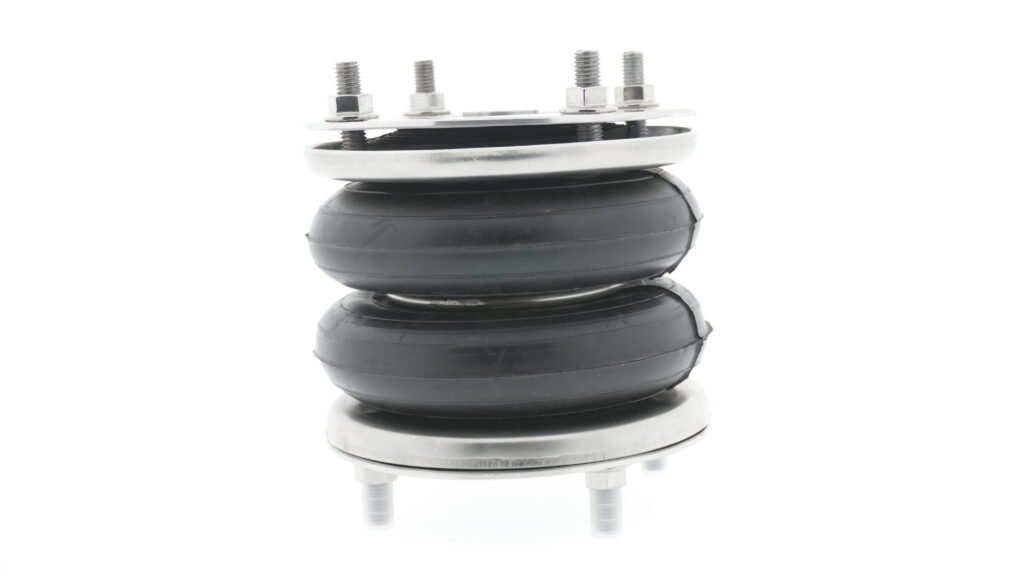
Optimizing Industrial Efficiency with Air Bellows
In modern manufacturing, energy consumption is a critical concern. Factories require efficient solutions to minimize costs and enhance sustainability. Air bellows offer a high-performance alternative to traditional actuators, reducing energy waste and optimizing production. They provide high force output with low air pressure, making them energy-efficient and cost-effective. Their flexible rubber structure allows them to absorb vibrations and compensate for misalignment, reducing mechanical stress on equipment. This increases machine lifespan and lowers maintenance costs. The reinforced elastomers used in air bellows ensure durability and resistance to extreme temperatures, making them suitable for harsh industrial environments. Standard air bellows can handle pressures up to 8 bar, while four-ply versions operate at 12 bar, delivering higher efficiency. Their low-friction design reduces energy loss, improving overall factory performance and operational sustainability.
How Air Bellows Improve Energy Efficiency
1. Reduced Friction and Wear
Unlike hydraulic cylinders, air bellows operate without sliding seals, reducing mechanical friction and energy loss. Their non-metallic construction extends lifespan and minimizes wear-related failures. Air bellows use high-strength rubber compounds, reinforced with textile plies to withstand repeated flexing without degradation. The bead ring design ensures a secure seal, preventing air leaks and maintaining consistent performance. Friction reduction leads to lower operational temperatures, preventing premature material fatigue. This results in better efficiency and reduced downtime, as less frequent maintenance is needed. The reduced wear also decreases air consumption, as the bellows maintain optimal pressure levels without excessive leakage. The combination of low friction, high durability, and efficient air retention allows factories to cut energy costs significantly, ensuring sustainable operations.
2. Minimal Air Leakage
Air bellows have a sealed design, ensuring low air consumption. This results in better energy conservation than traditional pneumatic cylinders. The bead ring mounting system improves sealing integrity, reducing leakage rates even under high pressure. Standard single-convolution bellows retain 98% of input air, ensuring minimal waste. The multi-layered rubber composition enhances sealing performance, preventing leaks even with continuous compression cycles. The precision-molded air inlets are designed for high-pressure retention, reducing energy loss from misfitting connections. Factories utilizing air bellows see a notable decrease in compressed air demand, leading to lower energy consumption. Additionally, the lightweight construction of air bellows reduces the power required for actuation, contributing to improved efficiency. These factors make air bellows a superior choice for applications requiring sustained air pressure with minimal losses.
3. High Force-to-Energy Ratio
Air bellows generate large forces with minimal air pressure. Their unique convoluted structure maximizes energy efficiency by converting compressed air into mechanical motion with minimal loss. A single-convolution bellow produces up to 40 kN of force at 7 bar pressure, while a triple-convolution version reaches up to 75 kN. Their high-load capacity makes them ideal for industrial presses, lifting platforms, and vibration isolation. The four-ply reinforced models allow operation at higher pressures, further increasing force output while maintaining low air consumption. Compared to hydraulic actuators, air bellows require 60% less energy to achieve the same force levels. The flexible rubber construction prevents overloading, ensuring smooth and efficient operation. Their ability to deliver force efficiently makes them a cost-effective and energy-saving solution for heavy-duty applications.
Industrial Applications of Air Bellows
1. Vibration Isolation in Heavy Machinery
Factories rely on air bellows to isolate vibrations from presses, motors, and other high-impact machinery. Their ability to absorb vibrations improves machine longevity and reduces energy costs. A typical air isolator achieves a 99% vibration reduction at 6 bar pressure, significantly improving equipment performance. The low-frequency response prevents resonance effects, ensuring stable machine operation. Air bellows effectively dampen impact forces, preventing mechanical stress buildup that could lead to component failure. Their versatile mounting options allow for easy integration into existing machine structures, optimizing vibration control with minimal modifications.
2. Automated Material Handling
Many factories use air bellows for lifting platforms and automated transport systems. Their smooth, uniform motion ensures precision while using less energy than hydraulic alternatives. Double-convolution bellows provide higher stroke lengths, reaching up to 400 mm extension at full pressure. Their adjustable height control allows seamless integration into conveyor systems, ensuring accurate positioning. The low air consumption of these systems makes them ideal for continuous operations, reducing energy expenditure over time.
3. Pressing and Forming Applications
Air bellows play a crucial role in pressing machines, providing consistent force distribution with minimal energy input. This makes them ideal for stamping, molding, and clamping processes. A standard industrial bellow exerts up to 100 kN of force, ensuring uniform pressure application. Their flexible design eliminates mechanical wear, improving equipment durability. Lower energy consumption and precise force control make them an economical solution for high-volume production lines.
Incorporating air bellows into factory operations significantly reduces energy consumption, improves efficiency, and lowers costs. Their durability, minimal maintenance, and environmental benefits make them a superior alternative to traditional hydraulic and pneumatic systems. By optimizing air pressure, selecting the right models, and integrating efficient automation, factories can achieve maximum energy savings. With force capacities ranging from 10 kN to 450 kN, air bellows provide a scalable solution for various industrial applications. The ability to function at lower pressures, while maintaining high force outputs, ensures long-term operational cost savings.