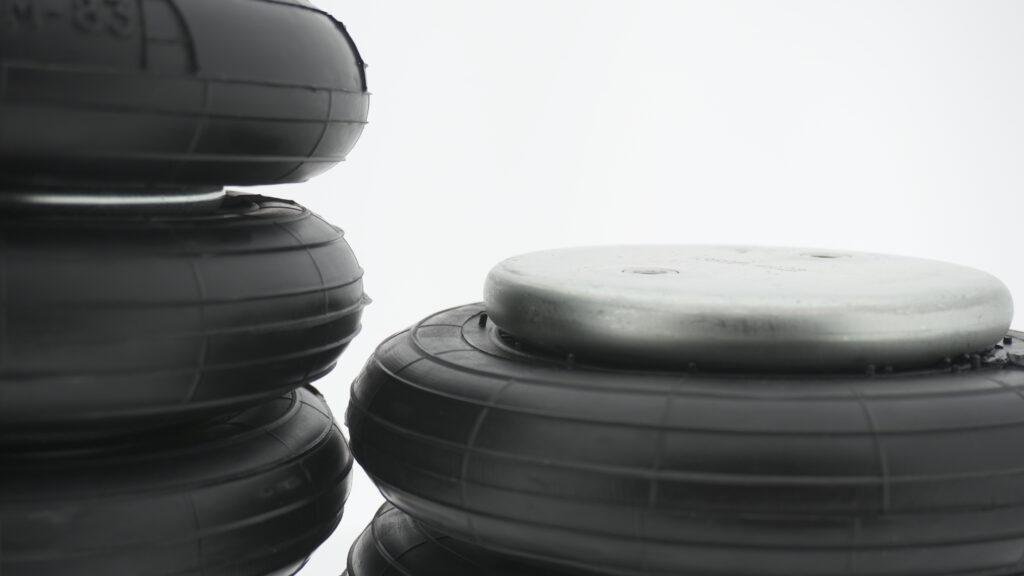
Tailoring air bellows to precise industrial needs requires an engineered approach combining material science, dimensional analysis, and system design. We always begin by evaluating the load, media type, mounting restrictions, and stroke requirements. Each project demands a unique solution that balances compact installation with long-term vibration control and dynamic performance. Selecting the right elastomer compound improves resistance to chemical exposure, ozone, oil, or water. We determine whether a single, double, or triple convolution format offers the correct stroke and stiffness balance. Each configuration alters the bellow’s response to pressure and lateral force. Mounting is another customisation area, with options like crimped, bead ring, and dismountable closures providing different benefits. Space availability and service intervals often guide this choice. We avoid overengineering by matching form to function with precision. All parameters—including pressure, load, angular movement, and misalignment—are modelled in advance. This ensures that each customised air bellow delivers reliability, performance, and low maintenance.
Selecting the right elastomer compound for durability and performance
The choice of elastomer directly affects the lifespan and safety of a customised air bellow. Different compounds behave differently under exposure to chemicals, ozone, and extreme temperatures. For general industrial settings, natural rubber (NR/SBR) combines cost-effectiveness with good dynamic flexibility. It operates reliably between -40 °C and +70 °C. If resistance to oil and grease is required, nitrile (NBR) is the preferred option, tolerating temperatures up to +110 °C. In chemical-rich environments, chlorobutyl (CIIR) delivers excellent acid resistance and low permeability. For outdoor exposure and high-temperature conditions, EPDM performs well up to +115 °C. Chloroprene (CR) serves as a hybrid solution, balancing weather resistance and moderate oil tolerance. Each of these elastomers is reinforced with high-strength textile layers for structural stability. Their performance is tested under cyclic pressure conditions. Selecting the proper compound avoids swelling, cracking, and fatigue. It also ensures compatibility with compressed air, nitrogen, or fluids containing oil, supporting operational consistency.
