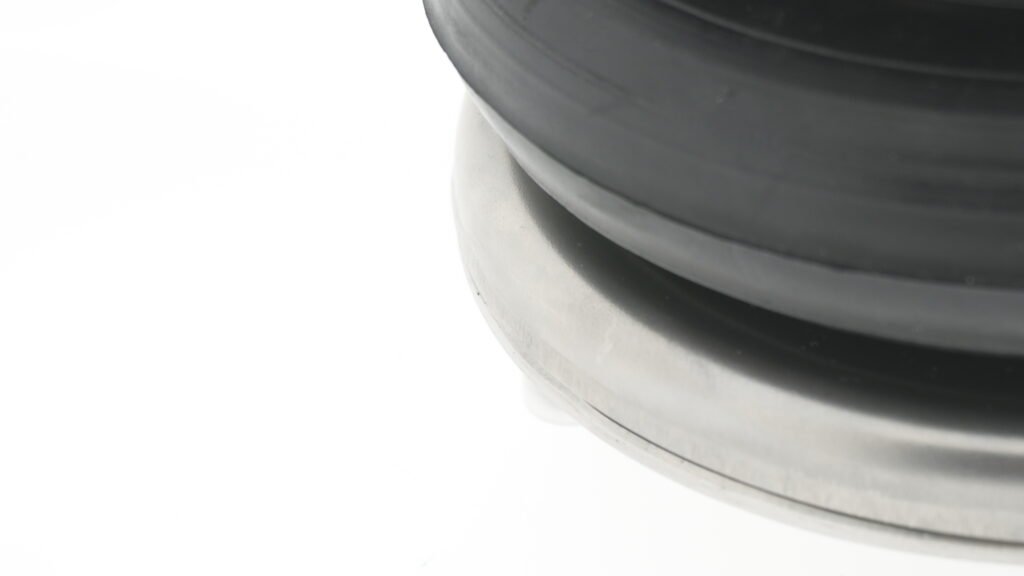
Enhancing Performance and Longevity in Rock Crushers
Rock crushing equipment operates under extreme conditions, requiring high-performance air bellows to withstand vibration, impact, and pressure fluctuations. Air bellows play a crucial role in protecting machinery, reducing downtime, and improving overall efficiency. These components consist of reinforced elastomeric materials with steel bead rings for durability. They function by absorbing dynamic forces, preventing structural fatigue, and mitigating impact loads. With adjustable air pressure, air bellows allow for precise force modulation, ensuring optimal system response. Their design accommodates lateral misalignment up to 30 mm and angular movement up to 25 degrees. By utilizing high-quality elastomers such as NBR (Nitrile) for oil resistance or EPDM for extreme temperature durability, they outperform conventional suspension components. Integrating these elements results in fewer breakdowns, lower maintenance costs, and improved rock crusher longevity.
Shock Absorption in Vibrating Screens
Rock crushing plants rely on vibrating screens to separate crushed material by size. These screens generate high-frequency vibrations that can cause premature wear and damage to mechanical components. Air bellows effectively absorb these vibrations, offering superior shock isolation compared to conventional coil springs. Each unit is designed to handle frequencies as low as 1.5 Hz at 6 bar pressure, ensuring optimal damping capacity. Air bellows prevent excessive vibrations from affecting screen decks, motor mounts, and frame structures. The use of four-ply reinforced rubber construction enhances durability and maintains performance even in extreme conditions. Air pressure adjustments between 4 and 12 bar allow for adaptable stiffness settings. By implementing these isolators, mining operations experience fewer mechanical failures, extended equipment service life, and reduced energy consumption. Regular inspections of sealing integrity and air pressure levels further enhance operational efficiency.
Impact Reduction in Jaw Crushers
Jaw crushers exert immense force to break large rocks into smaller aggregates. The impact forces generated during operation can lead to structural fatigue, affecting the crusher’s efficiency. Air bellows serve as damping elements between critical components, significantly reducing impact loads. With stroke capacities ranging from 50 mm to 375 mm, these components mitigate excessive shock loads. Their high-energy absorption prevents metal fatigue and frame deformations, increasing reliability. Air bellows with stainless steel bead rings (AISI-304) offer enhanced corrosion resistance in high-moisture environments. By absorbing vibrations, these components protect jaw crusher bearings, shafts, and frame components from premature wear. Adjustable air pressure optimizes stiffness, ensuring consistent performance across variable loads. The ability to withstand up to 450 kN of force per bellow makes them ideal for heavy-duty applications. Routine maintenance, including pressure adjustments and leakage inspections, further ensures their effectiveness in rock crushing environments.
