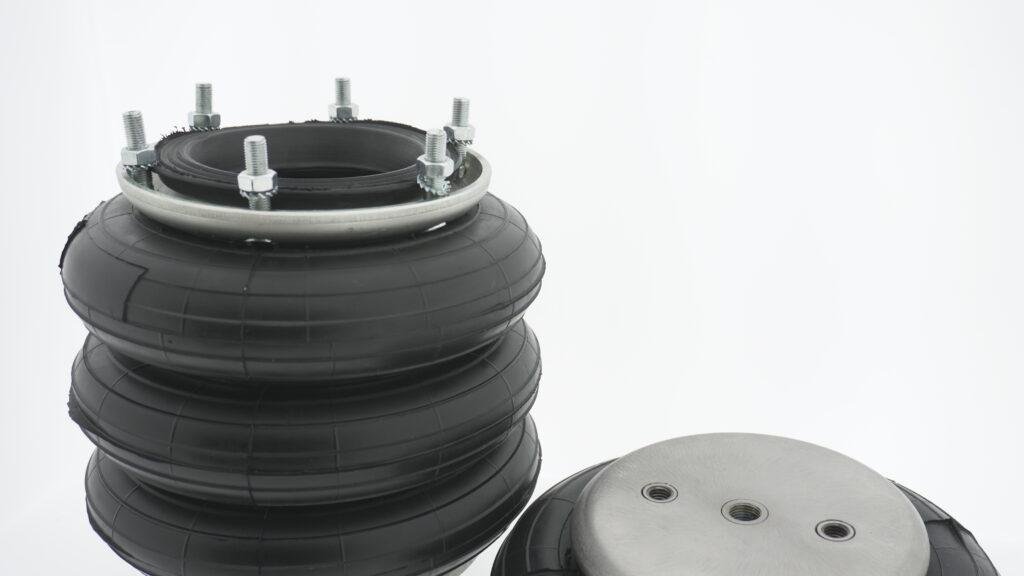
Ensuring consistent performance through certified air spring quality
In today’s industrial landscape, compliance with certified air spring standards guarantees safety, reliability, and longevity. At Tevema, we validate product performance through recognized certification procedures across varied operating environments. Every air bellow is tested using precise quality criteria. Our designs maintain tight tolerances on wall thickness, ply count, and convolution shape to ensure consistent mechanical response. Standard models handle 8 bar pressure, while our four-ply configurations manage 12 bar. We subject bellows to cyclic tests measuring compression, elongation, and torsion. Each component is certified for geometric stability and dynamic force control. ISO frameworks guide our production, ensuring global conformity and replicability across batches. Certified components boost system compatibility and safety margins. Clients count on us for bellows that perform reliably under constant mechanical stress. Our certified approach eliminates premature failures. Through this certification-driven strategy, we provide air springs capable of enduring demanding operational loads with minimal maintenance.
Why certification matters in industrial environments
Industrial equipment faces frequent vibration, temperature fluctuation, and pressure shifts. These conditions demand air bellows with validated resistance to fatigue and material degradation. At Tevema, certification ensures our products meet the industry’s most demanding durability standards. We test under accelerated lifecycle scenarios, confirming performance beyond 100,000 cycles. These tests replicate pressure surges, torsional loads, and elongation events. Our materials pass aging, flexural, and fatigue evaluations. We apply reinforcement strategies that maintain convolution alignment and wall elasticity. Certified bellows help prevent deformation and cracking. We simulate field loads during testing to ensure function under real operational conditions. These simulations include lateral misalignment and stroke variability. Results are recorded digitally and verified against international quality metrics. Compliance with certification guarantees predictability under high-duty applications. For industries where downtime is critical, certified air springs offer peace of mind. They minimize risk while extending equipment life. Certification isn’t just assurance—it’s an operational necessity across precision-driven sectors.
