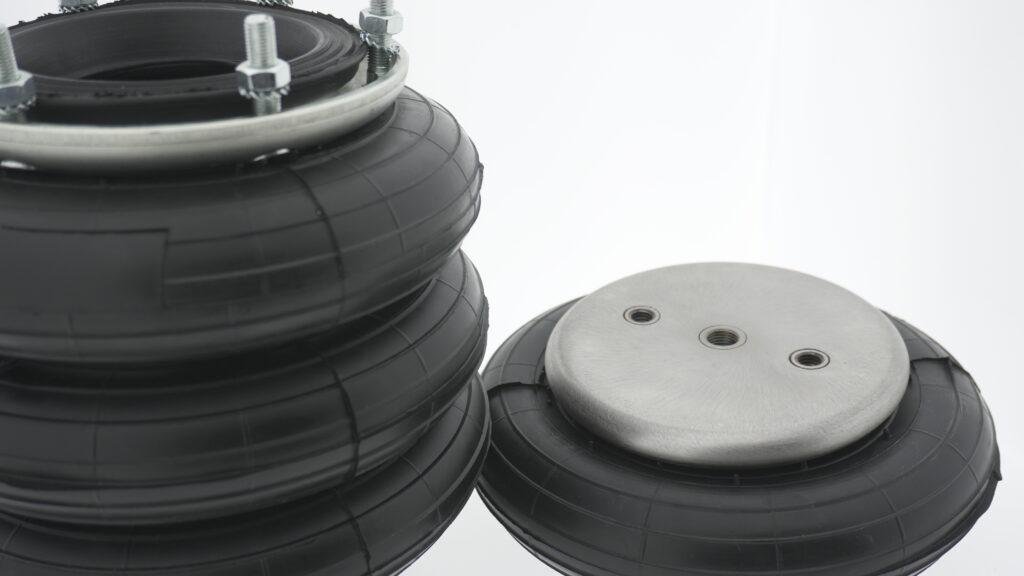
Calculating the natural frequency in air bellows is vital for designing effective vibration control systems. At Tevema, we ensure that our isolators function safely and predictably across varied industrial loads. Natural frequency is the point where the system’s own vibration matches external forces, possibly causing resonance. To avoid that, we select air bellows with the correct properties. Each Tevema air bellow includes a flexible multi-ply rubber structure with steel reinforcements. These design elements affect its response to load and pressure. For instance, double convolution models exhibit lower stiffness than single types. Our isolators feature consistent convolution geometry and standardized connection points. We typically operate within 50-80% of maximum stroke. This ensures our isolators stay within a target frequency range. By calculating the natural frequency in advance, we help our customers protect their equipment, reduce maintenance, and stabilize system behavior across a range of industrial conditions.
Why natural frequency matters in vibration isolation
The natural frequency in air bellows determines its effectiveness in blocking vibration at different operating frequencies. If the system’s excitation frequency matches the natural frequency, damaging resonance can occur. Our goal is to design systems that operate well below this threshold. Tevema air bellows are available in single, double, and triple convolution versions with varying load capacities and stiffness ranges. For example, a triple convolution unit can support up to 450 kN while maintaining a natural frequency below 2 Hz. The design height and effective area influence this behavior. Our technical team selects the right combination of pressure, geometry, and material to maintain system stability. In harsh environments, we use bellows made from EPDM or chlorobutyl compounds, which resist high temperatures and aggressive chemicals. These properties enhance the isolator’s resilience and ensure consistent performance. Keeping the natural frequency in check helps prevent long-term mechanical stress and excessive vibration transmission.
Basic formula for calculating natural frequency
To determine the natural frequency in air bellows, we use the standard formula: f = (1 / 2π) √(k / m). The variable f represents the frequency in hertz, k stands for stiffness in newtons per meter, and m is the supported mass in kilograms. At Tevema, we rely on exact technical data derived from our own measurements. We regularly test each unit for load response and deflection rate. For instance, a bellows with a dynamic stiffness of 9500 N/m supporting a 195 kg load results in approximately 3.5 Hz. This result guides our pressure adjustments and convolution selection. Higher stiffness increases frequency, which can reduce isolation performance. Therefore, our engineers recommend keeping frequencies between 1.2 Hz and 3 Hz for most applications. By maintaining consistent values, we avoid excessive vibration and system resonance. This method is foundational to our air spring design process and guarantees repeatable results in industrial setups.
