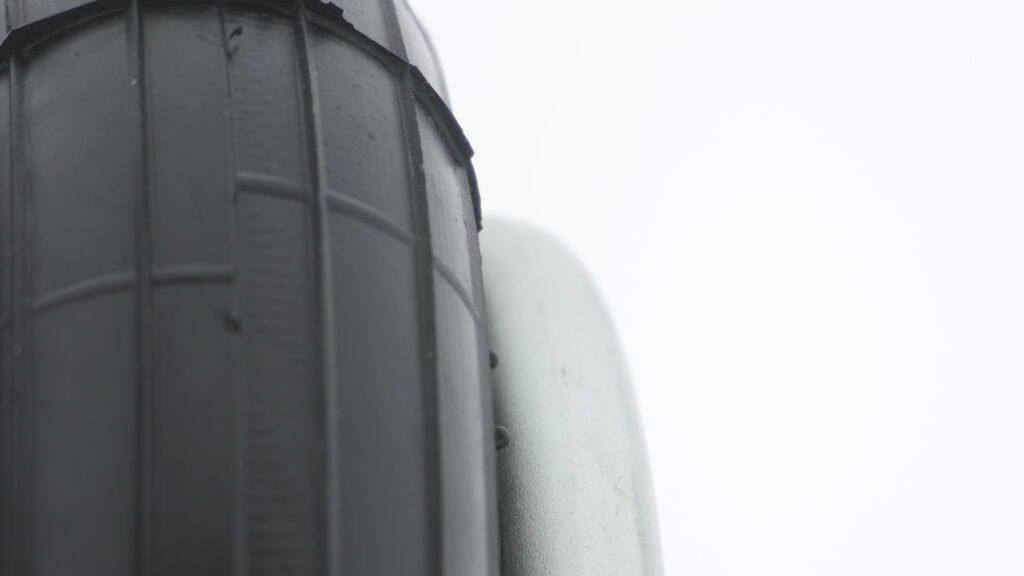
When operating in high-pressure environments, air bellows must withstand extreme conditions without compromising performance. At Tevema, we ensure that our air bellows meet stringent durability standards. Our testing protocols assess mechanical endurance, material resilience, and sealing efficiency. These tests guarantee superior load-bearing capacity and structural integrity. By focusing on high-performance elastomers, advanced reinforcement layers, and optimized production methods, we create air bellows capable of withstanding intensive workloads. These efforts lead to products that deliver enhanced stability, improved longevity, and consistent efficiency. Each stage of manufacturing is monitored to ensure compliance with industry standards. Our commitment to innovation ensures that our air bellows remain at the forefront of high-performance applications.
Key Factors Influencing Durability
1. Material Composition and Structural Integrity
The durability of air bellows depends on reinforced elastomers, high-strength steel, and precise manufacturing techniques. We utilize:
- Natural Rubber (NR/SBR): Superior flexibility and dynamic performance.
- Chlorobutyl (CIIR): Enhanced chemical resistance for aggressive environments.
- Nitrile (NBR): Exceptional oil resistance, perfect for hydraulic applications.
- Ethylene Propylene Diene (EPDM): Withstands high temperatures and ozone exposure.
Each material undergoes accelerated aging tests, such as elongation-at-break analysis, abrasion resistance evaluations, and hardness retention trials. The implementation of reinforced plies enhances structural stability, ensuring air bellows maintain integrity under constant pressure cycling and heavy loads.
2. Pressure Tolerance and Load Testing
Air bellows operate at pressures up to 12 bar, depending on ply count, reinforcement layers, and design specifications. Our load testing procedures evaluate:
- Axial load distribution under extreme pressure.
- Cyclic fatigue resistance over millions of cycles.
- Burst pressure thresholds beyond operational safety limits.
By integrating high-precision stress sensors, our tests provide real-time feedback on performance. This allows for continuous improvements in air bellow design and production processes.
3. Vibration and Shock Absorption Testing
High-pressure environments often induce mechanical vibrations that compromise system efficiency. Our air bellows undergo:
- Dynamic load simulations to assess compression-response efficiency.
- Vibration isolation assessments, ensuring up to 99% vibration dampening.
- Impact resistance trials to verify resilience under shock loads.
These tests help determine optimal material compositions and refine the balance between flexibility and reinforcement.
Testing Procedures for High-Pressure Durability
1. Thermal Stress Testing
To simulate real-world conditions, we subject air bellows to extreme temperatures from -40°C to +115°C. This process evaluates:
- Rubber elasticity at sub-zero temperatures.
- Heat aging resistance to confirm longevity.
- Thermal expansion coefficients under pressure variations.
Advanced thermal cycling equipment ensures that our air bellows meet thermal stability requirements, minimizing risks of material fatigue.
2. Salt Spray and Corrosion Resistance
In environments with chemical exposure, metal components must endure corrosion testing. We conduct:
- Salt spray tests per ISO 9227 standards.
- Chemical immersion tests for acidic and alkaline solutions.
- Galvanic corrosion analysis for stainless steel and aluminum alloys.
Protective coatings and advanced material treatments improve corrosion resistance, enhancing product durability.
3. Load Capacity and Burst Testing
Each air bellow is pressurized beyond its operational range to determine:
- Maximal force absorption capacity.
- Deformation limits under continuous loading.
- Safety margins for industrial applications.
Automated pressure monitoring provides real-time stress analysis, allowing for proactive design optimizations.
4. Fatigue Testing and Lifecycle Analysis
Fatigue is a major factor in air bellows performance. We simulate:
- 5+ million compression cycles under fluctuating pressure.
- High-frequency oscillation testing for continuous-use applications.
- Abrasion resistance tests to prevent premature wear.
By leveraging advanced wear-resistance materials, we enhance service life and minimize maintenance costs.
At Tevema, we push the boundaries of air bellow durability testing to ensure superior performance in high-pressure environments. Our rigorous quality control, material innovations, and precision engineering guarantee long-lasting reliability. Whether in transport, automation, or vibration isolation, our solutions are designed for unmatched durability and efficiency. By integrating state-of-the-art testing methodologies, we offer products that excel in structural resilience, load management, and performance stability. Our commitment to engineering excellence ensures that Tevema air bellows remain a trusted choice for high-pressure applications.