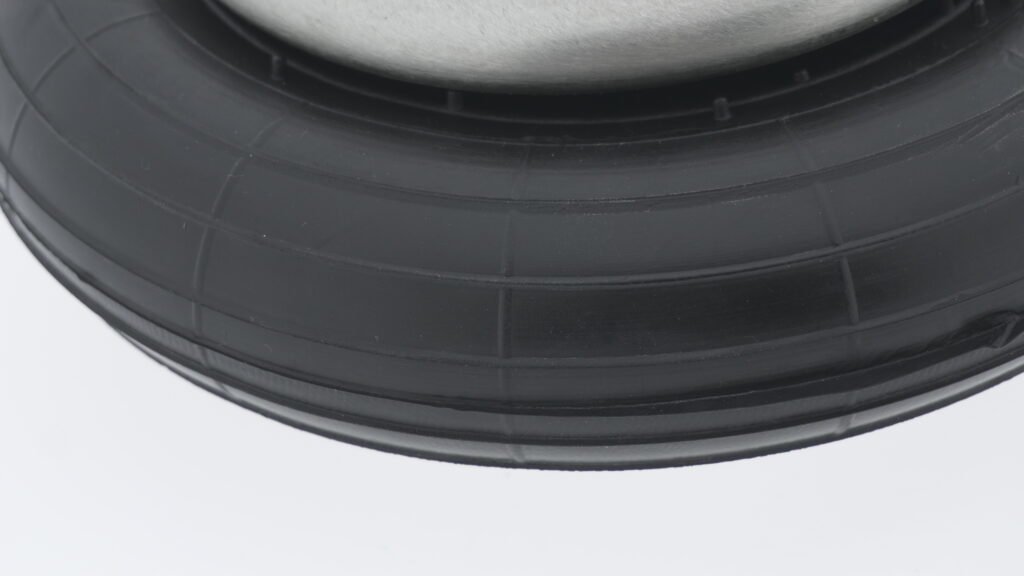
The automotive industry continues to evolve, demanding higher performance, durability, and adaptability from air bellows. As the market shifts towards advanced suspension systems, manufacturers and suppliers must align their offerings with modern requirements. Our focus is on the increasing global demand for air bellows and their impact on automotive applications. These components enhance ride stability, load-bearing capacity, and vibration reduction, ensuring optimal vehicle performance. With growing demand for energy efficiency, eco-friendly materials, and adaptive suspension systems, air bellows remain vital.
The Growing Role of Air Bellows in Automotive Engineering
Enhanced Suspension Systems
Modern vehicles, including commercial trucks, buses, and specialized transport, require air bellows to ensure optimal ride comfort and load distribution. The integration of air suspension improves vehicle longevity by reducing stress on mechanical components, leading to lower maintenance costs. These systems provide height adjustability, allowing ground clearance modifications for rough terrain. The ability to adapt to varying loads ensures consistent driving stability. Air bellows withstand intense vibration cycles, reducing shock transfer to the chassis. Their temperature resilience makes them suitable for extreme climate conditions.
Fuel Efficiency and Sustainability
Fuel efficiency remains a top priority in the automotive sector. Air bellows contribute to weight reduction, enhancing aerodynamics and fuel economy. As vehicle manufacturers seek to meet stringent emission regulations, air bellows play a crucial role in maintaining efficiency without compromising performance. Lightweight rubber-metal composites reduce unsprung mass, optimizing fuel consumption. Multi-layer elastomer structures improve air retention, ensuring pressure stability over extended periods. These properties extend air bellow lifespan, minimizing replacement frequency and waste generation.
Key Factors Driving Market Expansion
Technological Advancements
With advancements in rubber and metal composites, air bellows now offer higher durability, extended lifecycle, and better load capacity. The introduction of multi-layer elastomer compositions enhances temperature resistance, allowing usage in extreme environments. New vulcanization techniques strengthen bonding integrity, preventing delamination under stress. Hybrid polymer coatings further enhance abrasion resistance, extending operational performance. Precision-molded air chambers optimize airflow distribution, reducing energy losses in suspension applications.
Increasing Demand in Commercial Vehicles
Logistics and public transportation sectors continue to expand, driving the demand for high-performance air bellows. Fleets require durable suspension components to minimize downtime and operational costs, making air bellows an essential investment. Increased payload capacity, facilitated by multi-convolution designs, supports cargo transport efficiency. Anti-corrosion coatings improve longevity, reducing failure risks in high-humidity environments. Compact bellow configurations accommodate space-restricted chassis layouts without sacrificing ride comfort.
Rising Adoption in Electric Vehicles (EVs)
As EV adoption accelerates, manufacturers explore air suspension systems to enhance ride quality and battery efficiency. Air bellows support adaptive load balancing, crucial for optimizing EV performance. Smart control integration allows for automated height adjustments, improving aerodynamic efficiency. Lightweight air bellows offset EV battery weight, contributing to range optimization. Enhanced damping characteristics reduce vibrational stress on battery modules, extending operational lifespan.
Manufacturing Innovations in Air Bellows
Material Enhancements
Manufacturers continuously develop reinforced rubber compounds to improve tear resistance and elasticity. This ensures air bellows withstand high-pressure cycles while maintaining structural integrity. The latest four-ply construction increases load-bearing capacity, allowing air bellows to function at pressures up to 12 bar, compared to the standard 8 bar rating. This makes them suitable for heavy-duty applications such as off-road vehicles and military trucks. High-elasticity polymers improve shock absorption, minimizing fatigue failure in intensive operational environments.
Customizable Designs
Automotive manufacturers demand customized air bellows tailored to specific vehicle models. Variations in diameter, stroke capacity, and mounting types allow for optimal performance across applications. Some common size ranges include diameters from 80mm to 950mm, with load capacities ranging from 0.5 kN to 450 kN. These specifications ensure compatibility with both lightweight vehicles and heavy industrial transport. Tunable air chamber configurations optimize response rates for dynamic road conditions.
Corrosion-Resistant Components
Innovations in metallic components, such as stainless steel bead rings, enhance corrosion resistance. This is crucial for applications in harsh environments, such as off-road vehicles and heavy-duty trucks. Galvanized steel coatings offer protection against salt exposure, preventing premature failure in coastal regions.
The global demand for air bellows in the automotive industry continues to rise, fueled by technological advancements, sustainability goals, and expanding vehicle applications. As the industry shifts towards adaptive and energy-efficient solutions, air bellows remain an essential component of modern vehicle design. Companies must focus on innovation, customization, and quality assurance to stay ahead in this competitive landscape. The adoption of predictive maintenance tools, sensor-equipped suspensions, and eco-friendly materials will define the future of air suspension systems.