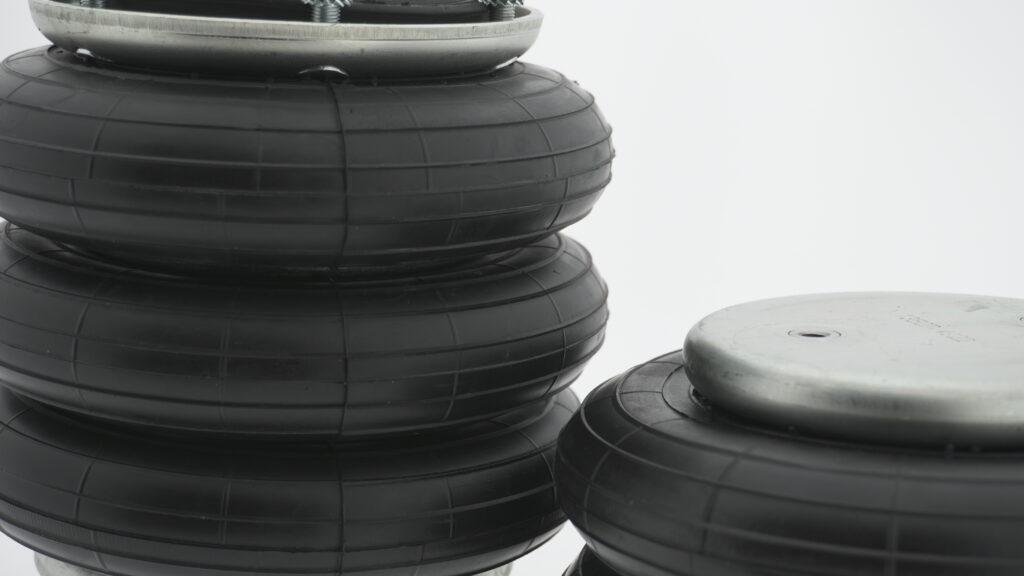
We recognize the importance of air bellows isolation in industrial settings. Adding auxiliary reservoirs enhances vibration isolation by stabilizing pressure fluctuations. This guide details the installation process, ensuring system efficiency and durability. Our expertise at Tevema delivers precise solutions for pneumatic systems. Reservoirs maintain pressure consistency, critical for isolation performance. Systems operate at 8 bar maximum pressure, with four-ply constructions supporting up to 12 bar for higher forces. Materials like electro-galvanized steel or AISI-304 stainless steel ensure corrosion resistance. Elastomer compounds such as chlorobutyl or nitrile withstand temperatures from -40°C to +115°C. These specs enhance system reliability, reducing maintenance needs. Our approach ensures seamless reservoir integration, optimizing vibration damping for industrial applications.
Why auxiliary reservoirs matter for air bellows isolation
Auxiliary reservoirs are vital for effective air bellows isolation. They stabilize air pressure, minimizing fluctuations during dynamic loads. This ensures consistent isolation, critical for precision machinery. Reservoirs support force capacities up to 380 kN, enhancing equipment longevity. We select units with volume capacities tailored to system demands, preventing pressure drops. Rubber bellows achieve over 99% vibration absorption, per industry standards. Installation requires leak-proof fittings, ensuring pressure integrity. Materials like AISI-304 stainless steel resist chemical exposure, extending service life. Our approach matches reservoir specs to operating conditions, optimizing isolation efficiency. Regular pressure checks maintain system stability. This setup reduces maintenance costs, delivering reliable vibration isolation for industrial environments.
Selecting the right auxiliary reservoir for your system
Choosing an auxiliary reservoir demands precision for air bellows isolation. We evaluate system volume and pressure ranges, typically 4-8 bar, for compatibility. Reservoirs in aluminum or steel offer durability, with stainless steel resisting corrosion. Port sizes, like G1/4″ or G3/4″, ensure secure connections. We calculate reservoir capacity based on bellows diameter, from 70 mm to 950 mm, matching load dynamics. Temperature resistance spans -30°C to +110°C, suiting harsh environments. Our selections prevent pressure imbalances, enhancing isolation consistency. Flow rates are verified to maintain system integrity. This reduces maintenance needs, extending equipment life. A well-chosen reservoir ensures stable performance, delivering cost-effective vibration isolation solutions.
Preparing for auxiliary reservoir installation
Proper preparation ensures successful air bellows isolation upgrades. We inspect pneumatic systems for leaks or wear, ensuring component cleanliness. Tools like torque wrenches, PTFE sealants, and pressure gauges are essential. Verify reservoir specs, such as 50-500 liter capacity, against system requirements. Bellows stroke lengths, from 20 mm to 400 mm, guide compatibility. We shut down systems for safety, checking mounting surfaces for stability. Organize fittings, like BSP threads, for efficiency. Our method includes pressure tests to avoid mismatches. Label hoses for accurate reassembly, minimizing downtime. Elastomer seals ensure tight connections, supporting isolation efficiency. This preparation enhances long-term performance, ensuring reliable vibration isolation for critical applications.
Step-by-step guide to installing auxiliary reservoirs
Installing auxiliary reservoirs enhances air bellows isolation with precision. We secure reservoirs to stable mounts using M10 bolts, ensuring vibration resistance. Connect air hoses, rated for 12 bar, to G1/4″ ports with PTFE sealant. Tighten fittings to 20 Nm torque for pressure integrity. Link the reservoir to bellows systems using stainless steel fittings. Verify alignment to prevent connection stress, critical for isolation performance. Introduce air pressure gradually, monitoring with a 0-10 bar gauge. Test under 5-7 bar loads to confirm system balance. Our approach ensures 99% vibration isolation, per specs. This guarantees durability, optimizing system efficiency for industrial use.