Key standards applicable to air spring manufacturing
Our manufacturing processes follow stringent certification systems, especially ISO 9001 for overall quality control. This standard ensures traceability, design discipline, and repeatable production quality. We implement material testing protocols like ISO 37, ISO 815, and ISO 34-1. These standards measure tensile strength, compression resistance, and tear properties of our elastomers. We also comply with ISO 7751 for pressure cycling and ISO 188 for aging performance. Laser scanners assess convoluted profile geometry, ensuring deformation remains within tolerances. Vulcanization data, pressure response curves, and material stress-strain reports are logged per ISO protocols. Internal quality control frameworks align with ISO rules to manage design validation. Product dimensions are measured with calibrated gauges and digital templates. Statistical process controls identify any variation across production. These systems certify that our bellows maintain mechanical properties over time. With each production run, compliance is rechecked. Standards aren’t optional—they’re embedded into our engineering philosophy. Certification confirms performance under controlled conditions.
Material and media certifications for diverse applications
Our air bellows are constructed using certified rubber compounds suited to specific media and temperature conditions. Chlorobutyl rubber resists acids and is validated up to 115 °C. EPDM withstands high temperatures and ozone exposure and is certified using ASTM D1171 standards. Nitrile rubber is ideal for fuel and oil-rich environments, tested under ASTM D2000 for chemical compatibility. Metal parts are made from AISI-304 or AISI-316L stainless steel to ensure corrosion resistance. These components pass EN 10088-1 corrosion standards and salt spray testing up to 500 hours. Each material batch includes certification data on composition, elasticity, and media compatibility. This ensures proper selection for every project. Clients receive supporting documentation confirming compliance with international material safety standards. These include REACH and RoHS declarations. Our bellows work reliably in moisture, oil vapor, and nitrogen-filled environments. Material certification protects long-term function and simplifies technical approvals. Proper material selection, backed by testing, reduces system failure risk.
Pressure validation and certification methodology
Every Tevema air bellow is tested under static and dynamic loads to certify pressure integrity. Our standard units withstand 8 bar, while our four-ply designs operate up to 12 bar. To validate burst strength, we test at 1.5 times the rated pressure using ISO 19879. Load tests measure behavior under prolonged compression. Sensors track dimensional changes in real-time under incremental pressures. Strain gauges confirm uniform material stress across convolutions. High-pressure cycle tests ensure structural stability under continuous use. Pressure retention and rebound response are documented for each tested configuration. Certification verifies that products maintain sealing and performance without material cracks or deformations. We simulate surge pressure and emergency loads during qualification. Certified test protocols are reviewed by external auditors annually. These reports support safety documentation during procurement. Certification ensures our bellows deliver stable behavior under high mechanical and pneumatic demands. It eliminates guesswork in pressure-critical operations and improves equipment uptime reliability across industrial sites.
Traceability and batch control standards
Traceability is key to ensuring quality and accountability in every Tevema air spring. Each product receives a batch code tied to its production data. We log materials, curing profiles, and test results using our ERP system. ISO 17359 standards guide our traceability protocols. Raw material lot numbers, curing times, and molding parameters are digitally recorded. Should issues arise, complete batch histories are retrievable within seconds. For regulated industries, we provide certificates including material compliance, dimensional reports, and quality audits. Our ERP system matches products to specifications, avoiding undocumented variation. Traceability supports root-cause investigations and maintenance planning. It ensures design conformity throughout the product’s lifecycle. Documentation is exportable for client audits or compliance inspections. Predictive maintenance programs also benefit from traceable data. This approach increases transparency and fosters trust. When accountability matters, our certified traceability delivers. Batch control enables performance tracking, warranty support, and engineering review across every operational cycle.
Certification for durability in vibration isolation
Industrial machinery requires stable vibration isolation. Our bellows are certified under ISO 10846 and DIN 45673 vibration performance standards. Each unit undergoes frequency testing from 1 Hz to 30 Hz under live load. Results confirm 99% vibration reduction across the operating range. Low natural frequencies are key indicators of isolation efficiency. Bellows are tested under multi-directional displacement and lateral force. We measure rebound behavior, compression consistency, and long-term flexibility. Repeated testing ensures resilience against vibration fatigue. Angular misalignment tolerance is verified for up to 25 degrees, per application type. Certification confirms stable performance across thousands of vibration cycles. Isolators are tested under combined pressure and movement to ensure functional consistency. Systems using our bellows benefit from fewer resonance issues and prolonged machine life. Reduced vibration enhances product longevity. Certified isolation capabilities ensure stable operation in equipment exposed to constant mechanical stress. These standards confirm durability under high-frequency vibration and irregular load patterns.