Determining convolution count for load and stroke flexibility
The number of convolutions in an air bellow defines how much stroke it can support and how much angular deflection it allows. Single convolutions are ideal where space is minimal and vertical motion is limited. These offer low natural frequencies and high stiffness. Double convolutions provide extended stroke and flexibility without compromising isolation effectiveness. They are preferred where more travel or damping is needed. Triple convolutions are used in advanced applications demanding long strokes or large angular tilt. Their added height allows better compensation for deflection. The convolution count also impacts the natural frequency range and overall lateral stability. For example, triple convolution bellows may reach stroke values over 300 mm and forces exceeding 70 kN. We calculate the load distribution, pressure input, and stroke limits before defining the convolution type. This step ensures the chosen bellow won’t overextend or collapse. Matching the right configuration guarantees reliability, mechanical safety, and consistent long-term motion control.
Matching closure design to installation and maintenance needs
Each closure type contributes to how easily a bellow can be installed, maintained, or integrated into a mechanical assembly. Crimped closures are compact, permanently sealed, and suitable for environments with limited space or infrequent access. Dismountable closures use clamping rings and separate plates, allowing for quick maintenance or part replacement. Bead ring closures provide robust, threaded or countersunk mounting options for high-precision integration. These are common where bellow replacement must be straightforward without disturbing the machine’s base structure. All closure types are available in configurations compatible with G1/4″, G3/8″, or G3/4″ air inlets. Their bolt circle diameters and port positions can be adjusted to fit the client’s layout. When corrosion or cleaning chemicals are present, closures can be manufactured in AISI-304 or AISI-316L stainless steel. We always verify mounting compatibility through dimensional checks. Choosing the right closure design ensures safe operation, serviceability, and long-term sealing performance, even under dynamic system pressures.
Adjusting pressure ratings to meet force requirements
Each customised air bellow must deliver the required actuation force at the available pressure without exceeding material limits. Standard bellows operate safely up to 8 bar, which covers most industrial use cases. In demanding setups, we use four-ply reinforced constructions rated up to 12 bar. These allow higher forces while keeping the installation compact. For example, a medium-sized bellow can reach 31 kN at 7 bar. We calculate the load per bellow, stroke range, and system air supply to set performance baselines. The media type—compressed air, oil-laden air, or nitrogen—also affects output characteristics. If water is used, all metallic parts must be corrosion resistant. We validate the entire system for burst pressure, fatigue cycles, and hysteresis effects. This guarantees reliable force generation over time. Correct pressure customisation ensures safety and function under static or dynamic loads. All configurations are tested to perform within specified stroke and pressure tolerances for industrial reliability.
Adapting port and thread configurations for system compatibility
Air bellows must integrate seamlessly with the customer’s mechanical layout and pneumatic system, requiring exact port and thread alignment. Standard port sizes include G1/4″, G3/8″, and G3/4″, with compatible internal threads for direct coupling. We offer several internal threading dimensions based on mounting and air connection requirements. In some cases, we use BSP, NPT, or custom thread types tailored to specific equipment. Matching these configurations avoids unnecessary adapters, which can cause leakage or instability. We align bolt circle diameters and port orientations to the client’s existing system. This simplifies installation and enhances performance. Adjustable drilling templates allow custom top and bottom plate geometry. For example, plates can be adapted for 6-, 8-, or 12-bolt patterns. Special air inlet locations can be chosen to ease hose routing. Customisation avoids misalignment, reduces installation time, and eliminates compatibility issues. Each unit is inspected for dimensional accuracy. Seamless system integration extends service life and reduces maintenance caused by poor assembly fit.
Selecting the right bellow height and diameter combination
Dimensioning the air bellow correctly is vital for balancing available space with the required performance. Bellows are available in diameters from 80 mm to 950 mm and heights from 45 mm up to 140 mm. A small-diameter bellow may support forces around 4 kN, while a larger unit can exceed 300 kN. We begin by defining minimum height, maximum extension, and required stroke. Applications with limited vertical clearance benefit from single convolutions, which offer compact design and short stroke. Double or triple convolution bellows are selected when more stroke or flexibility is necessary. For example, triple convolution bellows offer strokes over 300 mm. We calculate load per unit area to define diameter requirements. This ensures enough pressure coverage and stroke without exceeding travel limits. Matching height and diameter to the system helps prevent overextension or force loss. Our process ensures efficient movement, space-saving integration, and optimal pressure-to-load conversion for industrial setups.
