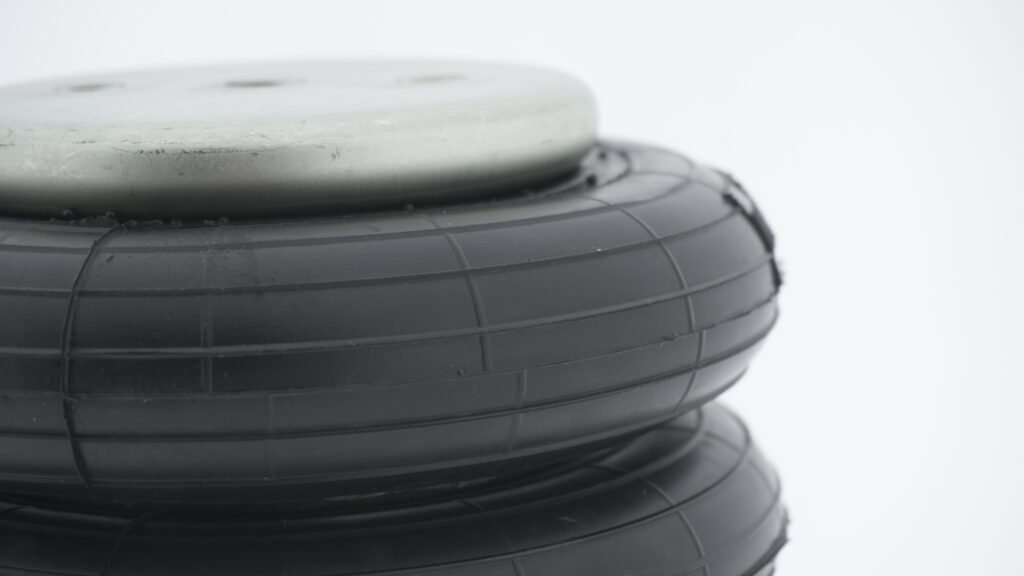
Air bellows, also known as air springs or air actuators, are indispensable components in industrial and vehicular applications. They excel in load-bearing, vibration isolation, and height control across various conditions. But one critical question remains: can they operate effectively in extreme temperatures? As specialists in this field, we will explore this issue in depth, highlighting performance factors, material considerations, and practical solutions.
The Impact of Extreme Temperatures on Air Bellows
Temperature Extremes and Material Performance
Air bellows encounter diverse temperature environments, ranging from sub-zero conditions to high-heat industrial settings. Their functionality largely depends on the elastomer compounds and metallic parts used in their construction.
Air bellows must remain functional in temperatures as low as -40°C (-40°F), where standard natural rubber may become brittle. In contrast, high-temperature settings, such as +115°C (239°F), require materials like ethylene propylene diene monomer (EPDM). The choice of elastomer ensures operational reliability. For instance, chlorobutyl (CIIR) is ideal for environments with high acid exposure, while nitrile rubber (NBR) is well-suited for oil and fuel-heavy applications.
Metallic parts also play a role in ensuring heat resistance. Electro-galvanized steel is commonly used, but AISI-316L stainless steel offers enhanced durability in high temperatures or corrosive conditions. This dual focus on elastomer and metal design enables air bellows to endure harsh conditions effectively.
Metallic Components and Heat Resistance
Metallic components, such as electro-galvanized steel or AISI-304 stainless steel, ensure structural integrity. In extreme conditions, AISI-316L stainless steel offers enhanced corrosion resistance, making it suitable for environments with chemicals, oils, or saline exposure. The integrity of metallic parts is crucial when air bellows face rapid temperature fluctuations. This resilience protects against deformation or structural failure during prolonged use in harsh conditions. Proper material selection ensures performance stability over time.
Key Factors for Optimal Performance
Material Selection
The elastomer and metal type dictate the air bellow’s ability to withstand temperature extremes. Proper selection ensures:
- Elasticity retention in sub-zero conditions.
- Durability against thermal expansion in high heat.
For applications requiring higher pressure and temperature tolerance, four-ply constructions provide additional strength, allowing operation at pressures up to 12 bar. Ensuring that the air bellows use the right elastomer compounds, such as EPDM or CIIR, can maximize durability in extreme environments. Additionally, choosing high-quality metals enhances resistance to temperature-induced fatigue.
Pressure Regulation
Maintaining the appropriate air pressure is critical. Over-pressurizing air bellows in extreme heat can lead to material fatigue, while under-pressurization in cold conditions might reduce load-bearing capabilities. Ensuring that air bellows operate within their pressure limits preserves their structural integrity. Regular pressure checks mitigate the risks of overstrain or reduced performance during temperature extremes.
Environmental Isolation
Environmental factors, such as exposure to ozone, UV radiation, or chemical vapors, can exacerbate the effects of extreme temperatures. EPDM rubber, with its exceptional resistance to ozone and weathering, is an ideal solution for outdoor applications. Installing protective barriers or coatings further extends the lifespan of air bellows. These measures protect sensitive components from environmental stressors.
Applications in Extreme Conditions
Automotive Industry
In vehicles, air bellows are often exposed to temperature fluctuations, from cold climates to high-heat engine compartments. They are designed to:
- Isolate vibrations for smoother rides.
- Adjust suspension height, ensuring load stability.
- Withstand high operational temperatures, especially in trucks and buses.
Air bellows in the automotive sector must meet rigorous standards to function reliably under rapid temperature changes. Choosing durable materials and integrating precise control systems are essential to sustaining performance.
Industrial Settings
In industrial applications, air bellows face challenges such as:
- Prolonged exposure to furnace heat.
- Cold storage environments requiring flexibility and resilience.
- Chemical and oil resistance in manufacturing plants.
Using materials like chloroprene rubber (CR) ensures resistance to both oils and weathering, making it suitable for such demanding environments. Industrial air bellows often feature enhanced pressure and temperature tolerance, allowing them to handle the heavy loads and challenging conditions found in factories and plants.
Solutions for Enhancing Performance
Regular Maintenance
Routine inspections and replacements of worn components prevent failures. Ensure that air bellows are:
- Stored in cool, dry environments (as per ISO 2230).
- Free from exposure to ozone-producing equipment or direct sunlight.
Regular maintenance ensures operational longevity, especially in applications where air bellows are subject to constant load and environmental stress. A proactive approach minimizes downtime and reduces long-term costs.
Customized Designs
For applications with specific requirements, custom air bellows with:
- Enhanced metallic bead plates for high-pressure environments.
- Elastomers tailored to the operating temperature range.
can significantly improve performance. Custom designs allow air bellows to meet unique application needs, ensuring reliability even under the most extreme conditions.
Height Control Systems
Integrating automatic height control valves ensures consistent performance despite temperature-related pressure changes. This is especially crucial in applications with alternating loads. These systems optimize performance by maintaining a stable operating height, even when external conditions fluctuate. Height control is particularly valuable in automotive and industrial settings, where precision and stability are essential.
Air bellows are highly adaptable, capable of functioning in extreme temperatures when designed and maintained properly. By selecting appropriate materials, maintaining correct pressure levels, and implementing regular inspections, their reliability in harsh conditions can be guaranteed. As experts in the field, we provide solutions that ensure optimal performance, whether in cold storage facilities, high-temperature industrial plants, or automotive applications.