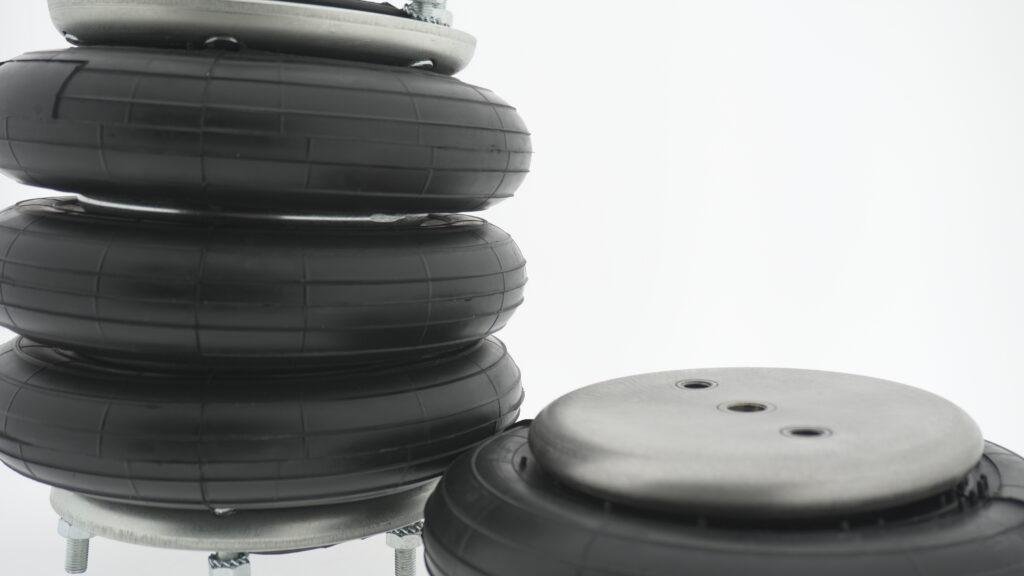
Enhancing precision through mechanical stability
Automated precision cutting tools require absolute mechanical stability to achieve repeatable and accurate results. Even minor vibrations or inconsistencies in machine behavior can compromise final tolerances. In our engineering processes, we integrate air bellows specifically for their ability to provide consistent vibration isolation, smooth height compensation, and enhanced stability. Unlike rigid components, air bellows adapt dynamically to shifting conditions, absorbing motion and minimizing transmission of unwanted forces. This adaptability improves performance, reduces equipment fatigue, and increases precision during continuous operation. Each air bellow model is selected based on calculated parameters such as maximum stroke, load capacity, and natural frequency. For instance, a double-convolution design can offer isolation at frequencies as low as 1.5 Hz, depending on pressure. Internal pressures range up to 12 bar using four-ply construction. Typical stroke lengths vary from 20 mm to 375 mm, with corresponding deflection control. Port positions are centered and sealed to handle dynamic load cycles.
Structural advantages of bellow design
The secret lies in the unique structure of air bellows. Each unit consists of a flexible rubber-metal composite formed into convolutions, enabling them to flex in multiple directions without losing form. Internally pressurized, the bellows counteract axial disturbances with precise resistance. We select configurations based on the tool’s size, load, and isolation requirements, choosing from single, double, or triple convolution models. These versions vary in stroke length, load-bearing capacity, and natural frequency. For example, a triple convolution bellow can accommodate strokes up to 375 mm and deliver forces over 75 kN at 7 bar. Frequencies stay low, around 2.0 Hz, enabling optimal vibration dampening. This combination of flexibility and strength ensures the bellow behaves as both an effective isolator and a compact actuator. Design height can range from 50 mm to 140 mm, depending on design. Inlet types include BSP and NPT threading for integration with common compressed air systems.
Environmental durability and consistent output
By incorporating air bellows, we prevent unstable tool paths caused by micro-vibrations. They absorb the mechanical energy before it reaches the cutting edge. This reduces chatter, ensures smoother finishes, and prolongs tool life. Additionally, our use of high-strength elastomers provides durability in demanding production environments, resisting oil, ozone, and temperature shifts. With pressure ratings up to 12 bar in four-ply configurations, they support heavier assemblies without sacrificing flexibility. Elastomers such as NBR, EPDM, and CIIR allow for compatibility with oil-contaminated air and exposure to industrial chemicals. Temperature ranges from -40 °C to +115 °C, depending on the compound. Most models are equipped with G1/4 to G3/4 air inlets, and installation bolts range from M6 to M10, offering easy mounting in various industrial platforms. Average internal diameters vary from 80 mm to 950 mm, ensuring accurate selection based on deflection requirements. Technical tolerances remain within ±1.5 mm under standard loading conditions.
Load distribution and response accuracy
In high-precision environments, uneven load distribution can distort movement and compromise the cutting process. Air bellows ensure uniform load balancing, particularly in multi-point setups supporting a machine table. Thanks to their design, they react instantaneously to vertical displacement, adjusting internal pressure in response to shifting weight. This responsiveness allows seamless alignment correction without halting the operation. Depending on configuration, load capacities range from 0.5 kN up to 450 kN, supporting both delicate tools and massive assemblies. For instance, a two-convolution steel design with 310 mm diameter can handle over 240 kN with minimal deflection. The natural frequency, typically under 2.5 Hz, minimizes vibration interference even under fluctuating loads. We prioritize using symmetrical mounting brackets and evenly distributed bead-ring assemblies to preserve alignment. Where relevant, centering collars with 0.2 mm concentricity tolerance are used. Combined with reinforced bushings, this allows for optimal motion transfer, high stiffness control, and consistent cutting performance.
Maintenance-free operation and lifecycle efficiency
A key benefit of integrating air bellows in cutting systems is their maintenance-free operation. Unlike hydraulic or mechanical actuators, air bellows have no sliding seals or pistons. The flexible body absorbs motion without internal friction, eliminating lubrication and reducing wear. This simplicity extends the service life and cuts downtime. On average, high-quality models endure tens of millions of cycles without performance loss. We prefer bellows made with electro-galvanized or AISI 304 stainless steel end plates, offering corrosion resistance in damp or chemically exposed conditions. For applications needing higher fatigue resistance, four-ply designs outperform standard two-ply systems by withstanding higher pressure and stress. Their superior rebound characteristics reduce rebound oscillation, keeping cutting heads stable. We also factor in storage guidelines: bellows should remain in controlled environments per ISO 2230 to maintain rubber elasticity. Testing shows axial stiffness deviation below 5% over 100,000 cycles, proving their long-term precision under variable load conditions.