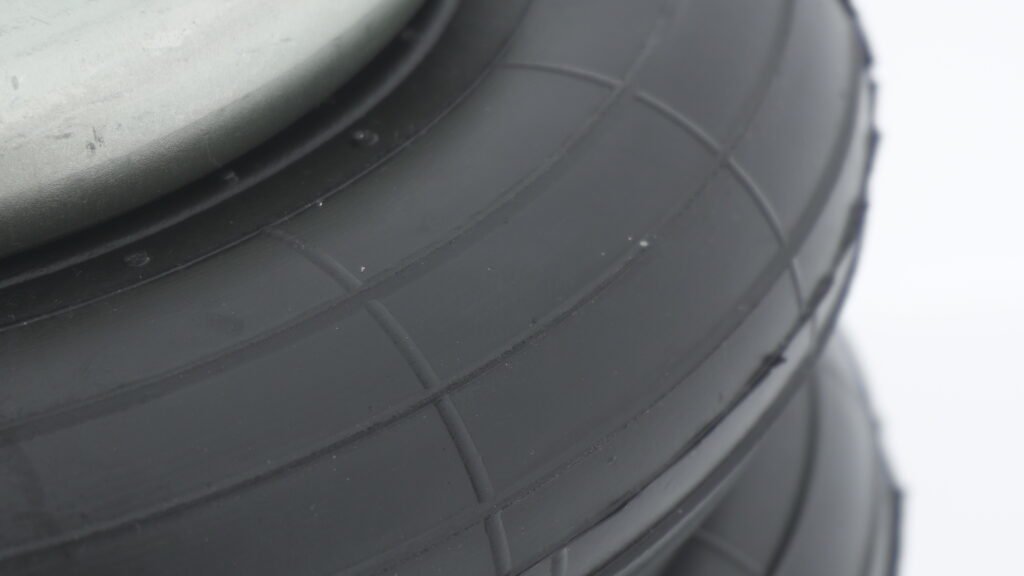
When it comes to air bellows, their versatility and performance often make them the go-to solution across industries. However, various misconceptions about air bellows persist, leading to improper usage, misjudged performance, or unnecessary costs. As experts in air spring technologies, we aim to clarify these misunderstandings and present accurate insights into the benefits and limitations of air bellows.
Each section of this article addresses a specific misconception to ensure clarity and detailed guidance for readers. By presenting facts, we hope to provide valuable insights into the practical applications and advantages of air bellows.
Misconception 1: Air Bellows Are Only for Heavy-Duty Applications
One common belief is that air bellows are exclusively suitable for large-scale operations, such as industrial vibration isolation or vehicle suspension systems. While air bellows excel in these areas, they are equally effective in smaller, more precise applications.
For instance, compact air bellows are frequently utilized in medical equipment, laboratory setups, and small-scale automation. These applications require reliability and adaptability, which air bellows provide effectively. Their innovative designs accommodate high flexibility while maintaining consistent performance under pressure.
Reality: Air bellows are available in a wide range of sizes, from diameters as small as 70 mm to over 600 mm. This flexibility is due to their modular design, allowing customization in stroke lengths, load capacities, and materials. Consequently, air bellows meet diverse industry needs beyond heavy-duty applications.
Misconception 2: All Air Bellows Are the Same
Another widespread myth is that all air bellows offer identical functionality. In truth, air bellows differ significantly in terms of materials, construction, and design variations.
Key Differences:
- Material Variations: Some bellows are made from synthetic rubber compounds, such as NR/BR or SBR, while others feature chlorobutyl for high-temperature resistance.
- Structural Configurations: Air bellows can be single convolution, double convolution, or triple convolution, each suited to specific operational needs.
Reality: Choosing the right air bellow depends on factors like operating pressure, temperature range, and vibration isolation requirements. For example, a stainless steel bellow may be necessary for corrosive environments, while rubber-based bellows are ideal for cost-sensitive applications. Such tailored solutions enhance efficiency and reduce operational risks.
Misconception 3: Air Bellows Require Complex Maintenance
The perception of air bellows as high-maintenance components often discourages their adoption. This notion stems from their pneumatic nature, leading users to assume frequent leak checks, lubrication, or alignment corrections are necessary.
Reality: Air bellows are nearly maintenance-free. Their frictionless operation and absence of internal moving parts eliminate the need for lubrication. Additionally, their robust design resists wear and tear under normal operating conditions, as long as pressure and alignment guidelines are followed. Proper maintenance practices ensure prolonged usability without significant additional costs.
Misconception 4: Air Bellows Are Not Suitable for Precision Applications
Some believe that air bellows lack the precision required for tasks involving fine control of motion or force output. This misconception overlooks the advanced engineering behind modern air bellows.
Reality: Air bellows offer remarkable positioning accuracy and consistent force output when integrated with precisely calibrated pneumatic systems. Their ability to adjust stroke length dynamically ensures accurate and repeatable results in applications like robotic automation or web tensioning devices. Moreover, their innovative construction supports smooth performance in sensitive environments.
Misconception 5: Air Bellows Cannot Withstand Extreme Conditions
Another frequent misunderstanding is that air bellows are incapable of performing in harsh environments, such as extreme temperatures or corrosive settings.
Reality: High-quality air bellows are designed with temperature-resistant materials, such as chlorobutyl rubber or ECO compounds, which operate efficiently between -40°C and +130°C. For added resilience, stainless steel end plates and reinforced components enhance their performance in corrosive or high-pressure environments. These materials ensure durability without sacrificing efficiency or safety.
Misconception 6: Air Bellows Have Limited Lifespan
Durability concerns often lead users to doubt the reliability of air bellows over extended periods.
Reality: Properly designed and installed air bellows, such as those from Tevema, can endure millions of cycles without failure. Their lifespan depends largely on adhering to recommended pressure ranges, installation heights, and load limits. Investing in quality materials and correct installation ensures prolonged, efficient service.
Best Practices for Optimal Air Bellow Performance
To maximize the benefits of air bellows, it is crucial to follow these key practices:
- Adhere to Operating Specifications: Ensure that the air bellows operate within their designated pressure and height ranges to avoid premature wear.
- Regular Inspections: Periodically check for air leaks, alignment issues, and surface damage. Early detection of issues ensures reliability.
- Use Appropriate Materials: Match the bellow material and design to the application’s environmental conditions for optimal performance.
- Follow Mounting Guidelines: Install the bellows securely, observing torque recommendations for fasteners and maintaining positional tolerances. Proper installation prevents unnecessary strain or misalignment.
By debunking these common misconceptions, we hope to enhance the understanding of air bellows and their unmatched versatility. Whether for vibration isolation, load bearing, or precise actuation, air bellows deliver dependable performance when applied correctly. As experts, we stand ready to assist you in choosing the right solution for your specific needs.
By following the outlined best practices and understanding their true capabilities, users can confidently integrate air bellows into various applications.