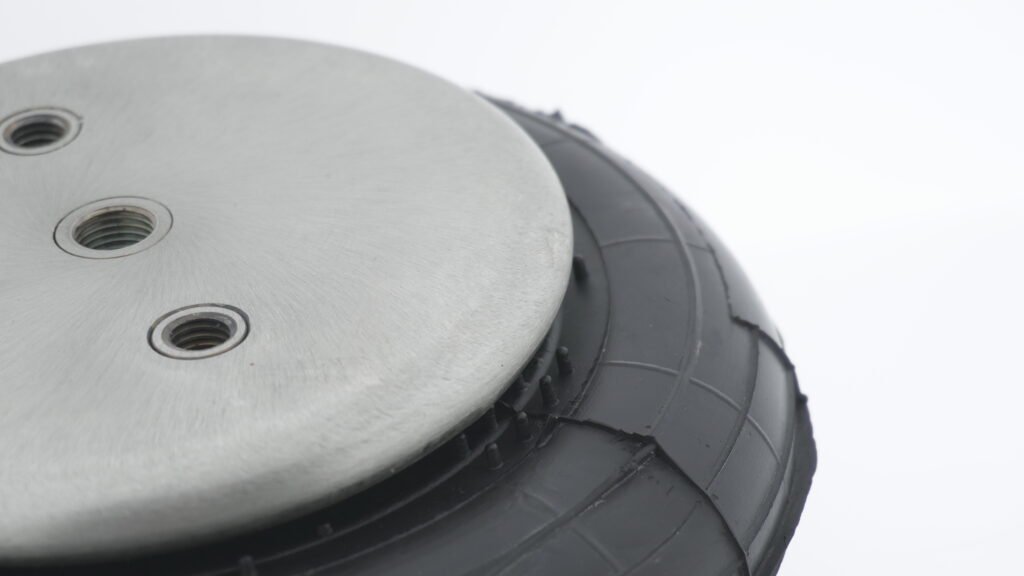
Optimizing Wind Turbine Performance with Advanced Vibration Isolation
Wind turbines are complex structures that must withstand mechanical stress, extreme weather conditions, and dynamic loads. One of the key challenges in wind turbine operation is vibration isolation, which plays a crucial role in prolonging the lifespan of components and ensuring optimal efficiency. The proper damping of vibrations enhances the stability of the turbine structure, preventing excessive fatigue in materials. Air bellows offer a highly effective solution by isolating vibrations, preventing damage to sensitive components, and optimizing energy production. These components work by absorbing and dissipating vibrational energy, reducing mechanical wear and extending the turbine’s operational life. Unlike traditional isolation systems, air bellows provide adjustable stiffness, ensuring adaptability to different wind conditions. By integrating air bellows, operators achieve a stable and efficient power generation system, minimizing downtimes and maintenance costs while improving overall performance.
Why Vibration Isolation Matters in Wind Turbines
Vibrations in wind turbines arise from multiple sources, including aerodynamic forces, gearbox interactions, and structural resonances. Unchecked vibrations lead to increased stress on turbine parts, accelerating mechanical wear and reducing efficiency. Structural integrity is crucial for wind turbine longevity. If left unchecked, vibrations may weaken tower structures and foundations, resulting in costly repairs and operational downtime. Effective vibration isolation prevents energy losses, ensuring optimal mechanical performance and increasing the turbine’s lifespan. By implementing air bellows, wind turbine operators mitigate excessive vibrations and enhance structural stability. With the ability to reduce component fatigue, air bellows serve as an essential part of modern turbine technology. Their integration helps decrease maintenance costs, improves gearbox performance, and minimizes failures. When wind turbines operate smoothly, energy output remains consistent, reducing long-term operational expenses and maximizing sustainability.
How Air Bellows Improve Vibration Damping
Air bellows, also known as pneumatic isolators, provide superior damping characteristics due to their ability to effectively absorb and dissipate vibrational energy. Their high elasticity allows them to flex under variable loads without losing efficiency. Natural frequency stabilization ensures turbines remain operational even under fluctuating wind speeds. Unlike conventional coil springs, air bellows are not susceptible to metal fatigue. This results in longer service life, requiring less maintenance compared to alternative isolation methods. The constant damping properties of air bellows ensure steady performance over time, reducing failures. Additionally, their high flexibility allows them to adapt to load variations, ensuring consistent vibration isolation even in extreme weather conditions. By adjusting internal air pressure, air bellows allow operators to fine-tune vibration isolation to specific turbine requirements. The combination of maintenance-free operation and long-lasting durability makes air bellows an ideal choice for wind energy applications.
Key Features of Air Bellows for Wind Turbines
High Load-Bearing Capacity
Wind turbine applications require isolators capable of supporting static and dynamic loads. Air bellows handle forces up to 380 kN per unit, making them ideal for supporting nacelles, gearboxes, and tower bases. The use of multi-layer reinforced rubber and steel components ensures maximum stability and strength. Their structural resilience allows them to withstand extreme mechanical loads without deformation. By incorporating air bellows, turbines maintain structural integrity, reducing the risk of mechanical failures. Their performance remains unaffected by high wind speeds, ensuring long-term operational reliability.
Adjustable Stiffness and Damping
The stiffness of air bellows can be adjusted by modifying internal air pressure, allowing for customizable solutions. Operating pressure ranges from 0.5 to 12 bar, with high-pressure configurations available for larger turbines. Adjustability ensures that optimal damping levels are maintained even under changing wind conditions. Load adaptability prevents excessive oscillations, improving stability and reducing vibration-induced failures. By fine-tuning stiffness, turbine operators achieve greater control over vibration damping, maximizing mechanical efficiency while minimizing energy loss.
Superior Environmental Resistance
Constructed from high-quality elastomers, air bellows withstand extreme environmental conditions. Their durability ensures they remain unaffected by ozone exposure, moisture, and corrosive agents. The materials used include:
- Natural rubber (NR/SBR) – Flexible, durable, and resistant to mechanical fatigue (-40°C to +70°C).
- Chlorobutyl (CIIR) – Acid-resistant, ideal for offshore applications (-30°C to +115°C).
- Nitrile rubber (NBR) – Oil and fuel-resistant (-25°C to +110°C).
- EPDM rubber – High resistance to ozone and UV exposure (-20°C to +115°C).
These materials ensure long-lasting performance, even in harsh operating conditions, extending the reliability of wind turbine systems.
Compact Design for Easy Integration
Air bellows feature a low-profile design, allowing seamless integration into turbine structures. With diameters ranging from 80 mm to 950 mm, they accommodate different turbine configurations. Their lightweight construction makes installation straightforward while maintaining optimal load distribution. Air bellows efficiently isolate vibrations without requiring extensive design modifications.