Material upgrades for corrosion and chemical resistance
Material selection for metallic components significantly impacts the reliability of air bellows used in aggressive environments. Standard units use electro-galvanised steel, which performs well in dry, controlled spaces. In wet or chemical-rich settings, we offer stainless steel variants like AISI-304 and AISI-316L. These metals resist acids, detergents, and cleaning agents that degrade standard coatings. For weight-sensitive installations, aluminum end closures are also available. All materials are tested for tensile strength, corrosion resistance, and compatibility with the chosen elastomer. For instance, systems exposed to cleaning fluids require fully stainless closures and hardware. We also provide optional coatings or treatments on bolts and plates. Mounting holes, threads, and sealing faces are machined to strict tolerances. Every component is verified for mechanical fit and chemical durability. Using the right metal increases uptime, minimises unplanned service, and extends product lifespan. Material compatibility is essential in maintaining long-term mechanical and sealing performance under challenging conditions.
Optimising natural frequency for vibration control systems
Vibration isolation depends heavily on tuning the natural frequency of the bellow to avoid resonance with machine movement. For effective isolation, this frequency must be below 3 Hz. We achieve this by adjusting air volume, convolution count, and mounting stiffness. Lower natural frequencies result in better absorption of unwanted motion. This is critical in precision machinery where vibration affects accuracy. Larger bellows with longer strokes typically yield better isolation. For example, a triple convolution bellow with 410 mm diameter may achieve a natural frequency near 1.6 Hz. We conduct dynamic simulations to identify ideal pressure, height, and load settings. We also validate performance using frequency response curves. Maintaining a stable natural frequency under changing loads ensures predictable performance. Proper tuning prevents energy buildup and mechanical resonance. The final design is tested under operational conditions to confirm isolation effectiveness. This approach extends component life, improves safety, and protects delicate systems from harmful vibration exposure.
Custom bellow design for angular and lateral movement
Industrial systems often demand more than just vertical compression—air bellows must also tolerate angular and lateral movement. We design for angular deflection up to 25° and lateral displacement up to 30 mm. These capabilities prevent misalignment stress and reduce the need for expensive guides or pivots. Triple convolution designs are particularly effective at supporting tilt while carrying load. Fabric reinforcements inside the rubber allow multidirectional flexibility without sacrificing strength. For instance, a large bellow may provide 75 kN of load support while allowing 20 mm offset. We analyse the system’s movement envelope and determine necessary tolerances. Port positions can be adjusted to suit angle-specific installations. Asymmetrical convolution patterns or varied reinforcement angles improve side load stability. Material selection also plays a role in handling multi-axis force. Custom bellows reduce failure caused by unintended motion. We ensure consistent performance, structural safety, and stress relief even under dynamic lateral or angular movement.
Lifecycle and maintenance planning in design phase
We consider long-term use when customising every air bellow, factoring in service intervals, maintenance needs, and operational environment. For systems requiring easy maintenance, we recommend dismountable closures with quick-access clamping rings. In areas with limited access, crimped closures reduce parts and offer sealed longevity. We apply ISO 2230 storage standards to avoid rubber degradation before installation. Elastomers are selected for temperature range, UV resistance, and chemical stability. We test bonding strength and fatigue life using accelerated ageing procedures. Clients can choose features like standardised ports, guide points, or extended sealing surfaces. These options make servicing predictable and reduce time spent on replacements. Thread sizes and hole patterns are standardised across models where possible. This supports inventory management and simplifies staff training. Proper lifecycle planning reduces total cost of ownership and improves reliability. Each custom bellow becomes a robust, long-lasting solution designed not only for performance—but also for durability and convenience.