Environmental resistance and storage certification
Rubber degradation occurs over time if improperly stored. Tevema adheres to ISO 2230 for air spring storage protocols. Bellows are shielded from UV, ozone, and high humidity during warehousing. Packaging includes moisture barriers and opaque wrapping. Rubber properties are checked after extended storage to ensure elasticity and hardness. Shelf-life is tracked based on environmental conditions and batch production. We retest older inventory before shipment when needed. REACH and RoHS compliance ensures rubber formulations are free from hazardous substances. Elastomers, adhesives, and paints meet substance safety requirements. Environmental compliance documentation is provided upon request. Certified storage preserves product performance until installation. In long project cycles, storage control is essential. Clients in regulated sectors depend on reliable mechanical properties post-storage. Proper warehousing preserves functionality. Certification ensures products retain operational quality during delayed deployment. These measures prevent startup failures. Certified air springs stay mechanically reliable even after extended storage in challenging industrial supply environments.
Cleanroom and hygienic compliance
Tevema air springs meet cleanroom and hygienic standards where contamination must be controlled. We certify products per ISO 14644-1 for particulate emission. Bellows are produced in controlled environments and tested for non-volatile residue and particle shedding. Smooth surfaces minimize microbial retention and enable easier cleaning. Components pass EN 1672-2 for hygienic design. Stainless steel elements meet AISI-316L corrosion and biocompatibility standards. Rubber is treated to resist biofilm formation. Cleanroom testing includes sterilization cycles and chemical resistance evaluations. Products are compatible with high-temperature cleaning and disinfectants. Washdown resistance confirms integrity after repeated sanitation. Clients in food and medical sectors benefit from our hygienic certifications. Compliance guarantees that materials will not degrade or leach under standard cleaning procedures. Certifications include data sheets verifying hygiene readiness. Design geometry supports drainability and easy inspection. These features ensure continued sanitary conditions. Cleanroom compliance confirms our bellows deliver stable performance without compromising cleanliness or safety.
Independent laboratory verification and certification audits
To ensure impartiality, Tevema air springs undergo third-party certification. External labs test pressure, fatigue, dimensional compliance, and chemical stability. Samples from every batch are randomly selected. These tests include high-pressure cycling, vibration exposure, and thermal aging. External inspectors follow ISO/IEC 17025 for audit methodology. We receive certified reports confirming compliance with all specifications. Results are stored in our database and are available to clients on request. Third-party audits build client trust and support procurement transparency. Dimensional stability, seal performance, and rubber-metal bond strength are all verified externally. Clients benefit from independent product validation. Certification audits are conducted annually, with interim spot checks. These assessments add credibility and highlight process consistency. Independent testing verifies engineering claims and strengthens supplier reliability. Our commitment to transparency is documented through these reports. External confirmation enhances internal accountability. It also simplifies integration into quality-controlled manufacturing systems requiring traceable third-party approval.
Continuous improvement through recertification
Recertification ensures Tevema products continue to meet evolving technical standards. We follow ISO 9004 and Six Sigma for quality enhancement. Product performance is reviewed annually using test data and field reports. Pressure endurance, vibration resistance, and geometric stability are reassessed. Updated standards are applied to new versions of existing models. Engineering improvements are documented and verified before release. Elastomer upgrades and steel refinements are introduced under strict control plans. All changes are revalidated through pressure and fatigue testing. Client feedback supports targeted improvement areas. Statistical process control monitors production consistency over time. Benchmarking against industry standards helps identify necessary updates. Recertification maintains client confidence and regulatory compliance. Future designs incorporate lessons from operational data and material science. Our innovation roadmap includes next-generation elastomers and sustainable materials. Quality is not static—it evolves. Periodic recertification ensures our certified air springs remain reliable, relevant, and compliant with the highest expectations.