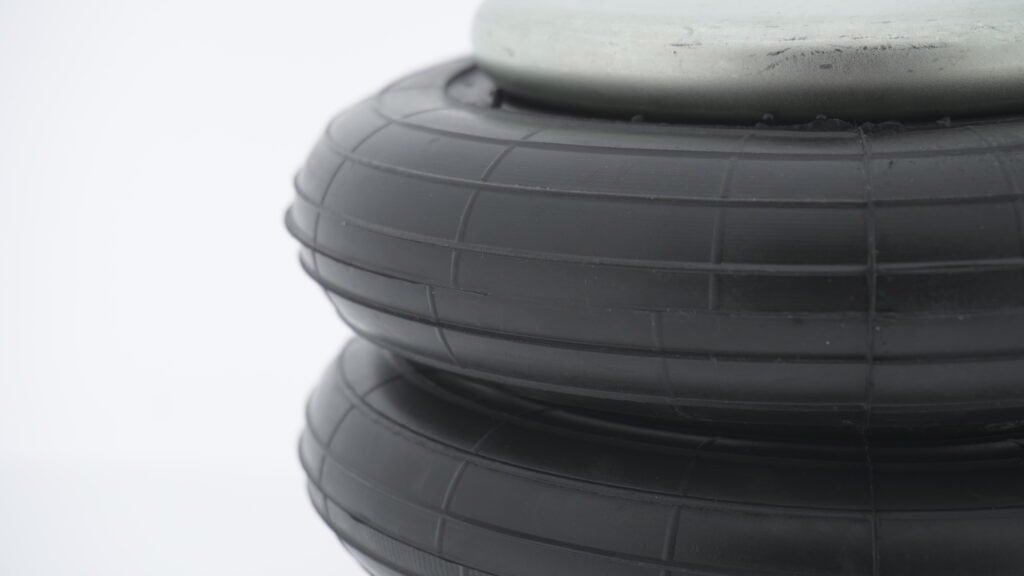
When it comes to air bellows, durability testing is crucial for ensuring their reliability and longevity in demanding applications. Our focus is on advanced testing techniques for air bellow durability that push the boundaries of standard evaluations. We aim to ensure performance under a variety of real-world conditions. In this article, we explore different testing methodologies, why they are vital, and how they can be optimized for better performance and longer service life.
The Importance of Rigorous Testing
Testing air bellows is more than just a quality check. It is a comprehensive analysis that ensures these critical components can withstand extreme pressures, vibrations, and environmental conditions. By implementing advanced testing techniques, we guarantee that air bellows meet stringent industry requirements. These tests include both static and dynamic tests, each aimed at identifying weaknesses that could emerge during the lifespan of an air bellow.
We utilize a combination of fatigue testing, pressure cycling, and thermal analysis to identify potential points of failure. Fatigue testing involves subjecting the air bellow to repetitive stresses to simulate years of use in a controlled timeframe. The aim is to predict the product’s fatigue life and ensure it can tolerate prolonged use without degradation. This approach helps us identify and mitigate risks, enhancing product reliability and safety.
Dynamic Fatigue Testing
Dynamic fatigue testing is one of the primary methods used to evaluate air bellow durability. By continuously cycling the air bellow under variable loads, we determine its capacity to withstand repetitive movements without breaking down. This test mimics the operational conditions that air bellows experience, including the impact of load variations and pressure fluctuations.
Dynamic testing reveals weaknesses in material composition and helps us improve manufacturing processes. Weak points identified during these tests are valuable for refining the design and enhancing the structural integrity of the product. By addressing these vulnerabilities, we ensure that the final product is robust and capable of performing well in a wide range of applications.
Pressure Cycling and Burst Testing
Pressure cycling tests are another cornerstone of air bellow evaluation. These tests involve exposing the air bellow to fluctuating pressure levels to determine its resistance to pressure fatigue. Pressure cycling assesses the resilience of air bellows to extreme conditions, simulating the changes in pressure they experience during use.
In addition, burst testing is conducted to establish the maximum pressure threshold an air bellow can tolerate before rupturing. This is essential for understanding the safety margins and for setting operational pressure limits. Burst testing ensures that our products operate safely even under unforeseen pressure spikes. This information is crucial for designing systems that withstand unexpected events, safeguarding equipment and personnel.
Environmental Testing Techniques
Air bellows must also withstand a wide range of environmental factors. We conduct environmental testing that includes exposure to extreme temperatures, humidity, and corrosive substances. Thermal cycling tests the air bellow’s ability to endure rapid temperature changes, which can affect the flexibility and elasticity of the bellow material.
Humidity testing focuses on the resilience of air bellows in moist or corrosive environments. Such tests are crucial for applications in harsh climates or industries where exposure to chemicals is common. By ensuring our products can withstand these challenges, we help our clients maintain system reliability even under adverse conditions.
Vibration and Shock Testing
Vibration testing evaluates how air bellows handle continuous vibration, a common factor in automotive and industrial applications. By simulating realistic vibration patterns, we ensure the air bellow’s integrity remains intact, even under prolonged exposure to shaking forces.
In addition to vibration testing, shock testing determines how air bellows respond to sudden impacts or load changes. This is especially important for applications in transportation, where air bellows may be exposed to road shocks or sudden load transfers. The results of these tests allow us to design air bellows that effectively absorb shocks, reducing the risk of mechanical failure in dynamic environments.
Material Analysis and Non-Destructive Testing
Advanced durability assessment also involves material analysis. We use non-destructive testing (NDT) techniques such as ultrasonic testing and X-ray inspection to identify any internal flaws in the air bellow material that might not be visible to the naked eye. These tests help detect cracks, voids, or material inconsistencies without damaging the product.
Tensile testing is another critical method, providing insight into the material’s strength and its ability to elongate under stress. By combining material analysis with other durability assessments, we provide a holistic evaluation of the air bellow’s performance. This approach ensures that all aspects of the material’s properties are understood and accounted for in the final product design.
Enhancing Air Bellow Longevity through Data Analytics
One of the newest approaches in durability testing is the use of data analytics. By integrating sensors during testing, we gather real-time data on stress distribution, temperature changes, and pressure levels. This data is then analyzed using advanced algorithms to predict potential failure points and recommend improvements in design and material selection.
Predictive maintenance, based on the data collected during these tests, allows us to offer customers insights into when their air bellows may need replacing or servicing. This proactive approach helps in reducing downtime and maintaining system efficiency. By leveraging data-driven insights, we can continuously refine our products, ensuring they meet evolving performance demands.
Advanced testing techniques for air bellow durability are essential for ensuring these components meet the rigorous demands of industrial and automotive applications. By employing a combination of dynamic fatigue testing, pressure cycling, environmental testing, and material analysis, we guarantee the longevity and reliability of our air bellows. Incorporating data analytics into our testing regime also enhances predictive maintenance, ensuring our customers receive the best possible performance from our products.
Our commitment to rigorous testing helps us deliver air bellows that meet and exceed industry standards, providing our clients with safe, reliable, and durable solutions.