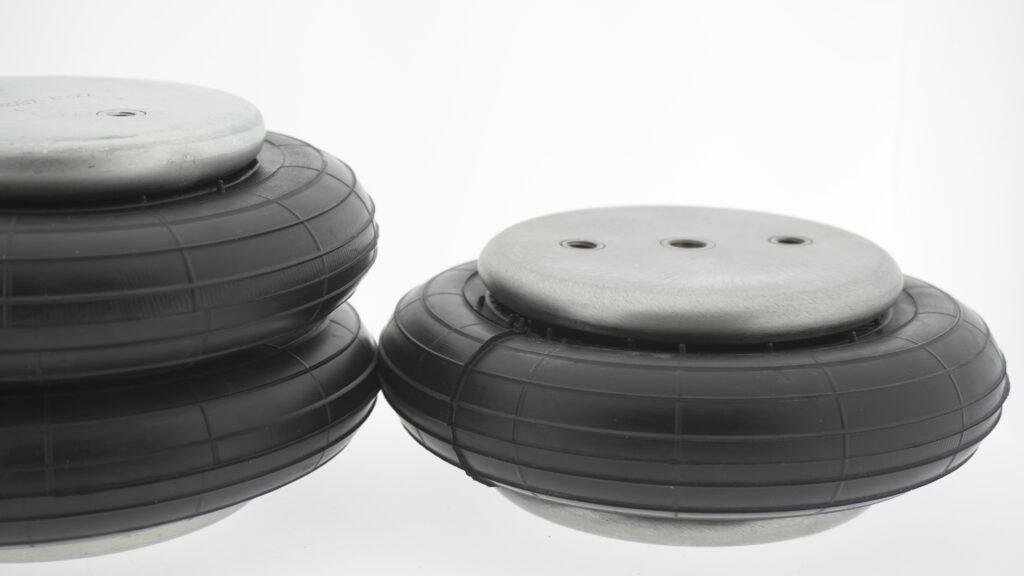
Understanding Safety Checks in Air Bellow Suspensions
Ensuring the reliability of air bellow suspensions requires a structured approach to safety checks. These components are essential in industrial applications, where precision, durability, and load-bearing efficiency determine operational effectiveness. Implementing strict inspection protocols improves performance, extends service life, and reduces failure risks.
Air bellows typically function under pressures up to 8 bar, with four-ply versions supporting up to 12 bar for higher loads. The rubber compounds include NR/SBR for flexibility, NBR for oil resistance, and EPDM for heat endurance. Ensuring correct installation alignment prevents asymmetrical load distribution, reducing premature wear. Selecting the proper mounting hardware, such as bead rings or crimped closures, impacts structural integrity. Corrosion-resistant materials like stainless steel AISI-316L provide protection in harsh environments. Adhering to these principles ensures optimal performance and longevity in critical applications.

Pre-Installation Inspections
Before installing an air bellow suspension, detailed pre-installation checks must be performed to confirm integrity and compatibility. The surface structure should be inspected for cracks, deformations, or defects that may compromise mechanical stability. The mounting points, bead rings, and end closures should match design specifications to ensure a secure fit.
- Examine rubber consistency for material flaws.
- Verify the metallic end closures align with attachment tolerances.
- Inspect fastening areas for misalignments that cause premature stress.
Dismountable bead ring designs allow for fast part replacements, minimizing maintenance time. Crimped models provide airtight sealing, preventing leakage under pressure variations. The choice between galvanized steel and stainless steel AISI-304 affects corrosion resistance. Selecting the correct elastomer material prevents degradation due to chemical exposure or temperature changes. A comprehensive pre-installation inspection reduces unexpected failures, ensuring a longer lifespan for the air bellow system.
Operational Load Testing
To ensure an air bellow suspension meets operational requirements, load testing must be conducted. Controlled inflation tests verify expansion consistency and load distribution uniformity.
- Monitor air pressure fluctuations under incremental loads.
- Identify air leaks using a soap solution around valves and connections.
- Measure rubber elasticity under maximum working conditions.
Single convolution air bellows have stroke lengths between 36 mm and 283 mm, depending on size. Double convolution models extend up to 470 mm, providing greater flexibility. The diameter range varies between 80 mm and 950 mm, supporting various industrial applications. Properly fitted blind nuts with BSP air inlets ensure tight connections, minimizing air loss. Performing load tests guarantees operational stability, preventing unexpected mechanical failures and optimizing system efficiency in demanding conditions.
Environmental Resilience Testing
External conditions like temperature shifts, chemical exposure, and humidity levels affect air bellow longevity. Simulating operating environments during testing phases helps identify vulnerabilities.
- Thermal endurance tests verify temperature stability in extreme climates.
- Corrosion resistance evaluations determine if metallic parts can withstand moisture.
- UV exposure analysis prevents rubber deterioration from prolonged sunlight contact.
Rubber bellows function between -40°C to +115°C, depending on elastomer formulation. Chlorobutyl provides acid resistance, while Nitrile resists oil and fuel exposure. Bead ring sealing efficiency affects pressure retention, influencing long-term durability. Stainless steel AISI-316L enhances protection against chemical agents. Conducting isolation efficiency tests ensures performance consistency across varying environmental conditions. Monitoring these factors allows air bellows to maintain functionality and safety in industrial applications.
Routine Performance Evaluations
Regular inspection schedules prevent downtime and sustain operational efficiency. Implementing a structured maintenance strategy reduces unexpected breakdown risks.
- Check compression and expansion ratios under various loads.
- Analyze wear patterns in rubber components.
- Evaluate material elasticity to detect fatigue symptoms.
Top-tier air bellows maintain natural frequency values between 1.21 Hz and 4.6 Hz at 6 bar pressure. Consistently tracking operating height prevents load imbalances in precision systems. Utilizing height control technology stabilizes air suspensions under variable weight conditions. Conducting preventative fatigue testing safeguards rubber integrity, improving long-term performance. Evaluating maintenance records helps predict potential failures, ensuring continuous reliability and system longevity.
Emergency Response Planning
Even with detailed safety inspections, unforeseen failures may occur. Establishing an emergency response framework minimizes operational disruptions and damage risks.
- Keep spare components for immediate replacements.
- Train teams in rapid fault detection techniques.
- Develop detailed inspection logs to identify recurring issues.
Emergency pressure-release valves prevent sudden collapses caused by overload stress. Fail-safe mounting structures guarantee secure installation under high-vibration conditions. Advanced failure analysis tools detect weak points before critical breakdowns. Ensuring mounting plate compatibility prevents seal malfunctions linked to misalignments. Following these protocols allows industrial air bellows to function safely and reliably under demanding circumstances.
Conducting safety inspections for air bellow suspensions is crucial for performance enhancement, failure prevention, and prolonging service life. By applying pre-installation checks, load verification, environmental durability testing, routine assessments, and emergency strategies, companies ensure consistent functionality.
Key factors include material quality, pressure cycle tracking, and temperature resistance analysis. Routine vibration isolation tests maintain load stability. Continuous pressure monitoring maximizes system performance. Implementing quality control benchmarks ensures uniform product reliability across industrial applications.