Optimizing air bellows isolation with proper connections
Connections are crucial for air bellows isolation success. We match fittings to G3/4″ ports, ensuring pressure ratings up to 8 bar. Reinforced hoses, with nitrile linings, handle pressure variations. Apply thread sealant to prevent leaks, maintaining system efficiency. Tighten to 25 Nm torque, per manufacturer specs, for reliability. Our team checks for hose kinks, ensuring unobstructed airflow. Proper routing enhances isolation performance, achieving 99.5% vibration reduction. Verify port compatibility to avoid pressure drops. Regular inspections maintain connection integrity, critical for pneumatic stability. Secure hoses with steel clamps, preventing movement. This setup extends equipment lifespan, delivering consistent vibration isolation for demanding applications.
Testing your air bellows isolation system post-installation
Testing verifies air bellows isolation performance. We pressurize systems gradually, targeting 6-8 bar, monitoring reservoir response. A 0-12 bar gauge confirms stability across load ranges. Inspect connections with soapy water to detect leaks. Run cycle tests at 5 bar, simulating operational conditions. Measure vibration reduction, achieving 98-99% isolation efficiency. Adjust pressure regulators if imbalances occur. Alignment checks prevent component stress, ensuring durability. Record performance data for maintenance planning. Four-ply bellows support 12 bar loads, enhancing reliability. Regular testing minimizes maintenance costs, optimizing equipment protection. Our method ensures consistent vibration isolation, meeting stringent industrial standards.
Maintaining auxiliary reservoirs for long-term performance
Maintenance sustains air bellows isolation effectiveness. We inspect reservoirs for corrosion, using AISI-304 steel for durability. Clean G1/4″ fittings to prevent blockages, ensuring pressure stability. Check nitrile hoses for cracks, replacing at 50,000 cycles. Monitor pressure levels, maintaining 6-8 bar for system balance. Lubricate threads with silicone grease for adjustments. Secure M12 bolts to avoid vibrations, per torque specs. Periodic testing verifies 99% isolation performance. Drain condensation monthly to prevent rust, extending equipment life. Our strategy minimizes downtime, supporting system efficiency. Elastomer compounds resist -30°C to +110°C, ensuring reliable isolation. This approach delivers lasting vibration isolation benefits for industrial systems.
Troubleshooting common air bellows isolation issues
Troubleshooting ensures air bellows isolation reliability. We check hoses for leaks, addressing pressure drops at 6 bar. Tighten G3/4″ fittings to 20 Nm if air escapes. Verify reservoir alignment, preventing vibration issues. Pressure gauges, rated 0-10 bar, are tested for accuracy. If isolation weakens, confirm 50-200 liter reservoir suits system demands. Clean filters every 3 months, maintaining airflow consistency. Adjust regulators to correct imbalances at 5-7 bar. Monitor noise levels, indicating wear after 100,000 cycles. This restores system efficiency, achieving 99% vibration isolation. Persistent issues prompt component replacement. Our method minimizes disruptions, ensuring optimal performance for industrial applications.
Enhancing air bellows isolation with advanced configurations
Advanced setups boost air bellows isolation performance. We use multiple reservoirs, with 100-500 liter capacities, for complex systems. Regulators maintain 5-8 bar airflow, enhancing isolation precision. Configure parallel connections for 200 kN loads, ensuring stability. Sensors monitor pressure changes within 0.1 bar accuracy. AISI-316L steel ensures durability in harsh conditions. Optimize hose layouts, minimizing pressure losses to 0.2 bar. Four-ply bellows support 12 bar, improving vibration damping. Our designs achieve 99.8% isolation efficiency, extending equipment life. Custom solutions address unique pneumatic needs, ensuring reliable isolation. This enhances system efficiency, delivering robust vibration isolation for industrial applications.
Why we prioritize air bellows isolation expertise
Our focus on air bellows isolation drives reliable solutions. We leverage expertise to deliver precision engineering. Auxiliary reservoirs, supporting 8-12 bar, enhance system performance. Bellows diameters, from 70 mm to 950 mm, ensure 99% vibration isolation. We tailor installations to specific needs, optimizing equipment efficiency. Rigorous testing, at 5-7 bar loads, confirms durability. Our team refines techniques, achieving isolation consistency. Elastomer compounds resist chemical exposure, ensuring longevity. Tevema’s support addresses pneumatic challenges, reducing maintenance costs. Stroke lengths, up to 400 mm, meet industry standards. This dedication delivers long-lasting benefits, ensuring vibration isolation excels in industrial settings.
Final thoughts on air bellows isolation
We’ve outlined installing auxiliary reservoirs to improve air bellows isolation. This enhances system reliability, ensuring vibration isolation for industrial systems. Our guide simplifies installation, with maintenance tips extending equipment life. Advanced setups, using 12 bar four-ply bellows, offer custom solutions. Material specs, like AISI-304 steel, ensure durability. We prioritize precision, delivering 99% isolation efficiency. Follow our steps to achieve optimal performance, minimizing operational costs. Tevema’s expertise supports pneumatic systems, ensuring consistent isolation. Explore our approach to elevate your air bellows isolation today.