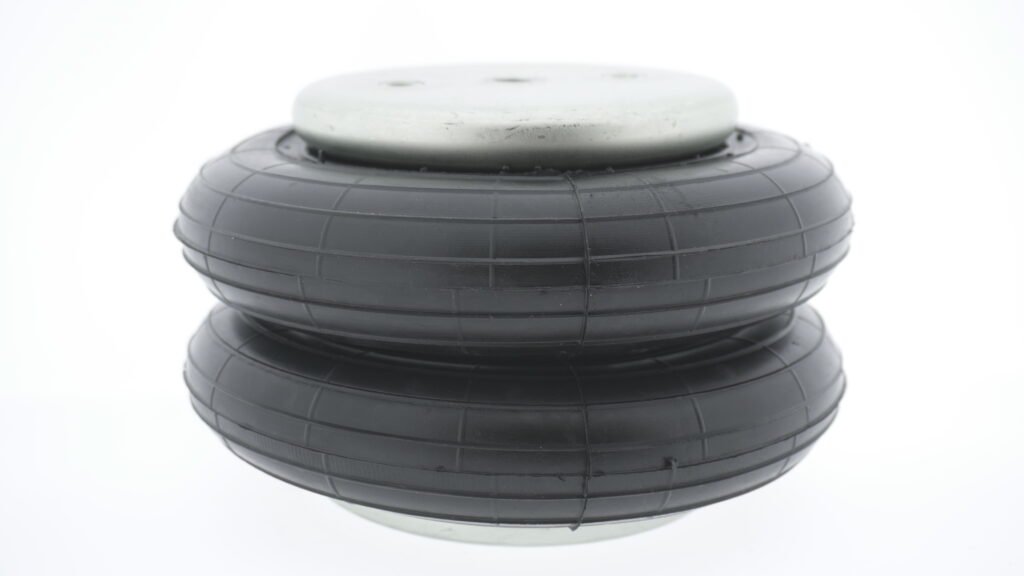
Efficiency in Industrial and Automotive Applications
Selecting the optimal vibration isolation or suspension system for heavy-duty machinery and vehicles requires understanding two prominent choices: air bellows and shock absorbers. Each system has unique strengths and limitations, making them suitable for various applications. This article provides a detailed comparison to determine which solution is best for your specific needs. By analyzing their functionality, cost implications, and performance metrics, industries can make informed decisions to enhance operational efficiency and durability. Ultimately, understanding these differences can lead to improved system performance and reduced downtime. Choosing the correct system not only benefits the equipment but also maximizes long-term savings and operational effectiveness
Core Differences: Functionality and Design
Air Bellows: Precision and Versatility
Air bellows are flexible components composed of reinforced rubber and metal. Using compressed air, they excel in both actuator and vibration isolation roles. Their compact height and adaptable design make them ideal for diverse applications. Key features include custom pressure adjustments to maintain consistent operational height, high load capacities supporting up to 380 kN per unit, and compatibility with various media, such as nitrogen, oil, and water. These attributes make air bellows an efficient solution for industrial and automotive sectors where precision and versatility are crucial.
Shock Absorbers: Simplicity and Durability
Shock absorbers are linear dampers converting kinetic energy into heat to reduce motion. Typically employing hydraulic fluid, they are effective in dynamic scenarios, like vehicles on uneven terrain. Benefits include reliable high-frequency oscillation damping, straightforward integration into systems, and robust resistance to environmental damage. These features make them a dependable choice for managing rapid, consistent motion in various operational settings. However, their limited flexibility compared to air bellows can restrict their suitability for precision-based applications.
Performance Metrics
Vibration Isolation
Air bellows provide superior vibration isolation, reducing up to 99% of unwanted vibrations. This capability minimizes structural damage and prolongs machinery lifespan, making them invaluable for stationary industrial equipment. Conversely, shock absorbers focus more on motion damping than isolation, making them less suitable for sensitive applications requiring high precision.
Energy Efficiency
Air bellows are energy-efficient due to their adjustable pressure capabilities, reducing operational costs over time. In contrast, shock absorbers rely on continuous hydraulic motion, which can be energy-intensive. This efficiency disparity highlights the cost-saving advantages of air bellows in large-scale or long-term operations.
Maintenance Requirements
Air bellows require minimal maintenance, thanks to their durable rubber construction and lack of sliding seals. Conversely, shock absorbers demand regular servicing, including hydraulic fluid replacement, which can increase downtime and costs. This maintenance contrast impacts the overall cost-effectiveness and reliability of each system.
Application Scenarios
Air Bellows: Industrial Precision
Air bellows excel in:
- Heavy Machinery: Absorbing vibrations in compressors, turbines, and presses.
- Height Control Systems: Adjusting height for conveyor belts or automated systems.
- Railway Suspension: Enhancing lateral stability and tilt absorption. These qualities demonstrate their adaptability and precision across industrial settings.
Shock Absorbers: Dynamic Performance
Shock absorbers perform well in:
- Automotive Applications: Ensuring comfort and stability for passengers.
- Aerospace Systems: Managing forces in landing gear setups.
- Construction Equipment: Stabilizing loads on dynamic vehicles. These examples highlight their robustness and reliability in motion-intensive environments.
Material Considerations
Air bellows are available in diverse elastomer compounds, including:
- Natural Rubber (NR/SBR): General-purpose, dynamic applications.
- Nitrile (NBR): Oil and fuel-resistant for outdoor use.
- EPDM: Superior temperature and ozone resistance for harsh climates. These materials allow customization for various environments.
Shock absorbers use high-strength steel and hydraulic systems, providing durability but limiting adaptability. Their rigidity can restrict their effectiveness in applications demanding flexibility and environmental compatibility.
Cost Analysis
Air bellows often have a higher initial cost but offer significant savings over time due to their durability, energy efficiency, and low maintenance needs. Their total cost of ownership is typically lower compared to shock absorbers, which require ongoing servicing. This cost advantage makes air bellows a preferable choice in industrial applications focused on long-term efficiency.
The choice between air bellows and shock absorbers depends on application-specific needs. Air bellows deliver unmatched precision, vibration isolation, and versatility, ideal for stationary and industrial uses. Shock absorbers excel in dynamic, motion-intensive scenarios, such as automotive and aerospace applications. By weighing factors like performance, cost, and maintenance, industries can choose the optimal system to maximize efficiency and reliability, ensuring superior operational outcomes.