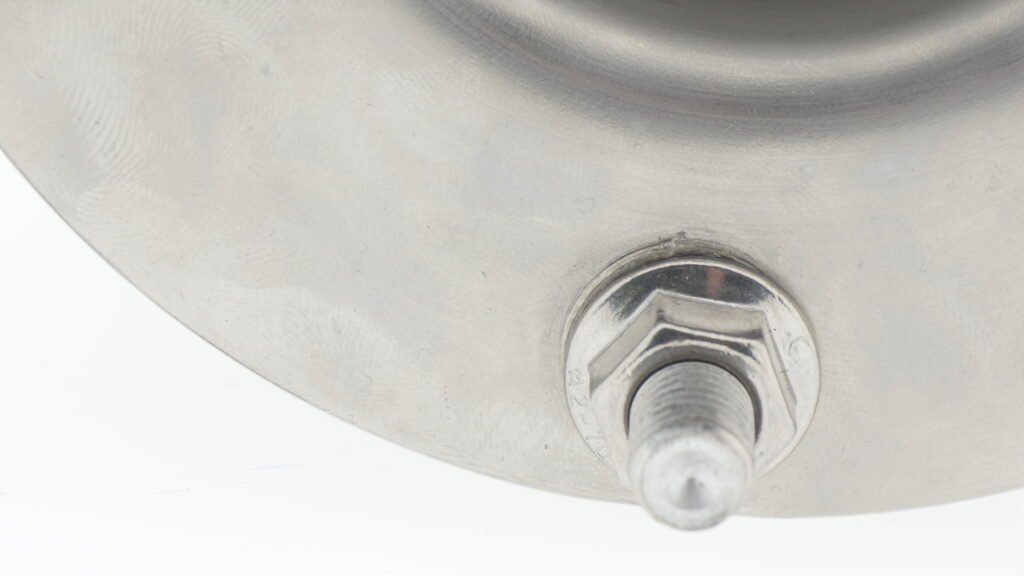
Maximizing Cost Efficiency with Air Bellows
In industrial machinery applications, cost efficiency is a critical factor for businesses seeking to enhance operational longevity and reduce maintenance costs. We integrate air bellows to optimize machinery performance, significantly cutting expenses on repairs, replacements, and energy consumption. By leveraging durable materials and innovative designs, our air bellows provide long-term financial benefits, improving shock absorption, reducing wear and tear, and extending lifespan. The latest four-ply construction air bellows withstand up to 12 bar pressure, offering enhanced load-bearing capacity. With reinforced fabric layers, they handle dynamic loads efficiently, preventing structural failures. Compared to conventional springs, air bellows last up to three times longer, making them an ideal investment. Their flexible structure absorbs vibrations effectively, reducing mechanical fatigue in heavy-duty applications. This ensures continuous machinery operation with minimal maintenance.
Durability and Reduced Maintenance Costs
The resilient elastomer compounds in our air bellows minimize material fatigue, preventing premature failure in heavy-duty applications. Our reinforced rubber layers withstand high pressure, ensuring stable operation at 8 to 12 bar. Compared to conventional springs, air bellows require little to no lubrication, reducing downtime and eliminating frequent maintenance expenses. This translates to lower operational costs over time. Additionally, the adaptive pressure control feature allows continuous load distribution, further preventing uneven stress on machinery components. The temperature resistance of our air bellows ensures functionality between -40°C and +115°C, making them suitable for extreme environments. The stainless-steel end fittings resist corrosion, increasing durability in chemical and moisture-prone industries. High-strength Kevlar-reinforced rubber options offer 40% greater tensile strength, making them ideal for intensive-use applications.
Key Maintenance Advantages
- Self-lubricating properties reduce the need for external lubrication.
- Corrosion-resistant materials extend lifespan in harsh environments.
- Adaptive pressure control minimizes component wear.
- Lower repair frequency, saving on replacement costs.
- High-strength fabric reinforcements ensure enhanced durability.
- Heat-resistant elastomers maintain performance in high-temperature applications.
