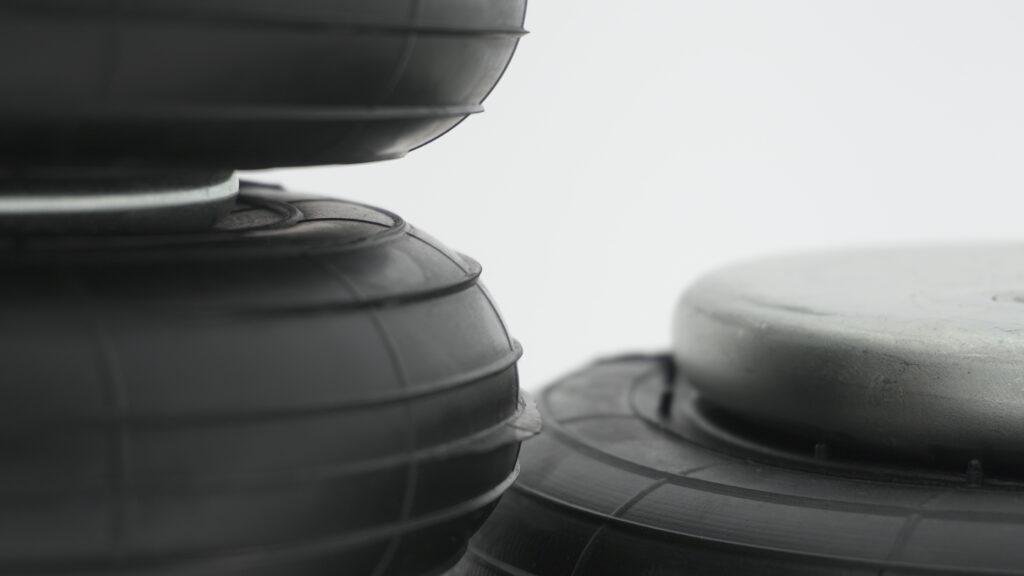
When working in tight machinery layouts, customising air bellows becomes a necessary step for proper system function and safety. We develop solutions for installations where space is limited in every direction. Our process begins with reviewing system drawings and identifying where off-the-shelf components fail due to spatial constraints. Compact environments demand shorter design heights, reduced diameters, and exact placement of ports and connections. We use single, double, and triple convolution setups depending on stroke and compression needs. Our modifications ensure a precise match to available clearances. Even within reduced dimensions, performance cannot be sacrificed. That’s why we support stroke ranges from 36 mm to 445 mm, even under high loads. Thread types are tailored to the machinery’s geometry. We maintain pressure limits and natural frequency requirements in every case. When every millimeter counts, we deliver high-performance bellows engineered for tight, complex environments where standard designs cannot operate.
Understanding dimensional limitations in tight installations
Confined environments limit not only vertical but also horizontal clearances, complicating actuator or isolator placement. We begin with precise spatial analysis to determine maximum and minimum allowable heights and diameters. Our bellows support compressed heights as low as 45 mm, making them ideal for shallow cavities. For height variation, strokes range up to 445 mm without structural compromise. Each custom model maintains full axial flexibility while preventing lateral bulging or misalignment. Design heights are optimized between 60 mm and 345 mm, depending on application demands. We select the right convolution count and reinforcement strategy to stay within these bounds. Port positions are adjusted to ensure easy connection access even in rear-mounted or side-mounted configurations. Standard inlet thread sizes can be rotated or moved. With careful planning, we avoid equipment redesign while increasing force output and maintaining consistent vibration isolation performance.
Selecting the right air bellow configuration
Each compact-space solution begins with choosing the ideal convolution type based on motion requirements and design height. Single convolution units are best when vertical space is severely limited. These units offer low internal volume and quick response times. Double convolutions provide additional stroke without significant increase in compressed height. For extended movement and better force absorption, triple convolution bellows are most appropriate. We pair each type with the right closure system: crimped, bead plate, or bead ring. Each format is selected based on mounting surface geometry and available tools. Crimped units are great for fixed systems with permanent sealing. Bead plates allow quicker replacements. Bead rings give flexibility in retrofit projects. All designs include standard port options and compatible connection sizes. Effective strokes range from 36 mm in low-profile units to 400+ mm in reinforced models. We make sure selected configurations provide both functional flexibility and structural compatibility.
