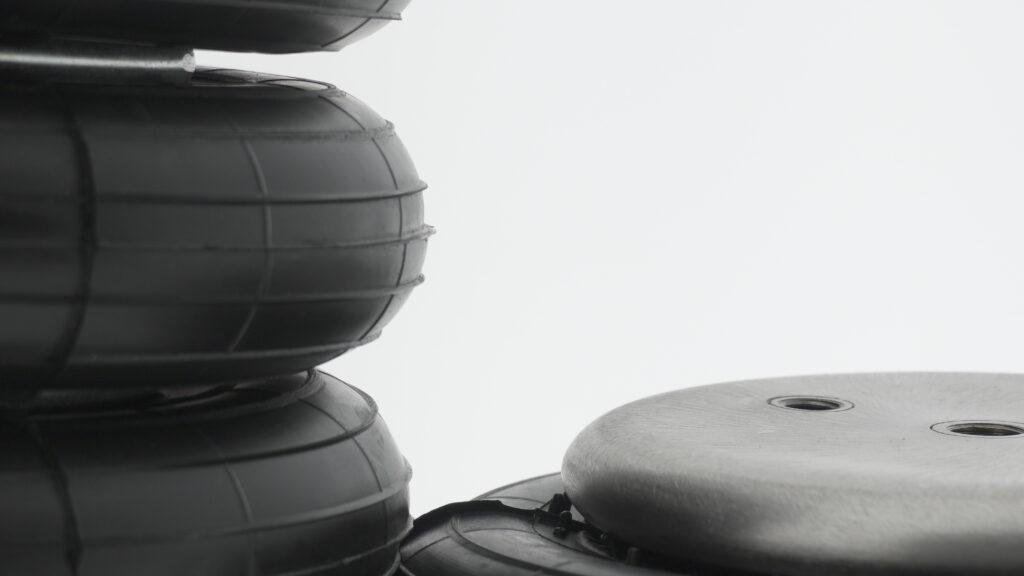
Integrating precise temperature management into air springs temperature regulation greatly enhances performance, reliability, and lifespan. Temperature fluctuations directly influence the internal stiffness and operational efficiency of air springs, potentially causing premature material degradation. By stabilizing internal temperatures, variations in structural integrity and load-bearing capacity are significantly reduced. Air springs typically include advanced elastomers like chlorobutyl, offering excellent resistance to acids and temperatures from -30ºC to +115°C. High-quality materials prevent excessive thermal stresses on internal fabric reinforcements and metallic parts, ensuring consistent long-term operation. Precise temperature regulation also minimizes internal friction, reducing heat-related wear and extending overall product life. Controlled thermal conditions enable consistent performance of air springs in demanding industrial applications. Incorporating integrated temperature regulation becomes crucial for maintaining high operational standards, optimizing efficiency, preventing unexpected downtimes, enhancing industrial productivity, and ensuring equipment safety under varying temperature conditions.
Importance of temperature control
Effective temperature management is essential for optimal functionality in air springs temperature regulation across industrial applications. Internal temperature stability significantly affects actuator precision and isolator performance, maintaining consistent load-bearing capacities and predictable response characteristics. Without accurate temperature regulation, operational variations cause decreased efficiency, rapid fatigue, and potential structural failures. Stabilizing temperatures within precise operational ranges supports uniform isolation properties and consistent natural frequencies regardless of load fluctuations. This stability significantly contributes to extended machinery life by reducing thermal degradation risks to sensitive internal components. Regulated temperatures allow air springs to reliably handle extreme hot and cold environments without performance loss. Properly managed thermal conditions within air springs protect critical materials, ensuring optimal functional longevity and enhanced safety standards. Effective temperature control directly correlates to improved productivity, minimized maintenance requirements, and sustained reliability in diverse industrial operations, highlighting the necessity of precise internal temperature management for air springs.
Advanced elastomer materials
Our air springs temperature regulation systems leverage specialized elastomer materials tailored to specific temperature and chemical environments. Natural rubber (NR/SBR) elastomers provide exceptional dynamic performance within temperature ranges of -40°C to +70°C, suited for general industrial applications. For demanding environments involving higher temperatures or chemical exposures, ethylene propylene diene monomer (EPDM) elastomers are preferred, operating effectively between -20°C and +115°C. Nitrile (NBR) elastomers demonstrate superior resistance to oils and fuels, maintaining properties from -25°C to +110°C, ideal for oil-rich industrial contexts. Conversely, chloroprene (CR) elastomers excel due to outstanding weathering resistance and moderate oil compatibility within temperatures of -20°C to +110°C. Elastomer choice significantly impacts durability, reliability, and functional performance, making it critical to match material properties precisely to operational temperature challenges. Appropriate elastomer selection enhances air spring robustness, ensuring optimal service life under demanding environmental conditions, and minimizing risks associated with thermal degradation.
