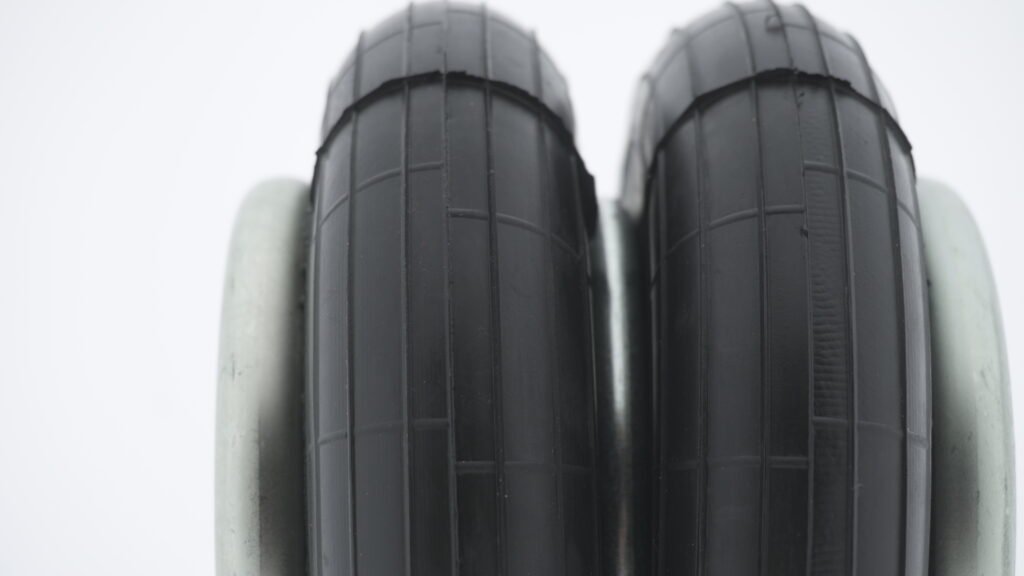
In industrial applications, ensuring the longevity and efficiency of air bellows is crucial for minimizing downtime and optimizing performance. Implementing sensor-based monitoring allows for real-time diagnostics, ensuring that potential failures are detected before they lead to system breakdowns. Advanced monitoring systems prevent costly malfunctions. By integrating sensors, engineers can track performance and intervene before issues arise. The combination of predictive analytics, IoT connectivity, and automation significantly enhances operational efficiency. Real-time diagnostics ensures continuous uptime, reducing unexpected breakdowns. Operators rely on accurate data to maintain optimal functionality. Sensor integration helps companies achieve cost-effective maintenance strategies. In this article, we explore the significance of sensors in monitoring air bellows health, detailing their types, functions, and benefits. Understanding these monitoring tools is crucial for industries relying on air bellows.
Why Monitoring Air Bellows is Essential
Preventing System Failures
Air bellows are integral to numerous industrial and automotive applications, providing shock absorption, vibration isolation, and load leveling. Over time, air leakage, material fatigue, and pressure inconsistencies can compromise their functionality. Sensors play a pivotal role in detecting early warning signs, preventing costly breakdowns. Continuous monitoring identifies minor issues before they escalate. Small leaks, excessive wear, or imbalanced loads can degrade performance. Operators can address concerns proactively, avoiding downtime. Sensor-equipped systems provide instant feedback, allowing rapid response to performance deviations. By maintaining optimal function, industries reduce operational risks. Monitoring also contributes to safety, ensuring compliance with strict industry regulations. Sensors help in extending air bellow lifespan, improving return on investment. Preventative maintenance minimizes repair costs. Advanced detection systems lower repair frequency, increasing productivity. Proper diagnostics enhance overall machinery reliability, ensuring consistent output. Real-time monitoring solutions significantly reduce inefficiencies.
