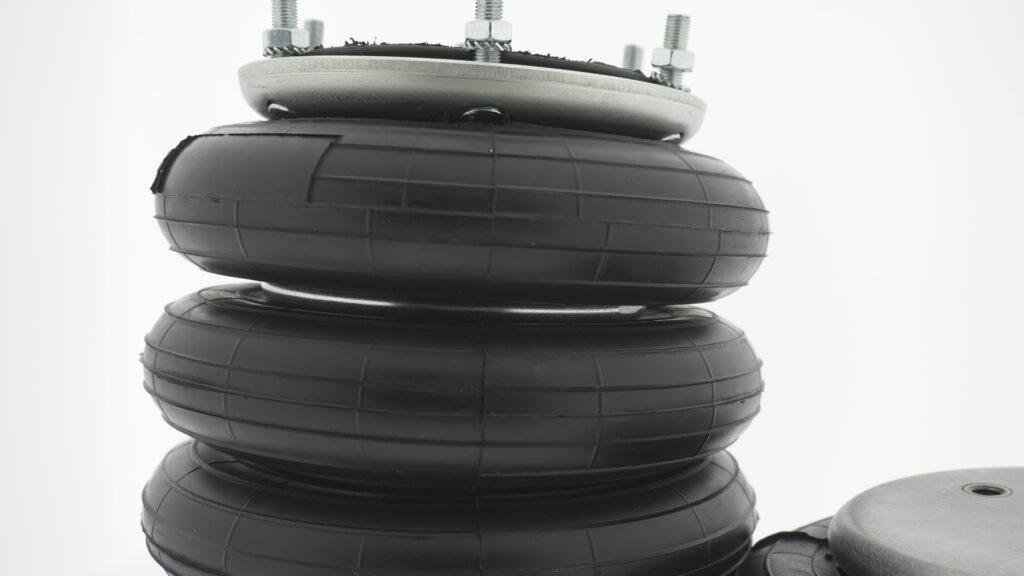
In advanced automation systems, air bellows play a vital role in improving motion control precision. We rely on rubber actuators with flexible construction to absorb vibration, support tilting motion, and maintain consistent alignment under load. This provides better performance for machinery that operates in highly dynamic environments. As motion varies, compressed air can be modulated to adjust stroke length and load resistance, offering real-time adaptability. The multi-convolution bellows construction ensures compactness while delivering powerful thrust and low natural frequency. This makes them ideal for repetitive motions, where precision and wear resistance are essential. Our bellows are engineered with vulcanized rubber layers, reinforced with fabric plies, and sealed with mechanical closures. Depending on design, supported diameters range from small to large-scale industrial formats, handling heavy-duty applications. We leverage this to improve dynamic positioning, shock absorption, and control response across a wide spectrum of industrial environments.
Low natural frequency improves accuracy and control
The low natural frequency of air bellows is essential to enhance motion control in vibration-sensitive systems. By isolating machinery from vibrations, we prevent misalignment, component fatigue, and inaccurate positioning. This isolation capability enables systems to operate more accurately, even under fluctuating loads or during rapid cycles. Our designs absorb over 99% of unwanted vibrations, outperforming coil springs or hydraulic isolators. Unlike rigid actuators, rubber bellows inherently dampen noise and reduce harmonic distortions. This leads to quieter and smoother operation. The damping capability ensures sensitive instruments stay calibrated, which is crucial in precision automation. Our bellows operate in a low-frequency spectrum, specifically tuned to match dynamic response requirements in complex systems. This ability to maintain consistent performance across varying inputs makes them ideal for feedback-driven applications. We achieve superior motion correction by integrating bellows into robotic arms, pressing devices, and other high-speed automation setups.
Enhanced stroke length flexibility for adaptable systems
We design our air bellows to provide enhanced stroke length flexibility, which is key in modern automation systems. With variable convolution counts—single, double, or triple—our bellows offer controlled and customizable movement ranges. Our use of compressed air as the working medium allows quick adjustments to force and travel without complex mechanisms. This makes our solutions ideal for systems that require adjustable actuation under varying conditions. The design height and diameter options allow compact integration into space-limited assemblies. We ensure that stroke variability doesn’t compromise performance or cause misalignment, thanks to internal reinforcements. The bellows accommodate lateral displacement and tilt without mechanical damage. Units support angular motion and limited lateral flexibility without introducing excess stress. This helps operators maintain consistent outputs across different cycles and product formats. Our engineering approach ensures smooth actuation and efficient energy transfer in all supported configurations.