Metallic components resistance
Durability of metallic components in air springs temperature regulation directly influences long-term operational performance and reliability. Typically, standard metallic parts consist of electro-galvanized steel, providing sufficient corrosion protection for moderate environmental conditions. However, demanding industrial scenarios necessitate superior materials, such as stainless steel grades AISI-304 and AISI-316L, recognized for excellent resistance to temperature extremes and harsh chemical exposures. These stainless steel types significantly reduce corrosion risk and thermal expansion, preserving structural stability and dimensional accuracy under varying thermal stresses. Employing stainless steel components enhances overall durability, reducing maintenance frequency and lifecycle costs associated with replacements. Further, these advanced metallic materials withstand prolonged exposure to chemicals, moisture, and fluctuating temperatures without performance degradation. Optimal selection of metallic materials is thus crucial, ensuring sustained performance, reliability, and structural integrity of air springs across diverse temperature-sensitive industrial applications, contributing directly to extended operational life and reduced long-term maintenance expenditures.
Four-ply high-strength construction
Specialized four-ply high-strength construction enhances the reliability of air springs temperature regulation, particularly for applications requiring higher operational pressures. This robust design supports increased operating pressures up to 12 bar, significantly surpassing the standard limit of 8 bar. Enhanced construction involves additional reinforcing fabric layers strategically positioned between elastomeric layers, substantially increasing resistance to mechanical deformation and thermal stresses. Structural reinforcement effectively maintains dimensional stability and pressure consistency under high-load, high-temperature operational conditions. The additional ply layers minimize deformation, providing stable height control, predictable stroke lengths, and reliable force outputs. Such robust construction extends air spring durability, minimizes maintenance requirements, and enhances safety margins, crucial for industrial operations under extreme demands. Employing high-strength designs enables air springs to reliably manage elevated temperature and pressure conditions, significantly improving industrial productivity, equipment reliability, overall system longevity, and operational safety, thereby proving indispensable for industrial applications subjected to challenging environmental stresses.
Working media considerations
Selecting appropriate working media is crucial for reliable operation of air springs temperature regulation across diverse industrial environments. Typically designed for compressed air, air springs may effectively function with alternative media such as nitrogen, oil, or water. Each medium interacts uniquely with internal materials and temperature conditions, influencing performance, durability, and maintenance needs. Nitrogen offers stable internal pressure maintenance across temperature extremes, ensuring consistent operational performance and predictable characteristics. Oil-based media reduce internal friction and heat generation, providing beneficial lubrication particularly suited to intensive industrial operations with high-cycle frequencies. Conversely, employing water necessitates careful selection of stainless steel components due to potential corrosion risks, especially under elevated temperature conditions. Proper media choice optimizes performance, enhances equipment longevity, and mitigates risks associated with thermal degradation or corrosion. Therefore, understanding and selecting suitable working media becomes fundamental for maximizing reliability, operational efficiency, and longevity of air springs under varying temperature and environmental conditions.
Operational benefits
Implementing air springs temperature regulation yields substantial operational advantages, significantly enhancing equipment efficiency, reliability, and durability. Stable internal temperature management ensures precise height control, consistent actuator performance, and uniform movements, effectively eliminating stick-slip issues common in conventional actuators. Precision enables accurate vibration isolation, significantly reducing structurally transmitted noise and enhancing operational comfort within industrial environments. Integrated temperature regulation supports compact installation designs, allowing tighter machinery integration without compromising performance integrity or reliability. Maintaining stable internal thermal conditions substantially extends air spring lifespan, reducing maintenance frequency, operational downtime, and associated long-term costs. Precise temperature regulation facilitates predictable and reliable air spring operation across various environmental conditions, optimizing industrial productivity and equipment performance. Ultimately, incorporating temperature control capabilities directly contributes to increased operational safety, reduced costs, enhanced efficiency, and sustained reliability, establishing temperature management as critical for industrial applications demanding consistent high-performance standards and rigorous operational dependability.