Understanding stiffness in air bellows systems
Stiffness in air bellows systems varies with pressure, load, and the specific convolution type used. Tevema measures both static and dynamic stiffness during internal testing. Static stiffness refers to the load divided by deflection at equilibrium. Dynamic stiffness includes additional factors such as oscillation behavior and cycle frequency. A typical double convolution bellows operating at 6 bar might show dynamic stiffness around 10,000 N/m. The effective area, usually in cm², plays a key role. Tevema models offer consistent areas, with ranges from 60 to over 800 cm² depending on size. Larger areas reduce stiffness and increase isolation. Our bellows also use high-strength fabric plies, which increase durability and maintain consistent response across cycles. We recommend using pressure regulation systems to manage stiffness during operation. Load-deflection graphs from our test data assist engineers in predicting performance. Monitoring these parameters helps us achieve reliable vibration control and maintain a stable natural frequency under changing load conditions.
The role of air pressure and load height
Air pressure within a bellows directly influences both the stiffness and operating height. Tevema air bellows respond linearly to pressure increases, within tested tolerances. At 6 bar, a standard unit might reach 80% of its maximum stroke. Increasing pressure raises the design height and load capacity. This also affects natural frequency. For instance, a higher internal pressure can raise the stiffness and thus increase the frequency. Adjustments must balance performance and safety margins. Bellows designed for four-ply operation can support pressures up to 12 bar. This allows for higher loads while preserving isolation efficiency. We recommend using height-control valves and regulators to keep pressure within optimal bounds. Operating the bellows within 50% to 80% of their stroke ensures consistent mechanical behavior. Charts showing height vs. pressure and force vs. pressure help engineers select appropriate settings. Using these references allows us to fine-tune the natural frequency for improved reliability and vibration suppression.
Practical example with double convolution bellow
Consider a Tevema double convolution air bellow supporting a static load of 195 kg. The dynamic stiffness at 6 bar is approximately 9500 N/m. Applying the formula f = (1 / 2π) √(k / m) results in a natural frequency of about 3.5 Hz. This value slightly exceeds the ideal range for high-performance vibration isolation. We can reduce the pressure to lower stiffness and bring the frequency closer to 2 Hz. Tevema provides technical charts indicating pressure vs. stiffness curves. These assist engineers in determining the ideal pressure for their load and application. Additionally, our bellows maintain consistent surface area and stroke across pressure ranges, improving predictability. The axial stroke might be around 115 mm, with a design height of 160 mm. For better performance, we can also switch to a triple convolution model, reducing stiffness. Using these tools, we accurately control the natural frequency, enhancing system stability and reducing unwanted resonance effects.
Influence of convolution type on frequency
The convolution type significantly affects the air bellow’s mechanical response and frequency characteristics. Single convolution bellows offer compact designs and fast reaction times but have higher stiffness. Double convolution versions provide moderate stiffness with greater stroke lengths, making them suitable for general industrial vibration isolation. Triple convolution models exhibit the lowest stiffness and the best isolation performance. For example, a triple convolution bellow may reach a natural frequency as low as 1.4 Hz at 6 bar. Tevema ensures all bellows maintain uniform material thickness and consistent geometry. These factors contribute to stable performance across multiple cycles. The number of convolutions also affects angular flexibility, which can improve installation alignment. Engineers should evaluate both the supported load and target frequency when selecting a model. Our product charts detail convolution effects on stiffness and frequency. Matching the right configuration helps us achieve optimal isolation without compromising system height or stroke. It ensures long-term system integrity and protection.
