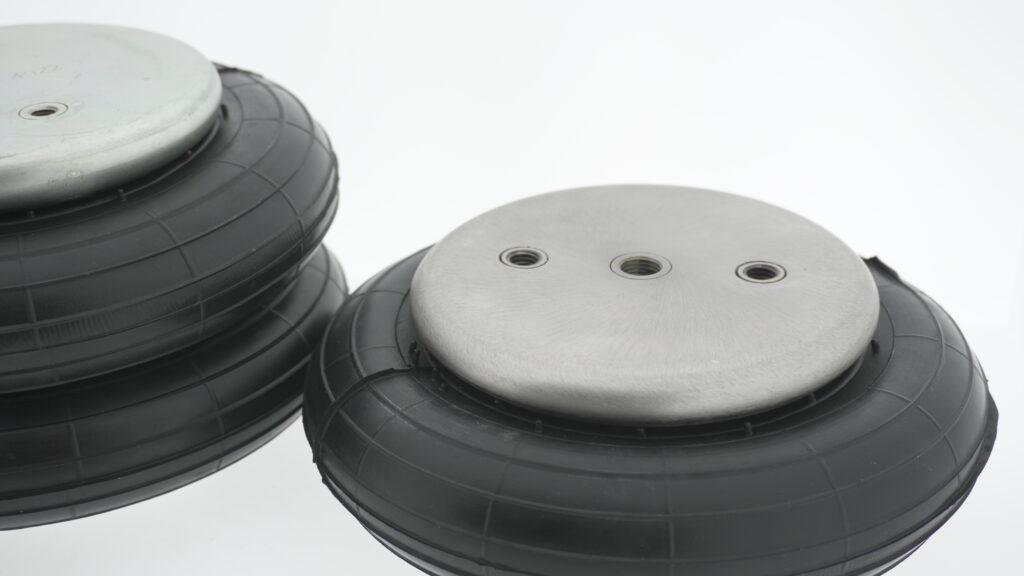
Finding the Right Balance for Your Needs
Selecting the right air bellows requires a careful balance between performance and cost-effectiveness. Businesses rely on these components for reliable force transmission, vibration isolation, and structural support. However, without a strategic approach, one may either overinvest in unnecessary features or compromise on quality. Understanding key parameters, such as material composition, pressure capacity, and durability, ensures the optimal balance between efficiency and budget constraints. Standard single convolution bellows have diameters ranging from 80 mm to 410 mm, providing different levels of load absorption. Double and triple convolution models extend stroke length, reaching up to 400 mm for added flexibility. With working pressures from 8 bar to 12 bar, different configurations handle load capacities between 2.4 kN and 450 kN, making them ideal for various applications.
Material Considerations: Steel vs. Aluminum
Choosing the correct metallic components is a major factor in cost and durability. Electro-galvanized steel is a common standard, offering a balance of corrosion resistance and structural integrity. For applications demanding higher resistance to chemicals, stainless steel AISI-304 is a superior choice. In cases where weight reduction is crucial, aluminum provides a lighter alternative without significantly sacrificing strength. Standard steel components maintain structural integrity under pressures up to 12 bar, while stainless steel improves chemical resistance and longevity. Aluminum-based bellows offer a weight reduction of up to 40%, making them suitable for weight-sensitive applications. The choice of materials impacts lifespan, load absorption efficiency, and temperature resistance, ensuring that the selected air bellows meet specific industrial demands.
Understanding Pressure Ratings and Load Capacities
The maximum allowable pressure of standard air bellows is typically 8 bar, but certain designs allow for pressures up to 12 bar. The choice between single, double, or triple convolution designs impacts stroke capacity, load resistance, and stability. Larger diameters and multi-ply reinforcement enhance force output, making them ideal for high-load environments. Single convolution bellows typically handle forces between 2.4 kN and 70 kN, whereas double convolution units accommodate loads up to 180 kN. Triple convolution bellows can exceed 400 kN, depending on reinforcement layers. High-strength four-ply constructions further improve pressure retention, ensuring consistent performance under demanding conditions. Pressure rating, load capacity, and stroke length must align with the operational requirements, ensuring an optimal balance between cost and performance.
Installation Efficiency and Design Configurations
Mounting options significantly impact ease of installation and adaptability. Various configurations, including bead ring, crimped, and dismountable designs, allow for custom integration. The selection depends on factors such as space constraints, misalignment tolerances, and maintenance requirements. Threaded inserts, socket head fasteners, and custom plate fittings further optimize compatibility. Bead ring designs allow for quick disassembly, ensuring easy replacement and maintenance. Crimped air bellows provide a permanent sealing solution, reducing the risk of leakage and enhancing durability. Dismountable air springs offer flexible installation, with threaded holes allowing for direct mounting onto equipment frames. Selecting the right configuration improves operational efficiency, reduces maintenance costs, and extends the service life of air bellows.
Optimizing Vibration Isolation Performance
One of the primary advantages of air bellows is their ability to provide exceptional vibration isolation. Their natural frequency can be regulated by adjusting air pressure, ensuring consistent operational stability. This reduces mechanical wear, extends machine lifespan, and minimizes noise transmission. A properly tuned system can achieve more than 99% vibration reduction, outperforming traditional coil springs. Vibration absorption efficiency depends on factors such as convolution type, air volume, and mounting configuration. With a natural frequency range between 1.2 Hz and 4.6 Hz, air bellows significantly reduce harmful oscillations. High-flexibility models allow for angular displacement of up to 25°, further improving shock absorption. These features contribute to longer-lasting equipment, reducing the risk of structural fatigue and operational failures.
Long-Term Cost Benefits: Maintenance and Longevity
Investing in high-quality air bellows reduces operational costs over time. Unlike conventional actuators, air bellows have no sliding seals, resulting in minimal wear and tear. Additionally, they are resistant to environmental degradation, ensuring longevity in harsh operating conditions. ISO 2230 storage guidelines help maintain rubber integrity and prevent premature aging. Air bellows made of NR/SBR compounds can withstand temperatures between -40°C and 70°C, while EPDM versions offer extended heat resistance up to 115°C. Proper storage conditions, avoiding direct sunlight and ozone exposure, further extend service life. Unlike hydraulic actuators, which require regular lubrication, air bellows operate maintenance-free, ensuring lower total cost of ownership.
Choosing the Best Air Bellows for Your Application
To maximize the cost-performance ratio, businesses must align technical specifications with operational demands. Consider the following criteria:
- Material selection for longevity and chemical resistance
- Pressure rating to match load requirements
- Convolution type for stroke capacity and force output
- Mounting configurations for installation flexibility
- Vibration isolation capabilities to protect machinery and structures
- Temperature tolerance to ensure compatibility with environmental conditions
When selecting air bellows, balancing performance and price requires a comprehensive understanding of material properties, pressure tolerances, and installation factors. Making the right choice ensures long-term reliability, cost efficiency, and optimal functionality. By carefully evaluating technical specifications and operational needs, businesses can make informed decisions that maximize both value and performance. Choosing reinforced constructions, selecting appropriate materials, and optimizing installation ensures efficient system performance, reducing unexpected downtimes and maintenance costs.