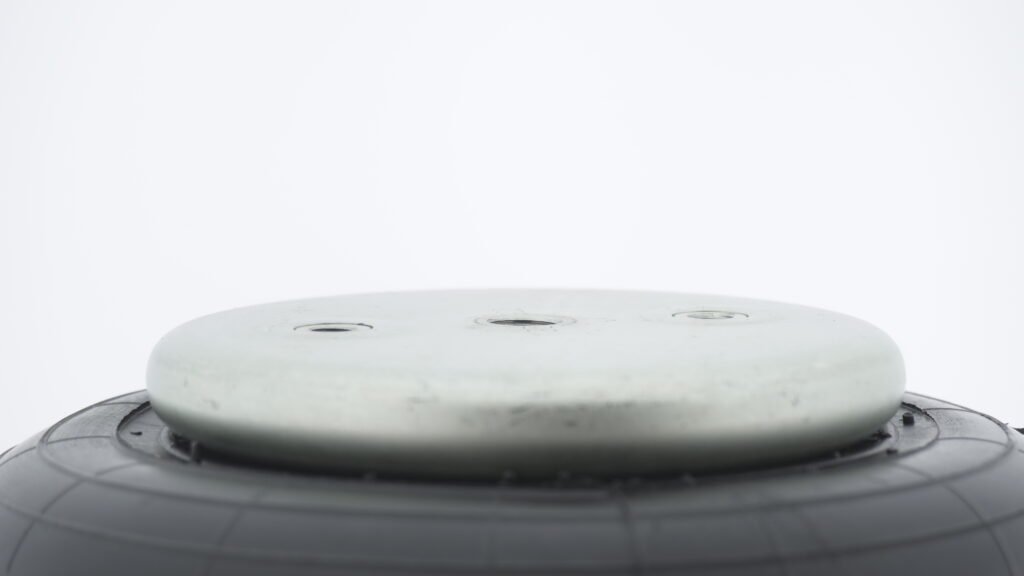
When selecting an actuation or vibration isolation solution, engineers must compare air springs and hydraulic actuators based on performance, cost, and application needs. Both technologies play crucial roles in industrial, automotive, and heavy machinery applications. Understanding their fundamental differences helps determine the best choice for your system. Air springs offer great vibration isolation and adaptability by adjusting stiffness and load capacity dynamically. Meanwhile, hydraulic actuators are recognized for their high-force output and precision. Key factors that differentiate them include their working principles, response time, environmental impact, and long-term costs. To make an informed choice, industries must evaluate the operational environment, performance parameters, and maintenance constraints. This article presents a detailed comparison of air springs and hydraulic actuators to determine which option best fits industrial applications.
Operational Principles
Air Springs
Air springs, also called pneumatic actuators, use compressed air to generate force and movement. They consist of a flexible rubber bellow that expands or contracts as air pressure changes. This provides smooth motion and excellent vibration isolation. These systems work well in applications needing adjustable stiffness, load balancing, and damping control. The rubber structure, reinforced with fabric plies and steel beads, ensures durability. Design variations, including single, double, and triple convolutions, allow adaptability in different load conditions. Air springs resist external contaminants like dust, debris, and moisture. Their lack of moving seals reduces wear, increasing their lifespan. Industries such as transportation, heavy equipment, and automation use air springs as a cost-effective alternative to rigid actuators. Their flexible function and durability make them valuable across many applications.
Hydraulic Actuators
Hydraulic actuators use pressurized fluid to generate linear or rotational motion. A hydraulic pump pushes fluid into a chamber, moving a piston to create force. These systems are known for high force output and precise control. They work best in heavy-duty applications needing constant force, such as construction, aerospace, and industrial machinery. Hydraulic actuators perform well under extreme pressure conditions. Their key benefit is their incompressible fluid, ensuring minimal energy loss and precise force transmission. However, they need regular maintenance, including fluid changes, leak checks, and seal inspections. Complex components such as pumps, valves, and reservoirs increase both cost and maintenance demands. Despite their upkeep needs, hydraulic actuators remain essential in applications demanding accuracy, sustained force, and controlled movement.
Key Performance Comparisons
1. Force and Load Capacity
- Hydraulic actuators provide high force output because hydraulic fluid is incompressible. They are best for construction, aerospace, and metal stamping applications. Their ability to maintain force under variable loads makes them ideal for precision manufacturing and industrial robotics.
- Air springs generate substantial forces but have a lower force-to-weight ratio. Adjusting air pressure easily modulates force, allowing load adaptability. They are used in vibration damping, height adjustment, and shock absorption. Air springs offer silent operation, minimal maintenance, and adjustable performance through air pressure control.
2. Precision and Control
- Hydraulic systems provide high precision and stability, especially in applications needing controlled movement. Their ability to maintain constant force and accurate positioning makes them crucial in robotics, injection molding, and CNC machinery.
- Air springs, while effective, have minor elasticity due to air compressibility. This makes them less ideal for tasks requiring pinpoint accuracy. However, they excel in cushioning, vibration damping, and load variation support. Their ability to adjust stiffness quickly enhances machine stability, ergonomic workstations, and impact-sensitive equipment. Hydraulic actuators provide fine control through pressure adjustments, ensuring steady and repeatable performance. While air springs may lack rigid precision, their adaptability to changing loads makes them useful in many industrial settings.
Choosing the Right Solution
- Air springs work best for vibration isolation, height adjustment, and maintenance-free applications like vehicle suspensions, conveyor systems, and industrial presses. They handle harsh environmental conditions, temperature changes, and corrosive substances effectively.
- Hydraulic actuators suit high force, precision, and constant pressure applications, such as heavy machinery, robotic arms, and aerospace systems. Their ability to deliver continuous power transmission with minimal energy loss makes them ideal for marine, mining, and defense industries. While hydraulic actuators require complex installation and upkeep, they excel in motion control, synchronized movement, and heavy load-bearing tasks. Engineers must consider cost, environmental impact, and operational efficiency when selecting an actuation technology.
Both air springs and hydraulic actuators serve different purposes, with advantages suited to specific industries. If cost-efficiency, low maintenance, and vibration isolation are top priorities, air springs are the better choice. For applications needing extreme force and precision, hydraulic actuators are unmatched. Engineers must analyze their operating environment, force needs, and long-term costs to select the best solution. Whether focusing on low operating costs, energy efficiency, or adaptability, each actuation method has unique benefits. In today’s engineering landscape, choosing the right motion control technology greatly impacts system reliability, durability, and performance.