How to identify isolator resonance
Detecting resonance in an isolation system is critical for long-term performance. Symptoms include excessive vibration, irregular equipment movement, or premature seal degradation. At Tevema, we advise performing system audits when such signs appear. We start by comparing the excitation frequency of the environment to the calculated natural frequency of the installed bellow. If the values align, resonance is likely the cause. Solutions include adjusting the internal air pressure to change stiffness or switching to a different convolution type. In some cases, increasing the supported mass can also shift the system away from resonance. Our engineers use digital accelerometers to record vibration amplitudes. This data guides the tuning process. We often recommend testing under simulated operational loads to better capture system behavior. Preventing resonance protects machinery and reduces maintenance downtime. By maintaining a safe gap between excitation and natural frequency, we help customers improve system reliability and prevent costly mechanical failures over time.
Tools for dynamic frequency tuning
Dynamic frequency tuning is essential when installing air bellows in variable environments. Tevema uses multiple tools to support this process. First, we apply digital pressure regulators to manage internal pressure levels precisely. This lets us adjust stiffness in real time. Second, we use test benches with calibrated masses to simulate field conditions. These simulations reveal actual load distribution and response. Third, we install high-sensitivity accelerometers to measure vibration frequency and amplitude directly from the system. With these tools, we detect small shifts in dynamic behavior. Engineers can then recalibrate the bellows by changing pressure or selecting alternate models. This avoids costly overdesign or underperformance. Our four-ply bellows allow greater tuning range due to increased strength and lower stiffness variability. Using these methods, we fine-tune the natural frequency during commissioning. This ensures each system meets the required isolation performance and remains adaptable to changes in load or vibration profile without physical modifications.
Material selection and its frequency impact
The choice of elastomer in an air bellow directly affects its dynamic properties and natural frequency. At Tevema, we offer multiple compound options for different operating environments. Natural rubber provides good all-round performance with excellent elasticity. Nitrile rubber is ideal for oil-rich or chemically aggressive settings due to its resistance to solvents. EPDM offers exceptional resistance to ozone and high temperatures, suitable for outdoor or hot environments. Each material affects stiffness differently. For instance, nitrile compounds are stiffer, potentially increasing the system’s natural frequency. In contrast, EPDM or chlorobutyl lowers resonance peaks due to higher damping. Our engineers select the right material based on environmental conditions, expected load, and target vibration range. We also provide metallic end closures in galvanized or stainless steel, which affect mass and resonance. The material compatibility ensures long-term durability and consistent isolation performance. Careful selection and combination of these materials enable precise control over vibration behavior and isolator reliability.
Measuring real-world natural frequency
Real-world verification of the natural frequency in air bellows is essential for final validation. Tevema employs several practical methods. One is the bump test, where we apply a short impact and measure the system’s oscillation using accelerometers. The decay rate and frequency of oscillation reveal the actual system resonance. Another method uses frequency sweep tests, where we expose the isolator to controlled harmonic vibrations and monitor system response. These measurements help confirm that theoretical calculations match installed behavior. We also employ FFT analyzers to capture spectral data and detect unexpected frequency peaks. Field measurements often reveal slight deviations from lab values due to installation variables. Tevema recommends verifying key parameters such as internal pressure, stroke, and load prior to testing. Documenting this data creates a baseline for future comparisons. It ensures the isolator performs within safe vibration limits and provides the expected protection across all operational cycles.
Final checks before system activation
Before activating an isolation system, we complete a series of checks to confirm that all parameters align with design targets. Tevema engineers inspect the installation for alignment issues, air line connections, and plate mounting integrity. We verify that the internal pressure is within the specified range using calibrated gauges. Next, we confirm the supported load matches the intended specification. These steps ensure the air bellow isolator operates at the expected natural frequency. We also conduct a simulated load test, using a known mass to verify stroke and deflection. The system response is recorded and analyzed. Any deviations from predicted behavior are corrected through adjustments to air pressure or alignment. Tevema maintains documentation for each test scenario. This reference assists future maintenance or audits. By finalizing these checks, we ensure long-term reliability, effective vibration isolation, and protection of surrounding equipment. Proper commissioning is essential to meet isolation goals and maintain frequency consistency in dynamic conditions.