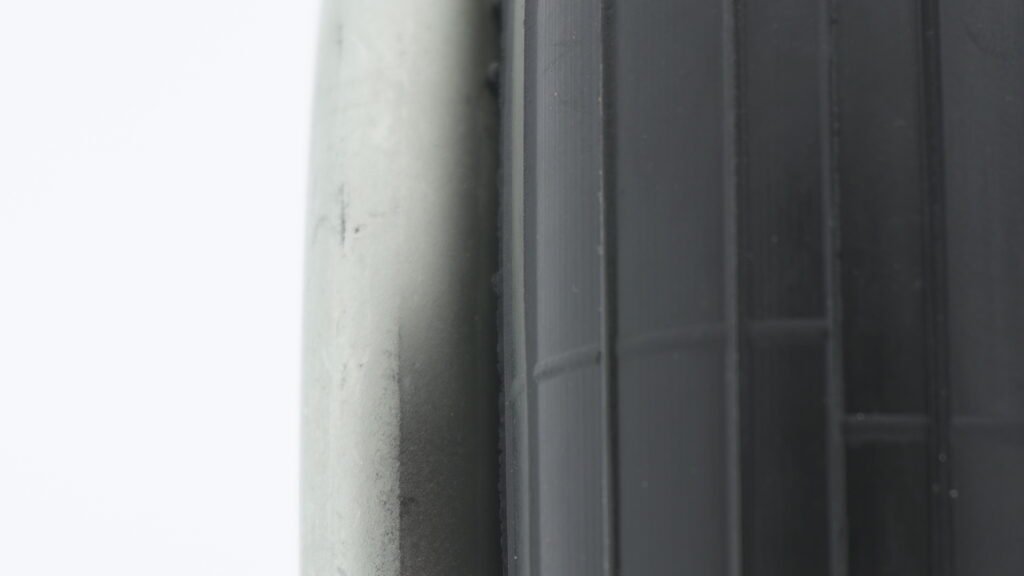
Enhancing Durability and Performance in Industrial Applications
Air bellows have undergone significant advancements in elastomer technology, leading to enhanced durability, resistance, and performance in various industrial applications. With the integration of high-strength elastomers, modern air bellows offer superior load-bearing capacity, chemical resistance, and operational efficiency. These innovations improve performance, making them essential for critical systems requiring high reliability.
Elastomer-based air bellows support higher pressures, increasing their ability to withstand harsh environments. The ability to handle extreme temperatures and chemical exposure ensures a longer service life. Modern air bellows also offer greater flexibility, allowing smooth operation under variable loads.
These improvements enhance cost-effectiveness, reducing maintenance needs and operational downtime. By utilizing advanced elastomer materials, manufacturers ensure optimal efficiency, making air bellows indispensable in engineering applications.
Innovations in Elastomer Formulations
The latest elastomer compounds used in air bellows include specialized blends of natural rubber (NR/SBR), chlorobutyl (CIIR), nitrile rubber (NBR), ethylene propylene diene monomer (EPDM), and chloroprene (CR). These formulations provide a balance of flexibility, mechanical strength, and temperature resistance.
- Natural Rubber (NR/SBR): Offers high dynamic capability, making it suitable for high-frequency applications. It provides excellent elasticity, allowing better shock absorption.
- Chlorobutyl (CIIR): Provides excellent acid resistance, ensuring longevity in chemical environments. It remains stable under high humidity.
- Nitrile Rubber (NBR): Delivers outstanding oil resistance, making it ideal for hydraulic applications. It resists fuel degradation effectively.
- EPDM: Excels in ozone resistance, extending operational lifespan in outdoor environments. It also withstands extreme heat.
- Chloroprene (CR): Features weather-resistant properties, reducing degradation over time. It provides excellent abrasion resistance.
Increased Load Capacity and Pressure Resistance
Through advanced reinforcement techniques, air bellows now support higher loads and increased internal pressure. The introduction of four-ply construction enhances their strength, allowing some models to operate at pressures up to 12 bar, compared to the traditional 8 bar limit.
Key Benefits of High-Performance Air Bellows
- Extended Service Life: Resistance to abrasion, ozone, and UV exposure extends their usage time.
- Optimized Weight Distribution: Improved load-bearing efficiency reduces structural strain, enhancing system performance.
- Superior Vibration Isolation: Absorbs over 99% of vibrations, minimizing wear and tear on machinery.
- Enhanced Flexibility: Maintains uniform movement, preventing stick-slip effects for smoother operations.
Improved Manufacturing Techniques
Recent manufacturing advancements ensure precision engineering, creating air bellows with optimized sealing mechanisms and reinforced bead rings. These innovations include:
- Crimped Designs: Provide a leak-proof structure, increasing durability and enhancing pressure stability.
- Bead Ring Constructions: Offer easy installation, making them ideal for modular systems.
- Multi-Convolution Structures: Enhance stroke capabilities, improving performance in variable-load conditions.
By refining manufacturing techniques, engineers have improved consistency, material integrity, and assembly efficiency. This results in cost reductions and better quality control.
Applications in Modern Industries
The adaptability of air bellows makes them indispensable in sectors requiring precise force control and vibration isolation. Key industries benefiting from these advancements include:
- Rail Transport: Provides shock absorption, ensuring passenger safety in dynamic environments.
- Manufacturing: Enhances precision machinery stability, reducing wear on components.
- Aerospace: Used for actuation systems in landing gears and aerodynamic controls.
- Energy Sector: Supports turbine vibration control, improving energy efficiency and operational safety.
Future Trends in Elastomer Technology
The future of air bellows technology is driven by eco-friendly elastomers, self-healing materials, and smart monitoring systems. The integration of embedded sensors will allow real-time condition monitoring, ensuring predictive maintenance and longer service life.
By focusing on sustainable materials, manufacturers aim to reduce environmental impact while improving product longevity. These advancements will lead to smarter, more adaptive air bellow solutions.
The continuous evolution of elastomer technology in air bellows is revolutionizing industrial applications. Enhanced durability, higher pressure resistance, and superior flexibility make these components essential in modern engineering solutions. As materials science advances, future air bellows will become even more efficient, sustainable, and intelligent.
By leveraging high-performance elastomers, manufacturers continue to develop air bellows that provide greater reliability, longer lifespan, and reduced maintenance requirements.