Energy Efficiency and Operational Savings
Air bellows consume significantly less energy than traditional hydraulic or mechanical suspension systems. Their lightweight construction and efficient air pressure management reduce the strain on machinery motors, leading to decreased energy consumption. This improvement results in lower utility costs, especially for high-load applications. Air bellows also contribute to noise reduction, making industrial operations safer and more efficient. Advanced pressure regulation systems optimize air consumption, preventing unnecessary power wastage. The flexible design of air bellows enables precise motion control, reducing power fluctuations in automated systems. Tests show that air bellows reduce energy consumption by 20% in continuous-use applications, ensuring sustainable operation.
How Air Bellows Improve Energy Efficiency
- Low-friction movement reduces power loss.
- No sliding seals, eliminating energy losses due to friction.
- Optimized pressure control minimizes unnecessary energy use.
- Lightweight construction decreases overall equipment load, reducing fuel and energy consumption.
- Precision-controlled inflation optimizes performance for variable loads.
Extended Product Lifespan and Reliability
Unlike coil springs and hydraulic actuators, air bellows exhibit higher durability due to their flexible structure. The rubber-reinforced body and stainless-steel mounting plates ensure resilience against vibrations, chemical exposure, and temperature fluctuations. By maintaining structural integrity over prolonged usage, air bellows significantly reduce frequent component replacements, leading to long-term cost savings. With certified endurance tests, our air bellows last up to 1.5 million cycles under full load conditions. The Kevlar-reinforced versions withstand higher tensile stress, making them ideal for heavy-duty operations. Additionally, the sealed air chambers prevent moisture buildup, ensuring corrosion-free performance in humid environments.
Factors Contributing to Extended Lifespan
- Temperature-resistant elastomers for extreme conditions.
- High-strength reinforcement fabrics withstand continuous stress.
- Corrosion-resistant end plates ensure long-lasting durability.
- Dynamic load absorption prevents sudden mechanical failures.
- Multi-layer rubber composites offer enhanced fatigue resistance.
- Sealed structures prevent contaminant ingress, ensuring clean operation.
Applications in Machinery and Industry
Air bellows play a vital role in various industrial sectors, including automotive, manufacturing, and heavy-duty equipment. Their ability to handle high loads while maintaining operational stability makes them ideal for press machines, conveyor systems, and vehicle suspensions. We ensure that each air bellow design meets industry standards, offering customized solutions for specific applications. Our ISO 9001-certified production ensures consistent quality, making our air bellows a trusted solution for industrial applications.
Key Industrial Applications
- Automotive suspension systems for improved load balancing.
- Pneumatic actuators for precision control in assembly lines.
- Heavy-duty machinery dampers for shock absorption.
- Vibration isolators for reducing mechanical wear in sensitive equipment.
- Customized solutions for automated production lines.
- Energy-efficient suspensions for industrial transport vehicles.
Optimizing Investment: Cost vs. Benefit Analysis
Investing in air bellows results in long-term financial savings. The initial purchase cost is offset by reduced maintenance, lower energy consumption, and increased machinery lifespan. The use of multi-convolution bellows provides enhanced flexibility, making them a cost-effective alternative to metal springs. Furthermore, their compatibility with various industrial applications ensures high return on investment. In real-world case studies, companies using air bellows reported 25% reductions in maintenance costs, showcasing their financial benefits over time.
Cost-Saving Factors of Air Bellows
- Reduced wear and tear lowers replacement frequency.
- Lower energy consumption translates into significant cost reductions.
- Minimal maintenance requirements save labor and material costs.
- Longer operational lifespan improves investment efficiency.
- Adaptive designs allow modular upgrades, reducing replacement costs.
Integrating air bellows into machinery leads to substantial long-term cost savings. With enhanced durability, energy efficiency, and lower maintenance requirements, our air bellows provide an economical solution for various industrial applications. As industries seek sustainable and cost-efficient alternatives, air bellows emerge as an optimal choice for reducing operational expenses while ensuring performance stability.