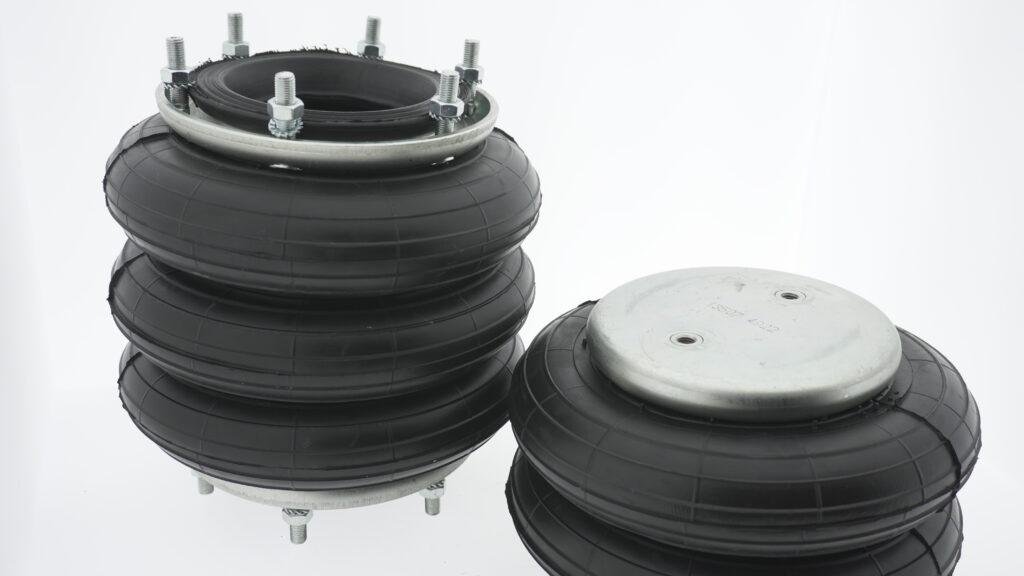
Smart air bellows in factories are transforming industrial automation by making operations smarter, safer, and more efficient. Smart air bellows in factories integrate sensors that monitor load, pressure, and system conditions continuously. These sensors allow real-time adjustments, ensuring machines operate at their most efficient settings. Consequently, facilities experience reduced energy use, extended equipment lifespan, and fewer unexpected failures. Furthermore, predictive maintenance becomes possible, minimizing downtime and maintenance costs across production lines. The integration of smart air bellows in factories also contributes to sustainability efforts by optimizing resource consumption. Along with efficiency gains, these systems improve workplace safety by detecting faults early. Additionally, they simplify the management of vibration isolation in complex industrial environments. Smart connectivity ensures seamless communication between air bellows and broader factory automation networks. Therefore, adopting smart air bellows in factories is a strategic move for companies embracing Industry 4.0 and sustainable operational excellence.
Real-time monitoring with smart air bellows in factories
Real-time monitoring through smart air bellows in factories delivers major benefits for industrial operations. Smart air bellows in factories provide live updates on pressure, load, and temperature, allowing immediate corrective actions. Data from these systems improves decision-making and optimizes production processes. Instant alerts warn operators about deviations before equipment damage occurs, enhancing reliability. Scheduled maintenance becomes more accurate because real-time data reveals the true wear conditions of components. This proactive approach reduces unnecessary servicing, saving time and money. Furthermore, historical monitoring data supports predictive analytics, highlighting long-term system trends and performance opportunities. Remote access capabilities enable supervisors to oversee multiple facilities from one control center. Smart dashboards provide easy visualization of key performance indicators, improving responsiveness. Besides operational benefits, real-time monitoring strengthens compliance with industry safety and quality standards. Implementing smart air bellows in factories leads to smarter operations, higher productivity, and better resource management.
Seamless integration of smart air bellows in factories
Seamless system integration is essential for unlocking the full potential of smart air bellows in factories. Smart air bellows in factories use industrial protocols like OPC UA and MQTT for fast, reliable communication with factory systems. These protocols allow easy connectivity to existing MES and SCADA systems without major infrastructure changes. Integrated air bellows automatically adjust operating parameters based on live process data. Cloud-based platforms store and analyze information for optimization and performance forecasting. Local edge computing ensures fast response times while reducing network loads. Smart air bellows also synchronize with maintenance management systems for streamlined scheduling. Moreover, modular system architectures guarantee flexibility and scalability as factory demands evolve. Integrated solutions simplify troubleshooting and increase operational transparency. Seamless integration improves responsiveness, boosts energy savings, and enhances equipment reliability. Therefore, smart air bellows in factories are crucial components of next-generation smart manufacturing ecosystems.
Sustainability and cost efficiency with smart air bellows in factories
Sustainability and cost efficiency are powerful drivers for implementing smart air bellows in factories. Smart air bellows in factories actively optimize compressed air usage, reducing energy demand without sacrificing performance. Dynamic load adjustments save compressed air during low-demand periods, translating into direct financial savings. Predictive maintenance minimizes resource use by targeting interventions only when necessary. This approach reduces spare part consumption, lowers repair waste, and cuts downtime significantly. Additionally, long equipment lifespans decrease the need for frequent replacements, further conserving materials and energy. Environmental reporting improves because real-time data captures operational emissions and efficiency rates accurately. Companies using smart air bellows gain strategic advantages in meeting sustainability standards. Cost reductions from energy savings and maintenance efficiencies enhance profitability. Through smart resource management and improved operational control, smart air bellows in factories support a greener, more financially resilient industrial future.