Enhancing Conveyor Belt Systems
Conveyor belts transport crushed rock from one processing stage to another. Uneven loading and heavy material impact can lead to misalignment and excessive wear. By integrating air bellows into the conveyor support system, shock absorption is optimized, reducing mechanical stress and preventing frequent maintenance interruptions. These units offer high axial load capacities up to 300 kN, ensuring stable operation under extreme conditions. Air bellows compensate for uneven material distribution, maintaining belt tension and reducing slippage. Their resistance to oil, dust, and environmental contaminants makes them ideal for heavy-duty conveyors. High-performance elastomers, such as Chlorobutyl (CIIR), prevent degradation in harsh conditions. By using air bellows, conveyor belt lifespan increases, and energy consumption decreases. Periodic inspections of mounting integrity and air leakage prevention further contribute to reduced downtime. Implementing these solutions results in improved material handling efficiency and reduced maintenance costs.
Dust Control and Sealing Applications
Dust is a major concern in rock crushing operations, leading to environmental hazards and mechanical failures. Air bellows are used in sealing applications to create flexible barriers around critical components, preventing dust infiltration. With their hermetic sealing properties, these units effectively block fine particulate matter from entering machinery. Rubber-reinforced fabric layers improve elasticity and enhance sealing efficiency. Depending on the application, air bellows can be manufactured with hydrophobic coatings to resist moisture absorption. The inclusion of high-strength bead rings ensures durability, preventing leaks under variable pressure conditions. Their resistance to chemicals and extreme temperatures makes them ideal for harsh environments. These features prevent contamination in bearings, gears, and hydraulic systems. Regular maintenance, including pressure adjustments and physical inspections, ensures long-term reliability. By integrating air bellows for dust control, operators reduce component failures and improve compliance with environmental regulations.
Precision Adjustment in Cone Crushers
Cone crushers rely on precision movement to achieve the desired rock size reduction. Air bellows provide controlled axial motion, enabling fine-tuned gap adjustments between the crushing surfaces. Their ability to expand and contract under pressure allows for smooth and accurate positioning, ensuring consistent product quality. These actuators feature low-friction, self-lubricating materials, preventing wear during frequent adjustments. Stroke lengths ranging from 50 mm to 350 mm allow for customized movement control. The use of multi-layer rubber reinforcement ensures consistent force application without premature fatigue. With pressure adjustability between 4 bar and 12 bar, stiffness can be fine-tuned to accommodate different material densities. Air bellows reduce impact shocks on internal components, preventing costly repairs. Their high-strength design enables precise adjustments while maintaining durability in harsh conditions. Regular air pressure calibration ensures optimal efficiency, improving overall cone crusher performance and reliability.
Advantages Over Conventional Suspension Systems
Unlike traditional metallic springs, air bellows offer:
- Superior vibration isolation, reducing wear and tear.
- Adjustable stiffness by varying air pressure.
- Corrosion resistance, ideal for harsh environments.
- Compact design, allowing flexible installation in tight spaces.
- Long service life, minimizing operational costs.
These advantages make them an essential component in modern rock crushing operations. Their ability to withstand high dynamic loads and extreme conditions enhances machinery performance and longevity.
Installation and Maintenance Best Practices
To maximize efficiency, proper installation and routine inspection of air bellows are essential:
- Ensure correct alignment to prevent uneven stress.
- Monitor air pressure levels for optimal performance.
- Inspect for leaks or wear periodically.
- Use stainless steel fittings in corrosive environments.
Following these best practices enhances reliability, reducing downtime and maintenance costs in rock crushing facilities.
The integration of air bellows in rock crushing equipment significantly enhances operational efficiency, equipment longevity, and maintenance cost reduction. Their ability to absorb impact, control vibration, and improve precision adjustment makes them an essential component in modern rock processing facilities. Air bellows designed with four-ply high-strength rubber withstand extreme forces while providing superior shock absorption. By selecting high-quality elastomers, operators achieve optimal performance under extreme conditions. Proper maintenance practices, including periodic inspections and pressure adjustments, further improve reliability. Implementing air bellows leads to reduced downtime, increased productivity, and extended machinery lifespan.