Material selection for confined and harsh conditions
Tight installations often occur in challenging environments, including exposure to temperature extremes and aggressive chemicals. That’s why material choice is critical when customising air bellows. Our elastomer options include NR/SBR for general use and CIIR for acid resistance. Where oil or fuel exposure occurs, we recommend NBR. For outdoor or ozone-prone areas, we use EPDM or CR. All materials are reinforced with multi-ply fabric layers to enhance strength. For high-load or high-pressure applications, we offer four-ply versions. These allow safe operation up to 12 bar. Operating temperature ranges vary between -40°C and +115°C depending on the rubber compound. In enclosed spaces where ventilation is poor, these materials resist heat buildup and mechanical fatigue. Galvanized steel is used as default for metal parts, with AISI-304 or AISI-316L stainless available where corrosion resistance is needed. We adapt material selections to every confined-space application, ensuring maximum durability in minimum space.
Adapting air inlet and mounting points
Machinery often has predefined mounting and port locations, which must be honored when retrofitting or designing air bellows. Our customisation includes repositioning air inlets and mounting holes to align perfectly with the machinery’s geometry. We provide alternate drilling patterns, rotated port orientations, and offset hole locations. This eliminates the need for modification to the host system. For fixation, we offer multiple thread alternatives tailored to each application. Thread length and pitch can be adjusted to match the equipment’s build. We also integrate crimped plates with embedded ports for ultra-low profiles, down to 50 mm mounting height. Where bead ring designs are used, customers can select between socket head, countersunk, or threaded types. These details enable our air bellows to be installed even in systems with hard-to-reach mounting points. Adapted mounting ensures fast, secure attachment with no compromise to performance or maintenance accessibility.
Force and frequency optimization in small designs
Despite their compact size, our bellows can support high loads while delivering stable vibration control. We assess required force output at 7 bar and match that to the application using the smallest possible bellow. Load capacities range from 2 kN in smaller models to 450 kN in reinforced types. Vibration isolation is optimized with natural frequencies between 1.4 Hz and 3.9 Hz. These low frequencies allow for up to 99% vibration absorption, ideal for sensitive machinery in compact installations. We evaluate vertical and lateral flexibility to prevent overextension or deflection during operation. Our triple convolution models allow extended stroke while maintaining form under pressure. These bellows also compensate for structural misalignment, offering tilting up to 25°. Isolation efficiency is maintained without needing large coil springs or hydraulic dampers. Compact construction does not mean compromise. Our designs deliver strong force transfer and dynamic damping within extremely confined system envelopes.
Reinforcement strategies for compact high-load systems
Many tight installations still involve large static or dynamic loads. We strengthen our air bellows with multiple reinforcement techniques to handle such conditions. The base layer includes high-tensile rubber fabric, with two to four-ply configurations depending on force and pressure. For mounting strength, we use galvanized steel, AISI-304, or AISI-316L stainless. Steel bead rings increase structural integrity at the closure points. Crimped types use embedded plates with blind fasteners for a flush, compact finish. Maximum supported loads can reach 450 kN in specially reinforced bellows. Stroke control is fine-tuned to prevent peak stress conditions, extending service life. This is especially critical in high-cycle applications or equipment with constant vibration. We monitor deformation limits to keep height variation within safe tolerances. Diameters range from 80 mm to 950 mm, allowing compact or heavy-duty options. Our compact high-load bellows combine form, strength, and reliability into a unified design suitable for tight equipment housing.
Case-driven customization workflows
Every confined-space request starts with a detailed technical review of the client’s system. We study the available footprint, required stroke, and operating medium. This can include compressed air, oil, nitrogen, or water, depending on the environment. From there, we create tailored CAD models, ensuring mounting alignment, stroke allowance, and thermal compatibility. Throughout design, we factor in side loading, angular deflection, and lateral misalignment, up to 25°. These compensations help reduce precision requirements on customer-side alignment. We define port positions, connection types, and support geometry for plug-and-play functionality. Our design documentation includes full technical specs such as stroke, frequency, load range, and pressure rating. All information is shared with the client’s engineering and maintenance teams. This collaboration ensures installation readiness without unplanned adjustments. When customising air bellows, we prioritize clarity, compatibility, and long-term function. Our tailored workflows offer efficient integration, even in highly restricted machine compartments where redesigning the host equipment is not an option.