure broad vibration control coverage. Port threading and bolt hole placements are standardized, reducing engineering effort and ensuring consistent alignment. Some variants include studs or blind nuts for direct fastening. These options simplify inventory management and streamline the selection process, enabling seamless integration across diverse applications and industries.
Technical specifications and customization support
Each of our tailored air bellows for precision manufacturing systems comes with technical data to support design validation and system planning. Parameters include stroke range, diameter, pressure rating, height, natural frequency, and mounting thread sizes. All units undergo pressure and cycle testing under dynamic conditions to ensure leak-free, consistent operation. Engineers can request alternate rubber types, steel grades, thread formats, or mounting geometries as needed. Our technical staff assist with special projects, matching mechanical and pneumatic specs with required performance outputs. Documentation supports multiple languages and formats, useful for international OEMs and compliance purposes. Models with non-standard hole patterns or extended stroke-to-height ratios are available upon request. Port sizes and air inlet locations can be adapted for integration with advanced control systems. Our engineering team ensures design feasibility and compatibility before finalizing production, making each configuration a high-performance, application-specific solution.
Why engineers trust our air bellows
Engineers trust our tailored air bellows for precision manufacturing systems because they consistently meet mechanical, environmental, and integration expectations. Units feature fabric-reinforced membranes and pressure-resistant closures tested under real-world conditions. Their flexibility absorbs misalignment and shock, reducing wear on connected components. Mounting plates support common standards for port locations, bolt circles, and thread compatibility. This ensures fast replacement and seamless design updates. These bellows handle dynamic loads, thermal shifts, and high-frequency cycles with minimal degradation. Dimensional tolerances are strictly controlled during production for repeatability and safety. Each model includes specification sheets for pressure, vibration isolation, material type, and movement range. Our multilingual support and experienced technical advisors help teams meet design milestones quickly. Whether used in automation, machine tooling, or industrial vibration control, our bellows deliver precise, dependable function. They preserve uptime, protect sensitive parts, and reduce vibration-related wear, ensuring peak performance across critical manufacturing systems.