Uniform force output under fluctuating pressure
Our air bellows are engineered to deliver uniform force output across fluctuating air pressure levels. This consistency is vital in applications where load conditions change rapidly. Traditional hydraulic or pneumatic cylinders often suffer from internal friction or wear, which affects their output reliability. In contrast, our rubber-based actuators provide stable force curves over time. The internal structure—comprising reinforced rubber layers and sealed closures—ensures even air distribution throughout the system. Our bellows are compatible with low to moderate pressure ranges and may include enhanced-layer constructions for more demanding use. Such stability is crucial for automated machinery, where every cycle must follow precise parameters. With accurate pressure modulation, we support real-time force adjustments and achieve higher levels of operational control. Our systems adapt seamlessly to dynamic requirements while preventing jerking, overextension, or incomplete cycles, ensuring reliable long-term operation.
Compact design supports modern machinery layouts
Modern automation setups often face space constraints, which we solve using the compact design of our air bellows. Unlike traditional actuators, our bellows maintain a low installation height while offering equivalent or greater motion range. This allows system designers to place actuators in tight enclosures or under mobile assemblies. Despite the smaller footprint, our bellows maintain strong axial thrust capabilities, making them efficient for high-load applications. The reduced size does not compromise stability or durability, as our elastomer compounds withstand wear, ozone, and chemical exposure. Our bellows are tested to function in extreme temperatures depending on the material type. By using mechanically fixed or bolted closures, we achieve a sealed and rugged structure with minimal maintenance needs. We’ve eliminated sliding parts that could otherwise introduce friction or degradation. The result is a compact, high-performance solution that supports demanding automation architectures.
Vibration isolation improves equipment longevity
We utilize the vibration isolation capabilities of our air bellows to extend equipment life and maintain consistent operation. Continuous exposure to vibration can lead to early component failure, calibration drift, and excessive noise. Our bellows isolate over 99% of structural vibrations, offering superior protection for sensitive assemblies. Their response characteristics are engineered to prevent resonance buildup and to mitigate disruptive oscillation. The rubber’s damping behavior also reduces impact shock during machine cycles. This means less wear on moving parts and more stable system behavior under cyclic loads. The consistent natural frequency response ensures that resonance doesn’t build up, which could otherwise damage internal parts. By minimizing transmitted vibration, our bellows also reduce the need for auxiliary dampers or support structures. Each unit is built with carefully calculated wall geometry and convolution profile to withstand dynamic loading conditions without structural fatigue or deformation.
Easy integration with various mounting systems
Integration versatility is key to why engineers prefer our air bellows in automation. We offer multiple end closure designs to ensure compatibility with diverse mounting setups. These range from integrated mounting plates to modular designs that support horizontal or vertical assembly. Bellows can be configured to fit a wide array of standard air inlet and fastening formats. Each unit includes anchoring options that simplify attachment to frames, tables, or platforms. Whether mounted on aluminum, steel, or corrosion-resistant alloy parts, our sealing configurations maintain system integrity under repetitive cycles. The modularity of our solutions makes them easy to scale or reposition based on production demands. With minimal tooling required, our bellows accelerate installation while reducing setup errors. This mounting adaptability also allows our bellows to serve both vertical and horizontal motions, offering broader engineering application without the need for redesigning support structures.
High durability in demanding environments
Our air bellows demonstrate outstanding durability in harsh industrial environments, where extreme conditions are the norm. We offer multiple elastomer options such as natural rubber, EPDM, nitrile, and chlorobutyl to handle temperature, ozone, oil, and chemical exposure. These materials perform reliably between -40°C and +115°C. Combined with corrosion-resistant metallic parts, our bellows maintain structural integrity in high-pressure or wet conditions. For applications requiring added strength, we offer designs with enhanced reinforcement capable of withstanding elevated force and pressure loads. This ensures long-term functionality even under cyclic or peak-load stresses. All units are tested to resist fatigue, cracking, and delamination under expected service cycles. By minimizing the risk of failure, we ensure consistent uptime in critical systems. Our sealing technology also prevents air leakage, ensuring performance retention across the full range of usage conditions. This durability translates into longer service intervals and reduced maintenance demand.
Final thoughts on improving automation precision
Through precision engineering, advanced materials, and smart design, our air bellows significantly enhance motion control in automation systems. Their flexibility, adaptability, and durability allow engineers to develop high-performance machinery with confidence. We address multiple challenges in automation—from space limitations to vibration mitigation—through one integrated solution. Whether optimizing stroke control, vibration isolation, or compact layout, our bellows consistently outperform rigid actuators. We maintain strict production standards, ensuring each unit delivers reliable performance across varying loads and environments. With numerous size configurations and mounting options, we offer tailored solutions for virtually any setup. Our approach simplifies both design and maintenance, enabling cost savings without sacrificing functionality. By prioritizing consistent performance, ease of use, and environmental resilience, we help businesses meet increasing automation demands. Choosing our air bellows means choosing reliability and technical excellence across every detail, without compromising system integrity or efficiency.