Enhancing Performance & Efficiency
By continuously monitoring air bellows, operators can optimize air pressure, ensuring consistent load distribution and reducing wear and tear. Proper monitoring minimizes energy consumption, resulting in lower operating costs and extended service life. Smart monitoring solutions adjust air pressure in real time. Load sensors ensure even force distribution, reducing stress. Preventative action stops excessive strain, ensuring longevity. Optimized performance improves fuel efficiency in transportation applications. In industrial settings, regulated air distribution improves machinery lifespan. Data-driven analysis enhances process efficiency, ensuring cost-effective solutions. Predictive analytics forecast potential failures before they occur. High-precision sensors detect minimal variations in pressure or load, allowing instant corrections. Automated systems reduce human intervention, minimizing labor costs. Cloud-based analysis tracks system status remotely, offering seamless oversight. Advanced monitoring solutions support sustainable operations, reducing waste. Smart algorithms optimize pressure regulation, enhancing overall effectiveness. Efficiency gains translate to long-term cost savings. Automated adjustments maintain stability, eliminating performance inconsistencies.
Key Sensor Types Used in Air Bellows Monitoring
1. Pressure Sensors
Pressure sensors measure internal air pressure, ensuring that bellows maintain the required inflation levels. A drop in pressure may indicate a leak or structural damage, while excessive pressure could lead to premature failure. Operators rely on accurate pressure readings to maintain function. Sudden changes in pressure indicate faults requiring immediate intervention. Automated pressure adjustments improve safety and efficiency. Dynamic response systems stabilize pressure in demanding conditions.
- Typical operating pressure: 4 to 8 bar
- High-strength versions: Up to 12 bar
- Response time: <5ms for dynamic adjustments
- Accuracy: ±0.25% full-scale reading
- Calibration frequency: Annual or semi-annual as per industry standards
2. Temperature Sensors
Excessive heat can degrade rubber compounds used in air bellows, leading to material fatigue. Temperature sensors help detect thermal anomalies, ensuring optimal operating conditions. Maintaining stable temperatures preserves rubber elasticity. Overheating can indicate excessive mechanical stress or friction. Temperature sensors provide early warnings, allowing immediate intervention. Remote monitoring systems ensure continuous oversight.
- Typical operating temperature: -40°C to +115°C
- Resistance to environmental factors: High-grade elastomers
- Thermal response rate: Instantaneous for rapid detection
- Compatibility: Works with IoT platforms for cloud-based analysis
3. Vibration Sensors
Monitoring vibration levels provides insights into structural integrity. Increased vibration amplitudes may indicate misalignment, loose fittings, or internal damage. Vibration sensors help maintain system stability and performance. Unusual vibrations suggest potential component failure. Consistent monitoring ensures early detection. Stable systems last longer with reduced stress on materials. Vibration analysis enhances predictive maintenance strategies.
- Measurement accuracy: 0.01g resolution
- Frequency range: 1Hz to 5kHz
- Durability: Shock-resistant, industrial-grade housing
- Data logging capability: Long-term trend analysis for preventive maintenance
4. Load Sensors
Load sensors measure force distribution, ensuring uniform weight distribution across air bellows. Any imbalance could result in uneven wear, potentially leading to mechanical failures. Load distribution affects bellow integrity and system efficiency. Automated load balancing optimizes functionality.
- Load capacity: Up to 450kN per bellow
- Measurement accuracy: ±1% full scale
- Integration: Compatible with automation systems
- Signal processing: Real-time digital analysis
5. Leak Detection Sensors
Air leaks significantly reduce system efficiency. Leak detection sensors use ultrasonic or acoustic technology to identify small leaks before they escalate into major failures.
- Sensitivity: Detects leaks as small as 0.1mm
- Operating frequency: 20 kHz to 100 kHz
- Alert response: Instantaneous detection system
- Maintenance benefits: Reduces unplanned downtime
Sensors play a critical role in ensuring the reliability, efficiency, and safety of air bellows. By leveraging real-time monitoring, predictive analytics, and IoT connectivity, businesses can achieve cost savings, extended service life, and enhanced performance. Advanced sensor technology detects failures before they become critical. Automated alerts provide proactive responses. Sensor-based systems ensure stable air bellow operations in industrial and automotive sectors. Technology continues to evolve, making air bellow monitoring more efficient. Future advancements will drive even greater levels of automation, ensuring unparalleled efficiency in air bellow applications. Companies that adopt sensor-driven maintenance strategies experience long-term operational benefits.