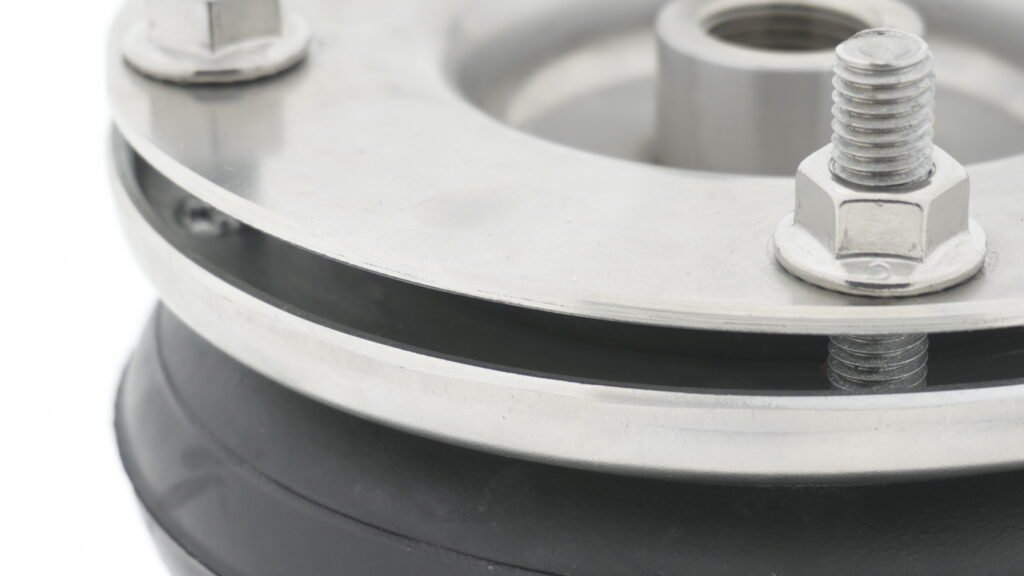
Enhancing Safety with Air Bellows in Mining
Mining operations demand robust, reliable, and safe equipment to mitigate risks and ensure efficient performance. One of the most effective solutions for vibration isolation, shock absorption, and load stabilization in mining equipment is the use of air bellows. These durable and high-performance components significantly reduce equipment failure, enhance operator safety, and improve mining efficiency. Air bellows have a maximum pressure rating of 8 to 12 bar, depending on the construction type. They are made from reinforced elastomers and corrosion-resistant metal components to withstand harsh mining conditions. Additionally, they have a stroke length ranging from 50 mm to 400 mm, allowing for optimal load balancing. The flexible design enables custom mounting configurations, making them suitable for various mining applications. These specifications demonstrate why air bellows are the preferred choice for mining safety solutions.
Air Bellows as Shock Absorbers in Harsh Environments
Mining environments are rugged, with intense vibrations, heavy loads, and constant exposure to dust, moisture, and chemicals. Air bellows provide a superior shock absorption mechanism, protecting both machinery and personnel from excessive vibrations and mechanical failures. Compared to coil springs, air bellows offer greater flexibility and customizable load handling, making them the preferred choice for mining vehicles and vibration-sensitive equipment. The rubber compounds used in air bellows include natural rubber (NR/SBR), nitrile (NBR), and EPDM, offering resistance to oil, ozone, and extreme temperatures. These properties ensure long-term durability in mining applications. The maximum load capacity of air bellows varies from 0.5 kN to 450 kN, depending on the size and design. The ability to withstand repetitive impact forces makes them highly effective for mining vehicle suspensions, drill rig damping systems, and conveyor belt vibration reduction.
Vibration Isolation for Critical Mining Equipment
Excessive vibrations from drilling rigs, conveyor systems, and underground transport vehicles can cause accelerated wear, structural damage, and increased maintenance costs. Air bellows act as a primary vibration isolator, significantly reducing transmitted vibrations, thereby enhancing operational stability and reducing maintenance downtime. The result is a safer working environment and extended equipment lifespan. Air bellows maintain a natural frequency range of 1.5 to 3 Hz, ensuring optimal vibration isolation. The internal air volume can be adjusted to fine-tune damping characteristics, making them adaptable to different load conditions. Studies show that air bellows can reduce vibration transmission by up to 99%, minimizing operator fatigue and mechanical wear. Their low maintenance and high resilience make them a cost-effective solution for improving mine safety and efficiency.
Load Balancing and Height Control in Mining Vehicles
Mining vehicles such as loaders, haulers, and excavators operate under variable loads, making height control essential for stability and safety. Air bellows provide precise height adjustment by adjusting air pressure, ensuring optimal balance and even load distribution. This improves maneuverability, reduces tire wear, and enhances fuel efficiency—critical factors for cost-effective mining operations. The design height of air bellows ranges from 60 mm to 400 mm, allowing integration with various mining vehicles. Height adjustments can be achieved within milliseconds, ensuring real-time load balancing. Mining trucks equipped with air bellows have demonstrated 20% improved fuel efficiency due to optimized weight distribution. Their ability to compensate for uneven terrain provides better vehicle stability, reducing the risk of tipping accidents. The long service life of air bellows makes them a valuable investment in modern mining fleets.
Dust and Corrosion Resistance in Air Bellows
The mining industry operates in dust-laden and high-moisture conditions that can severely impact mechanical components. Unlike traditional metal springs, air bellows are constructed with reinforced elastomers and corrosion-resistant materials, making them highly resistant to abrasion, moisture, and chemical exposure. This durability translates to longer operational life and lower replacement costs. Standard air bellows are available with AISI-304 stainless steel or electro-galvanized steel end closures, ensuring extended resistance to rust and wear. For extreme conditions, AISI-316L stainless steel options are available. Lab tests confirm that air bellows maintain full functionality even after 10 million load cycles in abrasive environments. Their ability to withstand extreme temperatures, from -40°C to +115°C, ensures reliable performance in all mining conditions. These features make air bellows a highly dependable component for underground and surface mining operations.
Maintenance-Free Operation for Continuous Mining
Downtime in mining operations is costly, making maintenance-free solutions essential. Air bellows require minimal upkeep compared to hydraulic actuators or metallic springs. Their self-contained design eliminates lubrication needs, ensuring consistent performance over extended periods. This reduces operational costs while improving workplace safety. The average lifespan of air bellows is 10 to 15 years, depending on usage intensity. Unlike pneumatic cylinders, air bellows do not have friction seals, eliminating the risk of air leakage. Their modular design allows for easy replacements, ensuring quick installation. Mining companies report a 40% reduction in maintenance expenses after switching to air bellows-based systems. The high reliability and low failure rate make them the preferred choice for continuous mining operations, preventing unexpected shutdowns and maximizing productivity.
Mining safety and efficiency are paramount concerns, and air bellows have revolutionized the industry by offering unmatched vibration control, shock absorption, and load stabilization. By integrating air bellows into mining operations, companies can achieve higher safety standards, longer equipment lifespan, and reduced operational costs, ensuring a sustainable and productive mining environment. Air bellows have proven to be an essential component in modern mining equipment, offering exceptional performance in harsh environments. Their ability to reduce vibrations, maintain load balance, and provide corrosion resistance makes them the most effective solution for mining applications.